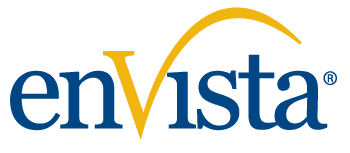
- 877-684-7700
- Inventory Optimization

Supply Chain Systems
Retail systems, it managed services, microsoft application management, design build services, material handling, robotics integration, warehouse control systems, slam line automation.
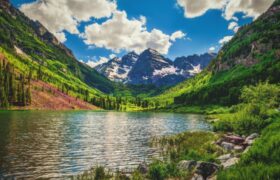
Big Rock Sports Implements New WMS for Greater Efficiency and Scalability
Big Rock Sports leverages enVista’s WMS implementation services to improve inventory and picking accuracy and lower labor costs.
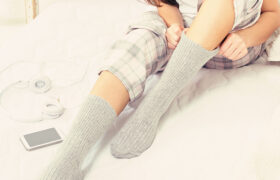
Leading Sock and Legwear Designer and Manufacturer Improves S&OP Strategy Program
Sock and legwear manufacturer reduces inventory costs and significantly improves service levels with enVista’s S&OP strategy program.
Distribution
Manufacturing
Third-Party Logistics
Private Equity
Food & Beverage
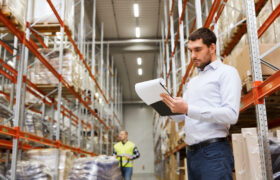
Hidden Treasures of Advanced Warehousing
Make the most of Microsoft Dynamics 365’s Advanced Warehousing module and gain insight into the hidden treasures to unlock value.
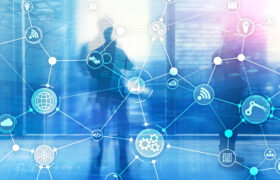
What Is Supply Chain Execution and How Can Supply Chain Execution Software Help Your Company?
Learn about supply chain execution and how supply chain execution software can help your company streamline processes and lower costs.
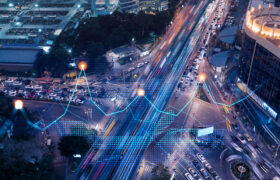
Get Rates Right: How You Need to Think About Strategic and Tactical Sourcing
Gain insight into strategic vs. tactical sourcing and how placing transportation procurement into these categories can reduce the complexity.
- Company Overview
Associate Experience
Client Experience
Community Impact
- Honors & Awards
Home > 4 Warehouse Management System Case Studies
4 Warehouse Management System Case Studies
- July 23, 2020
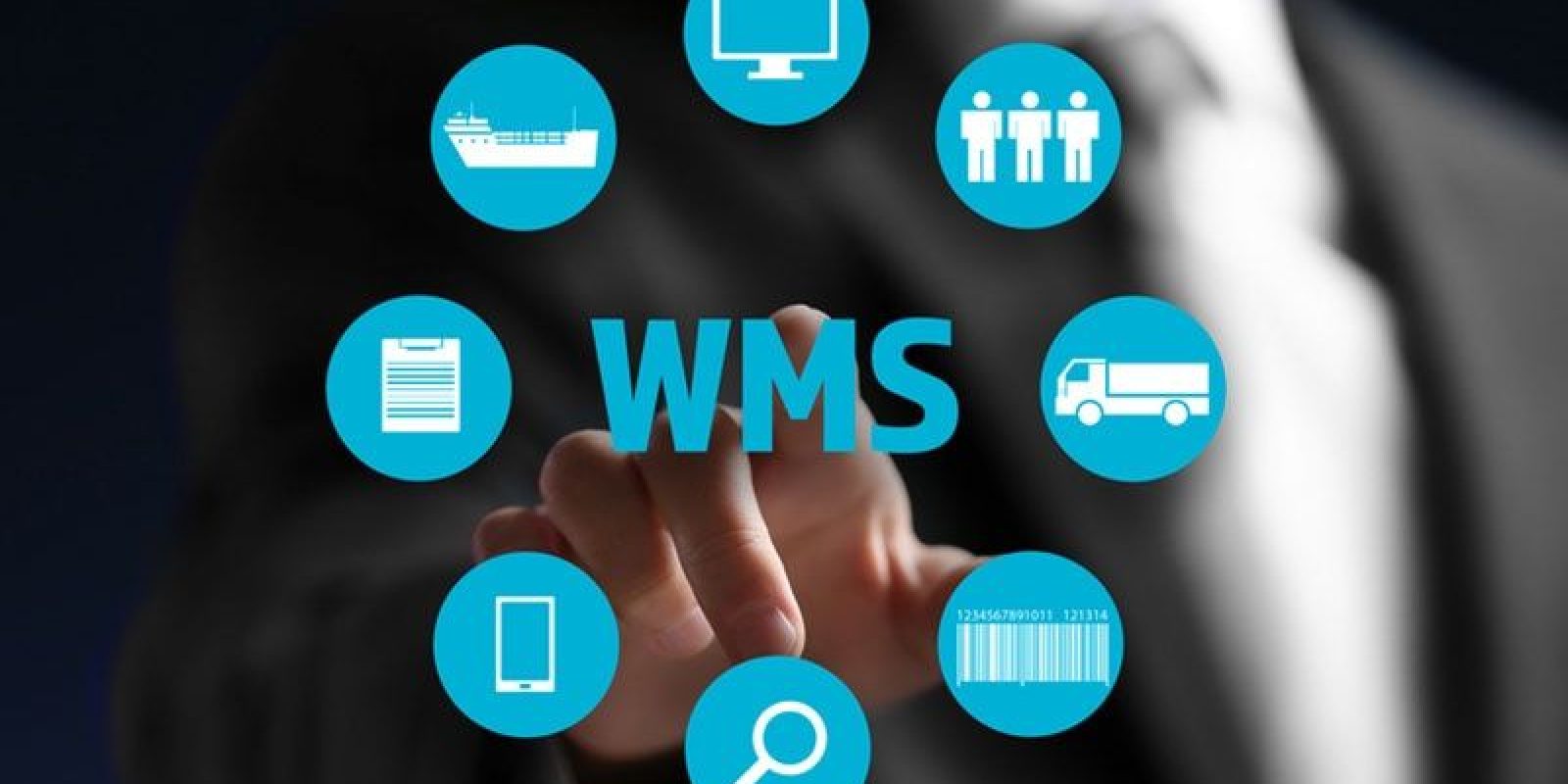
Successful WMS Implementation Case Studies
Warehouse Management Systems (WMS) represent a major investment in your supply chain and operational efficiency. While it can be difficult to gauge your estimated time to value, these four cases featuring enVista clients provide a warehouse management system business case and showcase outcomes after successful WMS implementations.
In this post, we’ll cover four examples of WMS implementations and how they helped companies to optimize warehouse operations :
- Nature’s Best
- Performance Bike
- Bradshaw International
- Men’s Wearhouse
Four WMS Implementation Examples
1. nature’s best.
*Note: Since project completion, Nature’s Best has been acquired by KeHE.*
Leading the market of health and natural foods distribution, Nature’s Best serves Certified Organic products in over twelve states. Nature’s Best was experiencing high labor costs based on time and manpower to transport temperature-controlled food products between four buildings on its DC campus. The company’s zones were organized to suit either small or large clients – a key competitive differentiator. Because of the facility layout, the overall distribution process was inefficient; each product was touched 18 times on its way to the customer. Nature’s Best technology, distribution processes and buildings also needed updating to keep pace with growth projections.
enVista was called upon to address and resolve the challenges Nature’s Best was facing and did so using its consult, implement and operate (CIO) methodology to create a customized solution.
Phase One: Consult
A supply chain strategy that met Nature’s Best’s business goals was developed. enVista conducted a material flow analysis and redesigned the internal flow processes to increase efficiencies. As a result, a global WMS was selected that addressed all of Nature’s Best’s concerns and determined construction needs for the distribution center (DC). Operations would be consolidated to one DC, and enVista designed the new facility with various temperature-controlled zones.
Phase Two: Implement
As Nature’s Best began construction, enVista supervised the integration and implemented a Manhattan Associates WMS including interface design, configuration, training, facility preparation and labor standards among other features. Nature’s Best shifted from a mechanized to non-mechanized system and from paper to radio-frequency (RF) devices with voice-based technology. enVista managed the move of $25 million of inventory and trained the company team on new system processes.
Phase Three: Operate
During go-live, enVista ensured a seamless transition into Nature’s Best new facility, systems and processes. Throughout the Consult, Implement, and Operate phases, sales were steady – even growing – and upon completion, the project was delivered on time and within budget. The chosen system required few modifications for Nature’s Best’s business model, which would lower costs and allow for easier upgrades in the future.
The new system reduced labor costs by over 30 percent and more than doubled productivity. Ninety-seven percent of full-time employees were retained, and temporary and non-value-added positions were eliminated. Nature’s Best went consultant-free only four weeks after go-live.
Download Nature’s Best Case Study
Example 2: Performance Bike
Performance Bike is a privately-held, specialty retailer focused on bicycles and accessories. The company had expanded to over 110 retail locations since its founding in 1982. Performance Bike had a DC in Chapel Hill, NC, with over 60 associates and partners with a 3PL in Long Beach, CA.
Due to compliance issues with the U.S. Postal Service barcodes, Performance Bike had to make system changes to its Manhattan PkMS WMS. The company’s experience with Manhattan Associates gave it a flexible approach when considering an upgrade. enVista’s enABLE methodology was used for the upgrade, and many of the roles typically filled by software or consulting companies were completed by Performance Bike.
Because of the prior experience and flexibility of Performance Bike and enVista, the WMS implementation was under budget and on time. Team members from both enVista and Performance Bike worked together to complete and implement the WMS. The vice president of warehouse operations for Performance Bike noted enVista’s customer-centric approach and flexibility.
The WMS upgrade was implemented in less than 6 months. There were very minor changes to the user experience, so trainings were seamless and increased productivity. Performance Bike experienced a pick per hour increase of 50 to 100 units per hour, exceeding the company’s executives’ expectations.
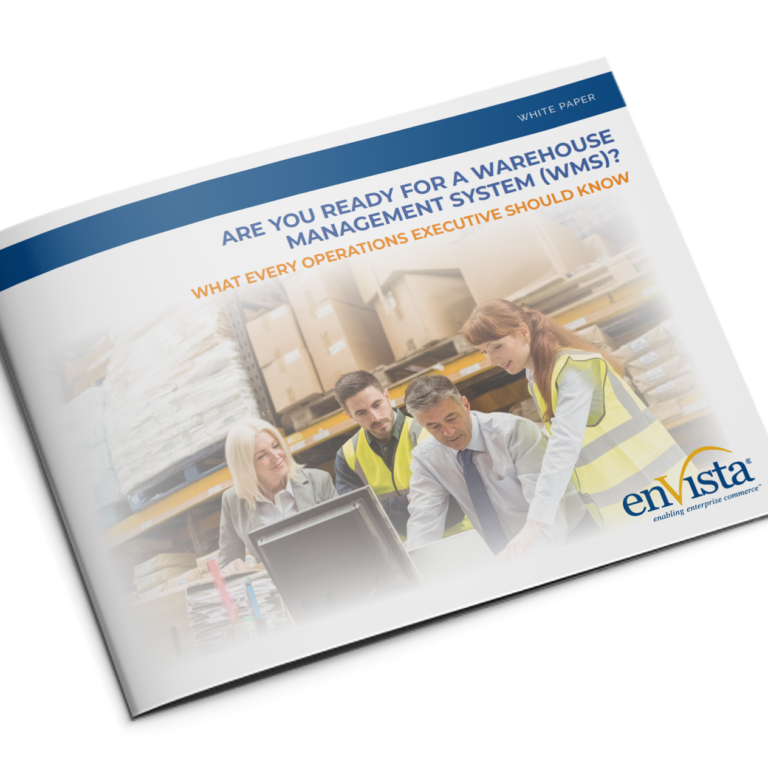
Are you Ready for a Warehouse Management System?
Discover what every operations executive should know about selecting a WMS to ensure a positive ROI, and improved operations.
Example 3: Bradshaw International
Bradshaw International’s Good Cook™ brand is sold in over 30,000 U.S. retail stores. Bradshaw is a leading marketer of kitchenware products and launched Good Cook to incorporate quality, value and service into every product. This philosophy has allowed Good Cook to achieve the best position for kitchen tools and gadgets with 43 percent of the market.
Bradshaw was asked to participate in Wal-Mart’s direct store delivery consolidation (DSDC) program as Good Cook is distributed in the stores. The program was designed to allow shippers to directly replenish Wal-Mart stores in less-than-case-pack quantities. To do so, Bradshaw had to make changes to several parts of its current distribution systems.
Changes to electric data interchange (EDI), order management, and a pick/pack operation integrated with a new WMS would be required to handle the new variable volumes. enVista was asked to help design and integrate the DSDC program. To meet Walmart’s DSDC objectives, the team had to design and build a new pick/pack module, select the technology to be used by the picking team, and integrate it with the WMS. The order management software , EDI software and billing system had to be modified to accommodate the structures required by Walmart’s DSDC program.
The team profiled SKU movements, identified pick and storage mediums to model replenishment rates, and formulated labor plans and proper work flows. Bradshaw IT and enVista worked together to make configuration changes to the RedPrairie WMS and integrate it with the Pick from Light System and EDI software. The joint team also specified data maps from order capture to order management to WMS through EDI transmissions to move the infrastructure to industry standards.
With enVista’s help, Bradshaw successfully integrated the DSDC program into operations. Shipping volumes increased beyond expectations, but the new WMS has allowed Bradshaw to keep up with demand. The program was implemented with almost no customer disruption.
Example 4: Men’s Wearhouse
Founded in 1973, Men’s Wearhouse is one of the country’s largest specialty retailers of men’s apparel with over 700 stores. The stores carry a full selection of high-end men’s clothing and accessories.
Men’s Warehouse’s main DC was a 1.1-million square foot facility in Houston, Texas. It is the core retail distribution center for Men’s Warehouse retail stores, as well as 60 percent of merchandise from K&G Retail stores, acquired in 1999. A significant percentage of its garment-on-hanger merchandise is shipped by dedicated fleet to regional hubs across the country. enVista’s main objective was to consolidate retail and e-commerce systems to run all operations on a single platform and a central material handling equipment (MHE) integration point.
enVista acted as the program management role for supply chain execution and MHE software functions for all facilities. The implementation of the new systems platform occurred in two distinct phases.
The first phase focused on using the new systems platform to more efficiently meet Men’s Wearhouse’s growing e-commerce business needs. A new WMS and distributed order management system were implemented and integrated to an e-commerce web platform. These systems allowed strategic decision making regarding e-commerce order fulfillment and room for growth, along with the accuracy and flexibility necessary for seamless execution and delivery.
Phase two focused on implementing the new WMS and a consolidated warehouse control system (WCS) in Men’s Wearhouse’s Retail Distribution Operation. The WMS replaced the retailer’s legacy system, and the WCS consolidated the management of several operations into one system. Men’s Wearhouse now has the ability to dynamically change product flow, unit allocation, and achieve more effective utilization of Case Level ASN receiving with the new WMS. The system’s ability to recognize and execute on cross-docking opportunities created improved throughput and lower overall processing costs.
With the implementation of a common WMS and standardized processes, Men’s Wearhouse was able to share recourses across operations and respond to seasonal increases in workload more effectively. The implementation of WMS and WCS gives the company the ability to consolidate its distinct Men’s Wearhouse and K&G distribution operations to reduce costs and increase overall processing efficiency.
Download Men’s Wearhouse Case Study
Conclusion: enVista’s WMS Expertise
Getting your WMS right and making sure it’s integrated properly across your supply chain technology stack is critical to realizing quick ROI and improved operational efficiencies.
enVista has completed hundreds of WMS implementation projects in its nearly two decades of experience, and our vendor agnostic approach to consulting and implementation ensures you get objective help for your most critical projects. We’re passionate about supply chains and delivering solutions that are the right fit for our clients and would love to help you optimize your supply chain.
If you have a WMS project on the horizon or want to learn more about how we can help you, let’s have a conversation .
About the Author
enVista Thought Leadership
Related posts.
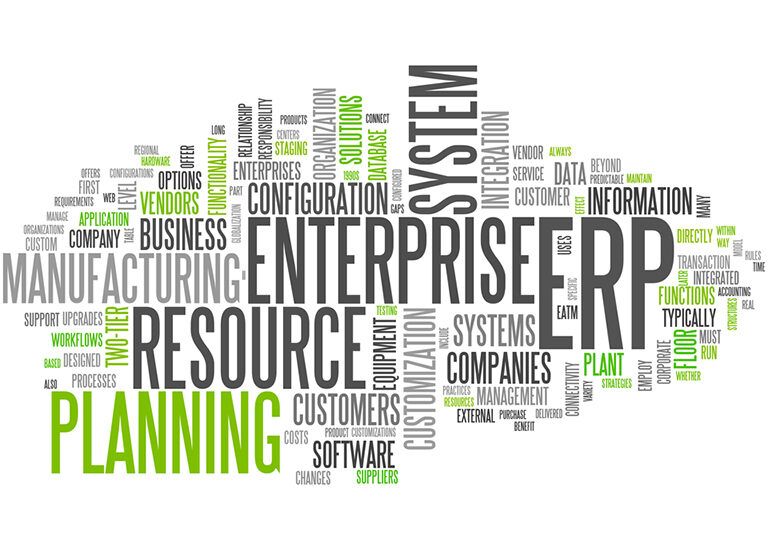
Why Supply Chain Management Features are Crucial for an ERP System
Bridging the gap between an ERP system and supply chain management allows businesses to maximize IT dollars and resources.
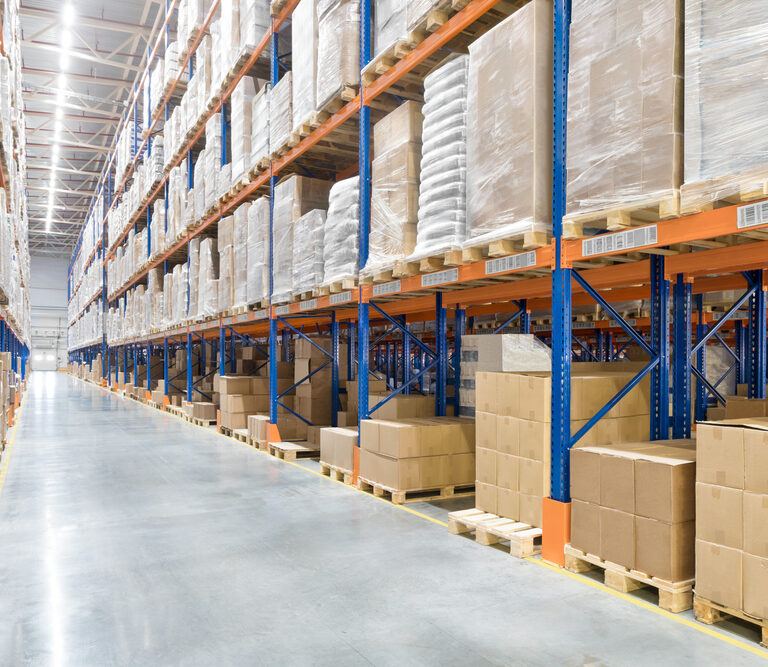
Increase ROI Through Successful Warehouse Slotting
A well-thought-out slotting strategy also enables businesses to minimize wasted space and maximize storage capacity within the warehouse. Increase ROI using the right tools, strategy and management plan with successful warehouse slotting.
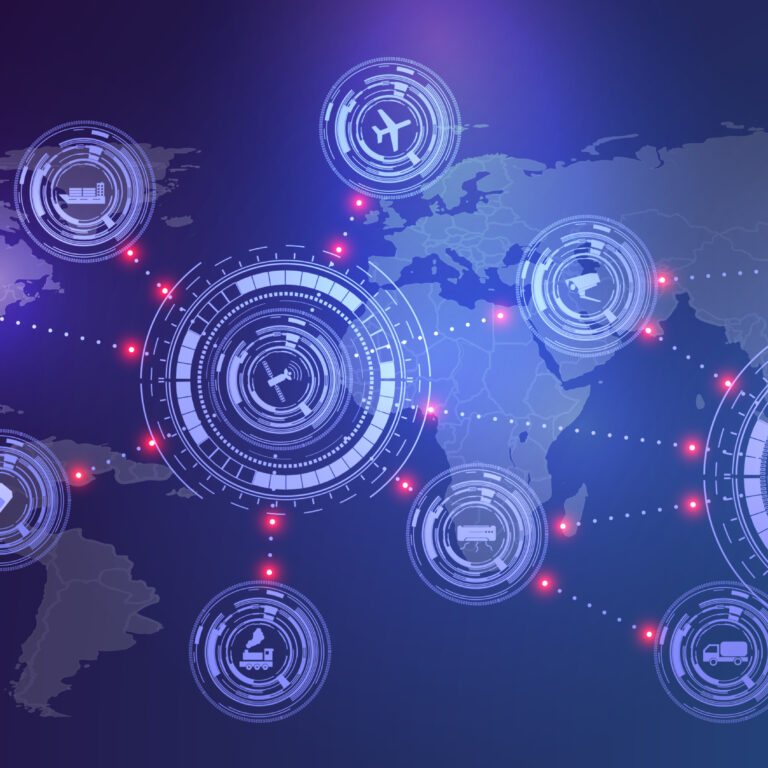
The Cost-Saving Power of Artificial Intelligence in Supply Chains
There are endless tactical opportunities for leveraging AI in your supply chain operations to increase efficiency, profitability and customer service levels. Beginning your AI journey within the areas of the supply chain that are costing your organization the most – network design, inventory and warehousing – will multiply your cost savings.
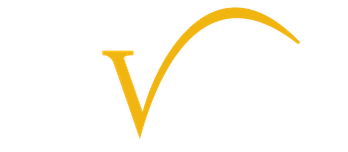
Subscribe to Our Insights
Why envista.
- Diversity, Equity, & Inclusion
About enVista
- Cookie Policy
- Privacy Policy
- Privacy Notice for CA Residents
- Terms of Use
We support your right to privacy and transparency about how we collect and use your personal data.
Privacy overview, contact envista.
- Bahasa Indonesia
- Sign out of AWS Builder ID
- AWS Management Console
- Account Settings
- Billing & Cost Management
- Security Credentials
- AWS Personal Health Dashboard
- Support Center
- Expert Help
- Knowledge Center
- AWS Support Overview
- AWS re:Post
Amazon Adopts Amazon Aurora for Inventory Database
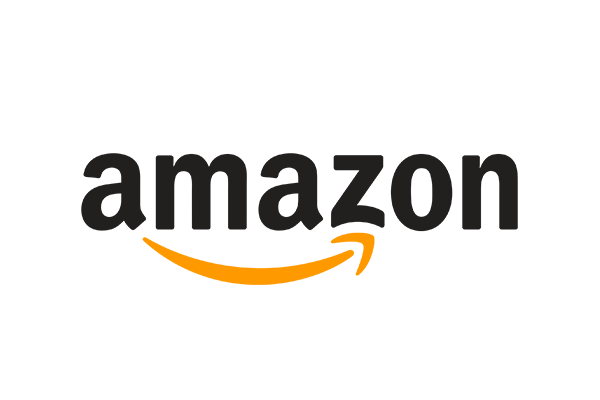
Choosing the Cloud
In May 2017, AFT decided to migrate the system to Amazon Aurora . A MySQL- and PostgreSQL-compatible database built for the cloud, Aurora provides the performance and availability of Oracle at approximately one-tenth the cost. Amazon Aurora is fully managed by Amazon Relational Database Service (Amazon RDS), which automates time-consuming administration tasks such as hardware provisioning, database setup, patching, and backups.
PostgreSQL was selected as the database because it could handle complex write transactions at speeds comparable to the Oracle system. “Our writes have a lot of components,” says Michael Wu, principal software development engineer at Amazon. “They include things like location, current state, and financial operations. The PostgreSQL-compatible edition of Amazon Aurora offers high performance for these scenarios.”
High-Stakes Migration, Managed
Once Amazon Aurora was selected, the team began planning the migration. AFT took a replatforming approach, preserving existing service architectures and database schemas to minimize complexity and disruption. Replatforming allowed more than 200 external services to migrate their dependencies with minor code changes.
Automation was essential to enabling such a large-scale migration. “Manual deployment simply wouldn’t work,” says Wu. “We wanted to migrate as quickly as possible by building mechanisms that would allow teams to manage the migration effectively.”
AWS Database Migration Service was used to migrate data from the Oracle databases to the PostgreSQL databases running on Amazon Aurora. Thanks to the modular nature of AWS, it took a team averaging three engineers only three months to complete the automation framework.
Because of the need for always-on operations in the fulfillment centers, the downtime window for the migration in each center was only two hours. Thanks to the automation built in the first stage, the team maintained a 100 percent migration success rate. “It’s always challenging to migrate a large system in a short time frame, but with AWS Database Migration Service, we were able to far exceed the initial expectations,” says Anthony Girolamo, senior software development manager at Amazon.
Keeping Up with Business Growth
The elastic capacity of preconfigured database hosts on AWS eliminated much of the administrative overhead required to scale the system. The transformation has been significant. “In the Oracle world, a seemingly simple change such as scaling from a medium to a large database instance required provisioning hardware, standing up primary and standby databases, and managing failover during transitions, which could take a full day for each instance,” says Bigonger. “Not to mention the fact that we were using specialized hardware that had to be ordered months in advance. After migrating to Amazon Aurora, provisioning additional capacity is achieved through a few simple mouse clicks or API calls.” The scaling effort has been reduced by as much as 95 percent.
High availability is another key benefit of Amazon Aurora. “Previously, if we lost a piece of hardware, it would impact our ability to maintain redundancy for up to a day,” says Bigonger. “With Amazon Aurora, reprovisioning happens automatically in just minutes, ensuring data is always fully protected.”
With the performance of Amazon Aurora, the team is no longer limited by the input/output operations the database instance can handle. “During the process, we shed software ‘technical debt,’ making our software systems better and enabling greater agility,” says Wu. “Our engineers can kickstart projects by spinning up their own test instances whenever they need to. It took the complexity out of the process.”
Migrating IMS to Amazon Aurora resulted in a range of benefits—the most important of which is dependable fulfillment for customers. “Using Amazon Aurora, we can keep up with Amazon’s business growth,” says Girolamo. “That means customers get products faster—which is why we do what we do.”
More Amazon Stories
Amazon's cloud journey on aws.
Amazon.com migrated 5,000 databases from Oracle to AWS, cutting its annual database operating costs by more than half and reducing the latency of most critical services by 40 percent. The company leverages Amazon DynamoDB to scale Prime Video and Amazon SageMaker to indentify misplaced inventory.
Learn more »
How Amazon is Achieving Database Freedom Using AWS
Migrating to AWS has cut Amazon's annual database operating costs by more than half. Database-administration and hardware-management overhead have been greatly reduced, and cost allocation across teams is much simpler than before.
Amazon.com Case Study
Amazon.com is the world's largest online retailer. In 2011, Amazon.com switched from tape backup to using cloud-based Amazon S3 for backing up the majority of its Oracle databases. By using AWS, Amazon.com was able to eliminate backup software and experienced a 12X performance improvement, reducing restore time from around 15 hours to 2.5 hours in select scenarios.
Amazon Reduces Infrastructure Costs on Visual Bin Inspection by a Projected 40% Using Amazon SageMaker
Amazon Fulfillment Technologies migrated from a legacy custom solution for identifying misplaced inventory to Amazon SageMaker, reducing AWS infrastructure costs by a projected 40 percent per month and simplifying its architecture.
Amazon Prime Video Uses AWS to Deliver Solid Streaming Experience to More Than 18 Million Football Fans
Amazon Video selected AWS Elemental, an AWS company that combines deep video expertise with the power and scale of the cloud to empower media companies to deliver premium video experiences to consumers.
Prime Video Boosts Scale and Resilience Using Amazon DynamoDB
As part of its strategy to build a platform that could scale to meet projected needs for at least 10 years, Amazon decided to migrate Prime Video to AWS. The migration would replace CQS with a suite of 12 microservices, built using a range of AWS services that included Amazon DynamoDB, AWS Lambda, and Amazon Simple Queue Service (Amazon SQS).
Amazon Robotics Uses Amazon SageMaker to Enable ML Inferencing at Scale
Amazon Robotics developed a sophisticated machine learning model using Amazon SageMaker to streamline inventory management, halving inferencing costs and improving inventory stow rate.
Amazon Advertising Case Study
Amazon Advertising Engineering and Development (AED) increased throughput and avoided a three-year project to rebuild performance monitors and management tools by shifting data held in Oracle databases to Amazon RDS. AED builds, manages, and scales the technologies that undergird Amazon's programmatic advertising offerings.
Amazon.com Buyer Fraud Service Gains Scalability, Cuts Costs in Half Using AWS
Amazon Transaction Risk Management Services (TRMS) migrated more than 100 on-premises Oracle databases to AWS. Because the Buyer Fraud Service is a critical application and must operate at 99.995 percent availability, TRMS decided to use PostgreSQL-compatible Amazon Aurora as the new platform to host its databases.
Amazon CloudWatch Delivers Metrics to Customers Faster, Saves Millions Annually Using Amazon DynamoDB TTL
Amazon CloudWatch (CloudWatch) is a service used by AWS customers to monitor their cloud resources and applications running on AWS.
Scaling Amazon.com’s Transactional Subledger using Amazon DynamoDB
Across its many business entities, Amazon uses the Financial Ledger and Accounting Systems Hub (FLASH) to process more than 20 billion financial transactions each month. In 2017, the FLASH organization decided to migrate all its Oracle databases to AWS services.
Amazon Speeds Desktop Deployment for 25,000 Global Workers Using Amazon WorkSpaces
Amazon's Client Engineering team uses Amazon WorkSpaces to give global workers fast, restricted access to corporate resources, onboard new users in minutes, and save over $17 million annually.
Learn more about Amazon Aurora .
Ending Support for Internet Explorer
We and our partners use cookies to give you the best online experience, including to personalize content, advertising, and web analytics. You can reject cookies by changing your browser settings. To learn more about the cookies we use see our Cookie Policy .
- Supply Chains
- Manufacturing
- Transportation
- Warehouse Operations
- Rail Logistics
- Ports & Terminals
- Road Traffic
- Passenger Terminals
- Business Processes
- Asset Management
- Social Processes
- Why simulation
- AnyLogic Timeline
- Artificial Intelligence
- Digital Twin
- Enterprise Simulation
- Get started
- White papers
Case studies
- Training and events
- AnyLogic Conference
- Documentation
- For academia
- Academic articles
- Clients & Testimonials
- --> Supply Chains
- --> Manufacturing
- --> Transportation
- --> Warehouse Operations
- --> Rail Logistics
- --> Oil & Gas
- --> Ports & Terminals
- --> Road Traffic
- --> Passenger Terminals
- --> Healthcare
- --> Business Processes
- --> Asset Management
- --> Marketing
- --> Social Processes
- --> Defense
Walmart’s Alphabot: Designing Material Handling System with Simulation
Walmart, the world’s largest retailer by revenue, was looking for an automation technology that would help complete orders faster and at a lower cost in the company’s fast-growing online grocery business. They wanted to evaluate Alert Innovation’s Goods-to-Person (GTP) concept, Alphabot (an AGV or robot-based system), which could automate the grocery pickup process by using autonomous mobile carts capable of operating in all three dimensions within a multilevel storage structure.
Optimizing E-Commerce Warehouse Operations
The global e-commerce sector has seen 320% growth in five years, and demand is increasing following the COVID-19 pandemic. To reduce costs and remain competitive, DHL Supply Chain ran a warehouse operations optimization project. The project involved developing a smart and robust warehouse simulation tool for testing wave picking strategies.
Optimizing Warehouse Operations for Pharmaceutical Distribution Company
Cardinal Health, a billion-dollar pharmaceutical distribution and logistics firm, manages multiple products from brand name pharmaceuticals and generic drugs to over the counter drugs, health & beauty items and their own private label. They face a multitude of typical distribution warehouse challenges that are further complicated by the nature of pharmaceutical products. Brian Heath, Director of Advanced Analytics at Cardinal Health, and an experienced user of AnyLogic software, employed agent based modeling to solve various business problems, saving Cardinal Health over $3 Million annually.
Warehouse Simulation for Choosing Optimal Picking Algorithm
Kuehne+Nagel, a leading global provider of logistics solutions, was involved in planning a new warehouse for one of their clients. The warehouse would process 13K order lines or 750 picking cartons per day. The project included the development of the best algorithm for multi-order picking. It was planned that the orders in the warehouse would be served by workers with trolleys (or fangos). Workers with trolleys would pick the goods and put them in cartons by order.
Warehouse Cluster Pick Optimization
How DHL optimized warehouse order picking and improved efficiency. Analysis using simulation-based modeling increased picking speed and reducing order completion times. The tool integrates with warehouse management systems.
Developing a Forecasting Simulation Model for Efficient Warehouse Operations
A warehouse in Thailand was encountering difficulties because of a number of complicated processes involved in their logistics and storage systems. In order to overcome these and achieve more efficient warehouse operations, EPIC InnoLabs was contracted to develop a forecasting simulation model. This model would be used to predict system behavior based on a number of inputs as well as retrieve the expected values of selected KPIs.
Large-Scale Logistics Network Planning and Optimization
For a delivery network processing 15 billion parcels annually, simulation modeling provided significant saving across key metrics in a package easily accessible to all stakeholders. Find out how in this case study and presentation from Pitney Bowes.
Creating a Workforce Optimization Model for a Micro-Fulfillment Center
Micro-fulfillment centers are small, sometimes highly automated facilities that can fulfill online orders for delivery as well as click-and-collect in-store pickups. They use a combination of automated picking technology and manual picking. Dematic wanted to create a workforce optimization model that they would be able to present to retailers. It would help them understand the staffing required to operate their micro-fulfillment centers and how different scenarios could impact their ability to fulfill orders.
Evaluating Introduction of Warehouse Automation Systems
Symbotic is a warehouse automation solutions provider. Its systems are based on mobile robots that can travel freely throughout a dense storage structure, accessing products in all locations and handling them at a very high throughput rate. The company needed a tool to help their customers learn the impact of warehouse reorganization and compare capital investments against expected operational savings before the actual introduction of automation systems.
Cold Store Warehouse Operations Optimization
Phoenix Analytics is a Turkish consulting company and provider of simulation solutions for various industries. They were involved in developing a warehouse optimization project for one of the biggest ice-cream and frozen desserts manufacturers in Europe and Asia.
Get a brochure with industry case studies
Case Studies
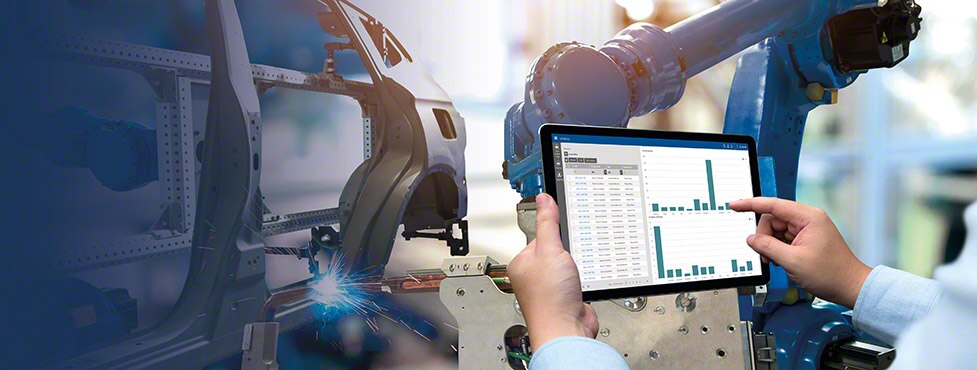
The automotive maker Renault has installed the Easy WMS warehouse management system by Mecalux in its production warehouse in Seville (Spain). The manufacturing centre in this city focuses on the assembly of transmissions and the warehouse supplies manufacturing ...
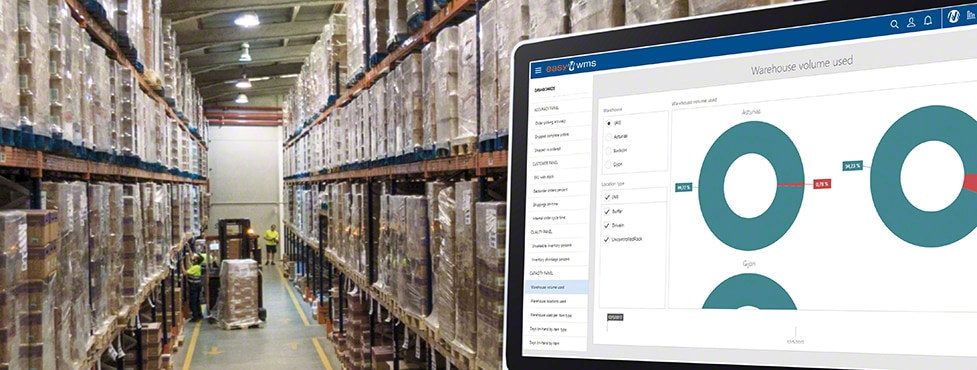
Danone’s distribution centre in Valdemoro (Spain) must cope with a very high-paced daily work rhythm: managing between 500 and 600 SKUs and preparing up to 700 orders. It is an all-in-one omnichannel warehouse, i.e. orders are sent to retailers, wholesalers and c...
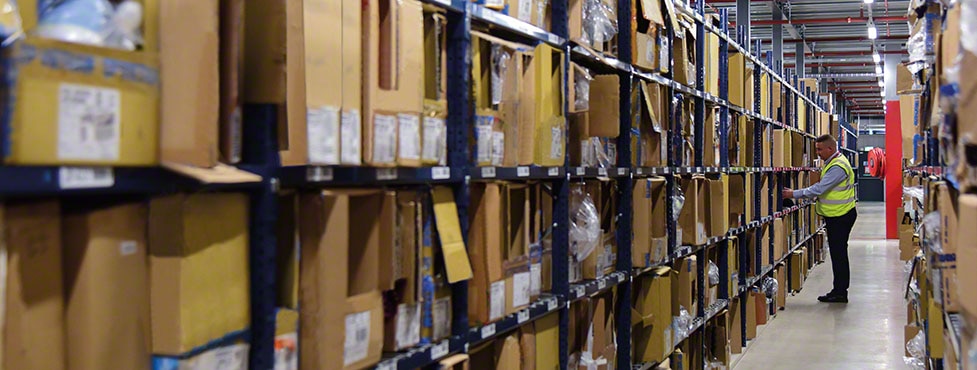
Decathlon has chosen Mecalux’s shelving for picking once again to manage its omnichannel logistics. After equipping its warehouses in France, Germany, Italy and Poland, it is Northampton’s (UK) turn. With 35,000 SKUs, the warehouse preps and ships out 3,000 order...
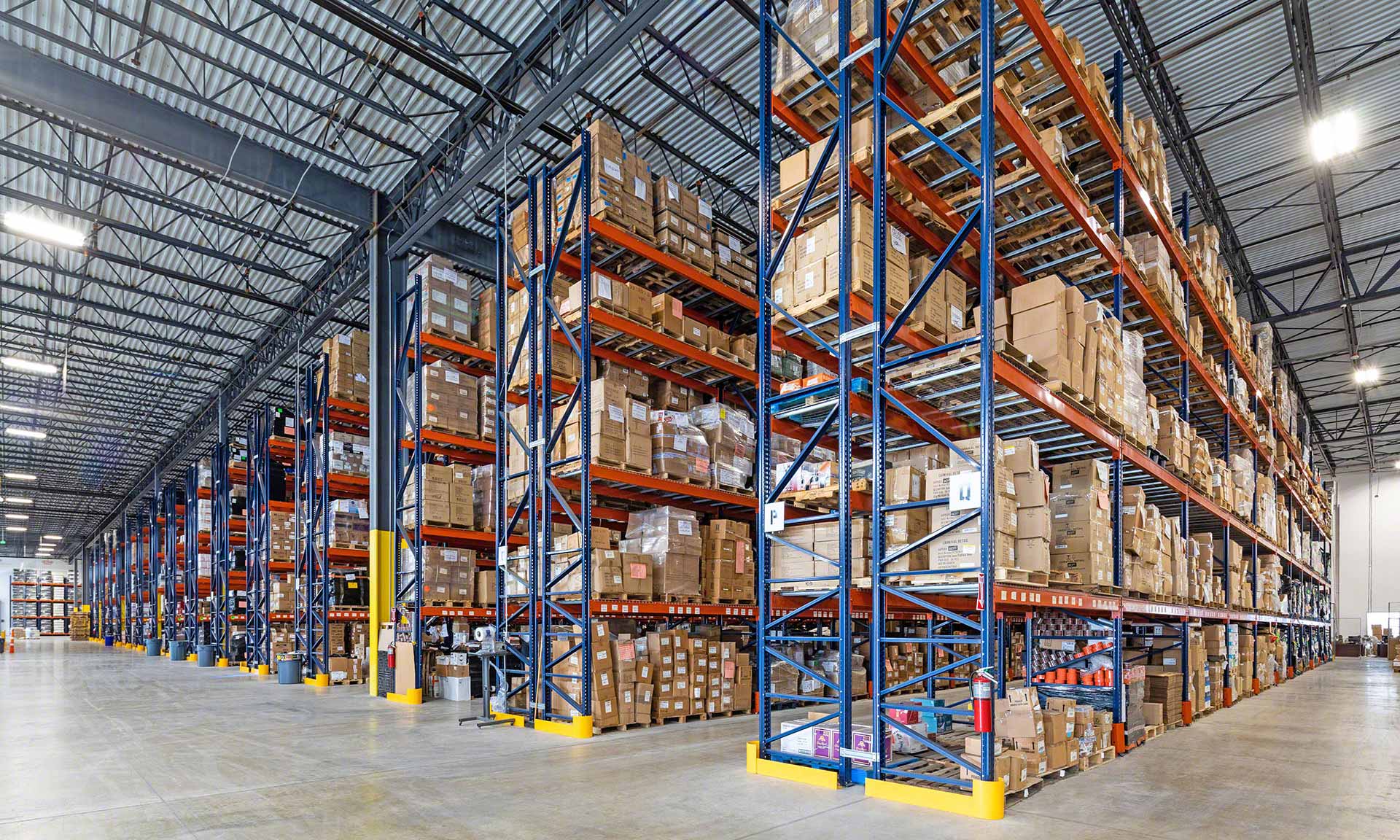
Interlake Mecalux and partner Andersen Material Handling have equipped a 13,935 m 2 warehouse in Miami, Florida, for Dufry, a travel retailer. The project includes adjustable pallet racks and the high-density push-back racking system. Overall, the syste...
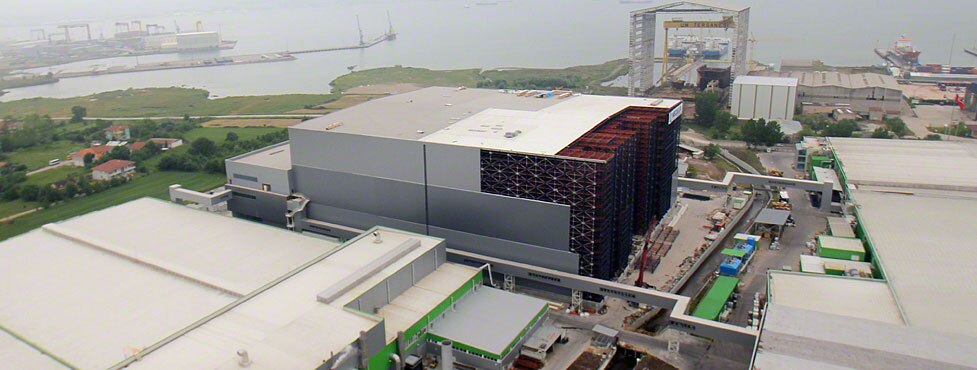
Hayat Kimya
Hayat Kimya is a leading manufacturer in the Eurasian fast-moving consumer goods market, specifically in the sector for hygiene and cleaning products. Founded in 1937, with its headquarters in Turkey, the company currently has 5,200 employees and exports to 101 c...
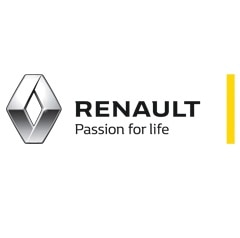
Here you can see some real solutions that Mecalux has developed. Contact us so we can assess the ideal solution for your company.
See our case studies for:
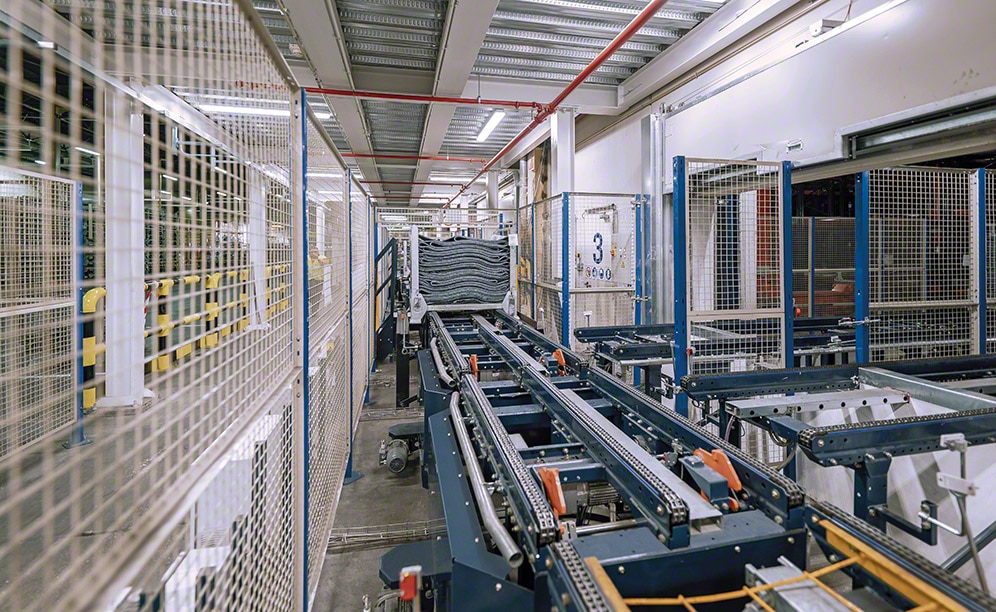
Automated clad-rack warehouse of Michelin integrated with manufacturing
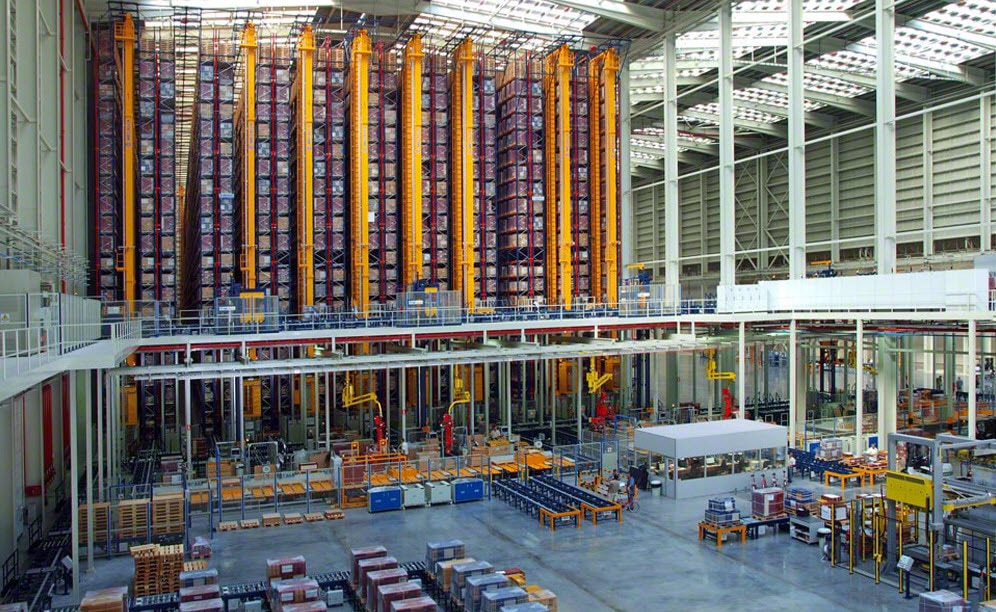
Porcelanosa
Mecalux completes the process of automating the porcelanosa group’s warehouses in castellón, spain.
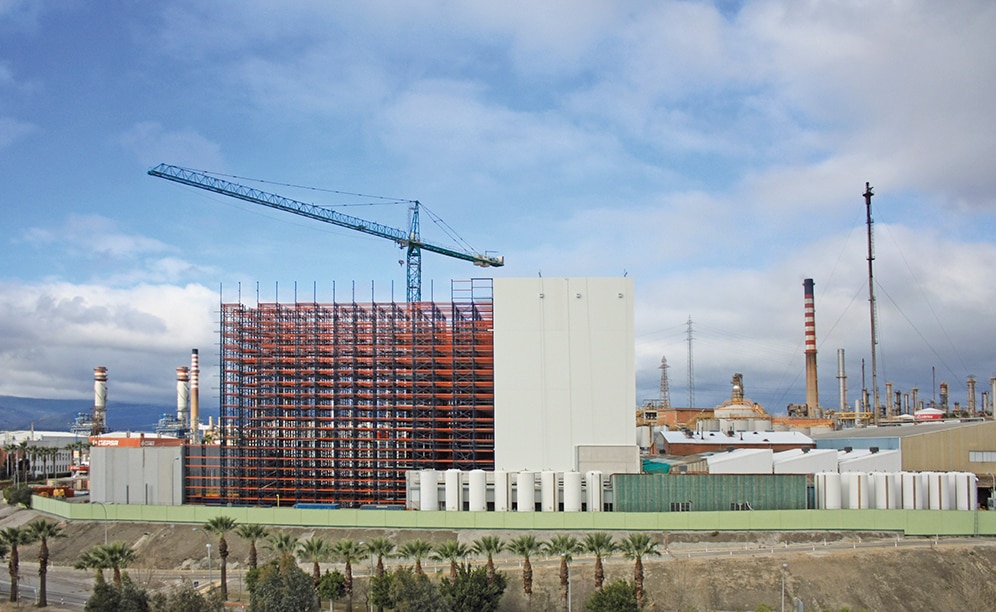
Next-generation automated clad-rack warehouse: a sure bet to streamline of logistics processes at Cepsa
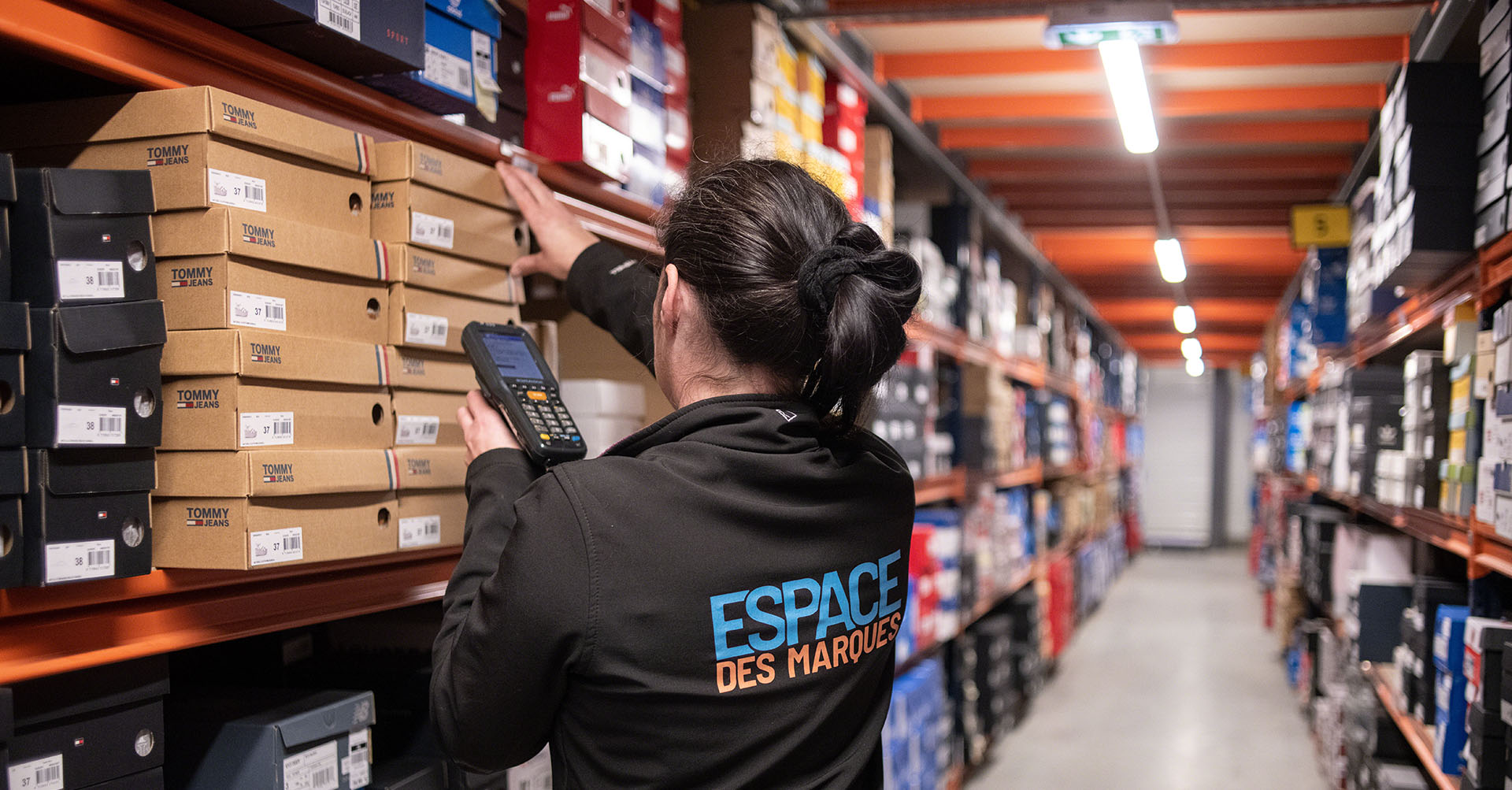
Espace des Marques
Omnichannel warehouses with 70,000 skus.
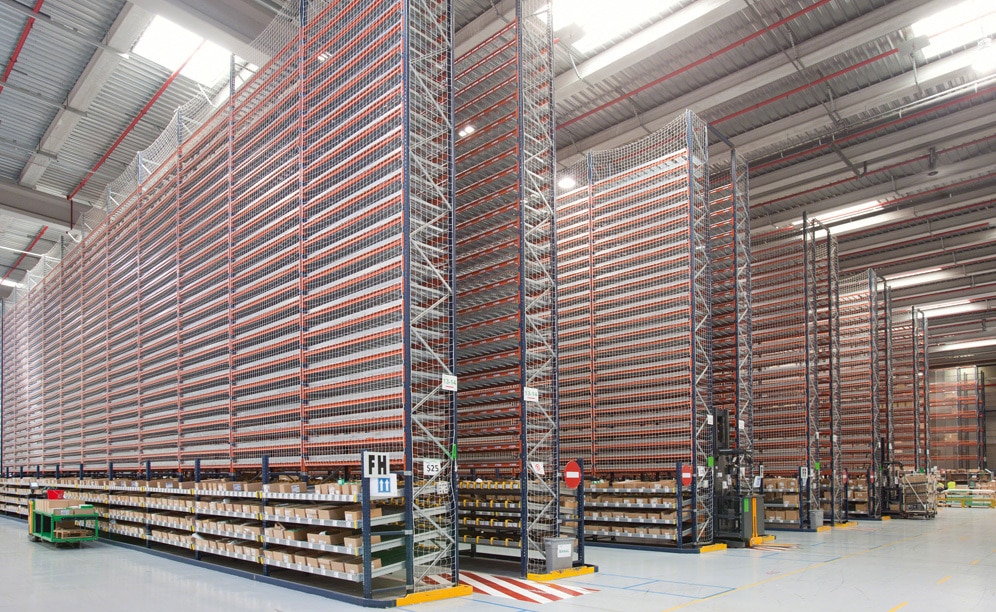
Schneider Electric
How to achieve the ideal balance between speedy picking and storage capacity.
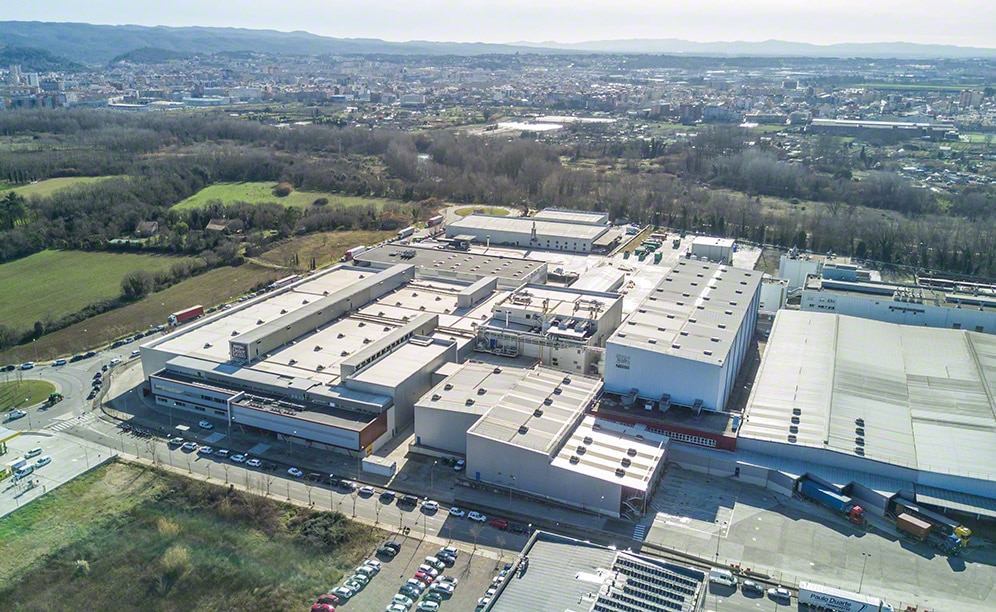
Efficient conveyors improve storage at Nestlé in Girona
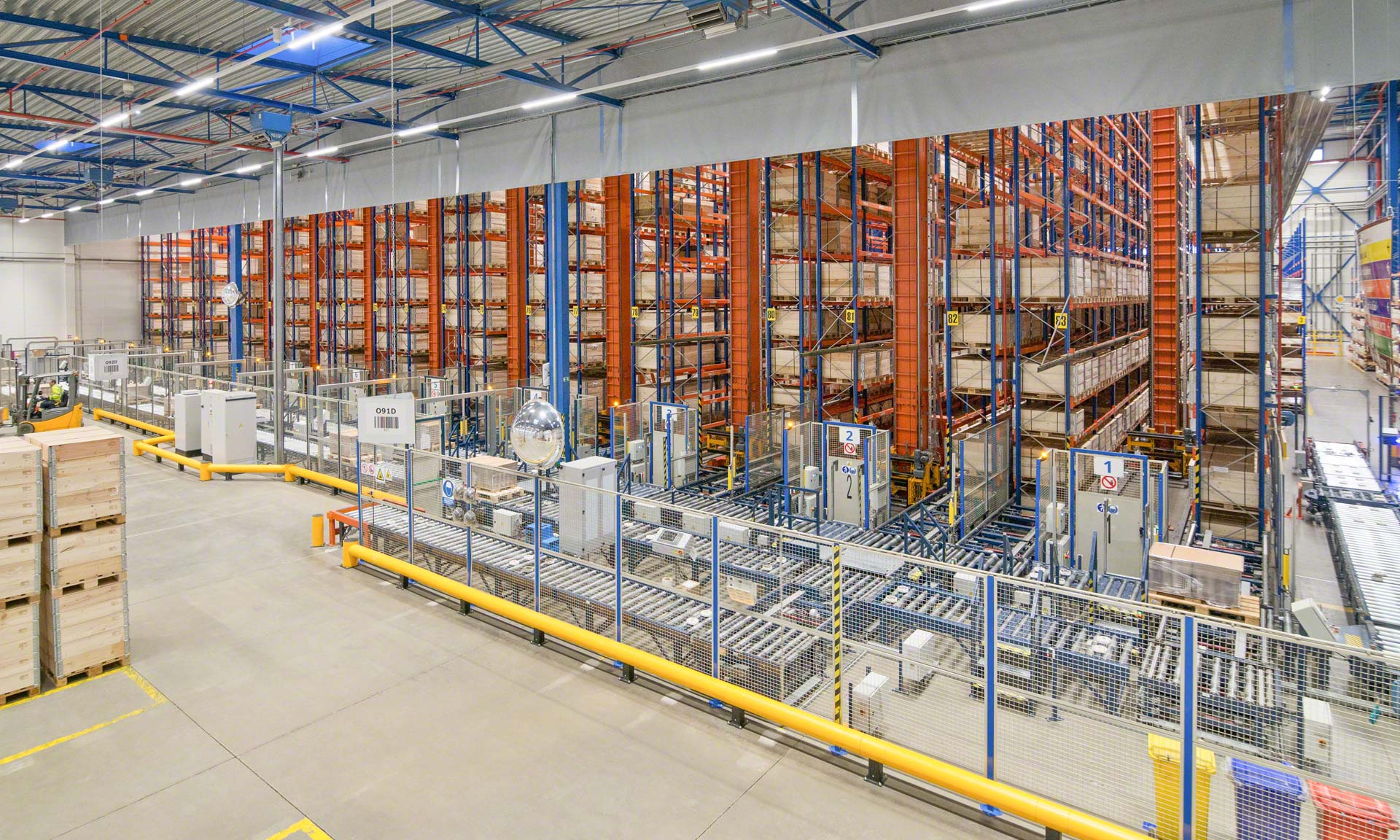
IKEA Components
Ikea components automates its warehouse in malacky without disrupting operations.
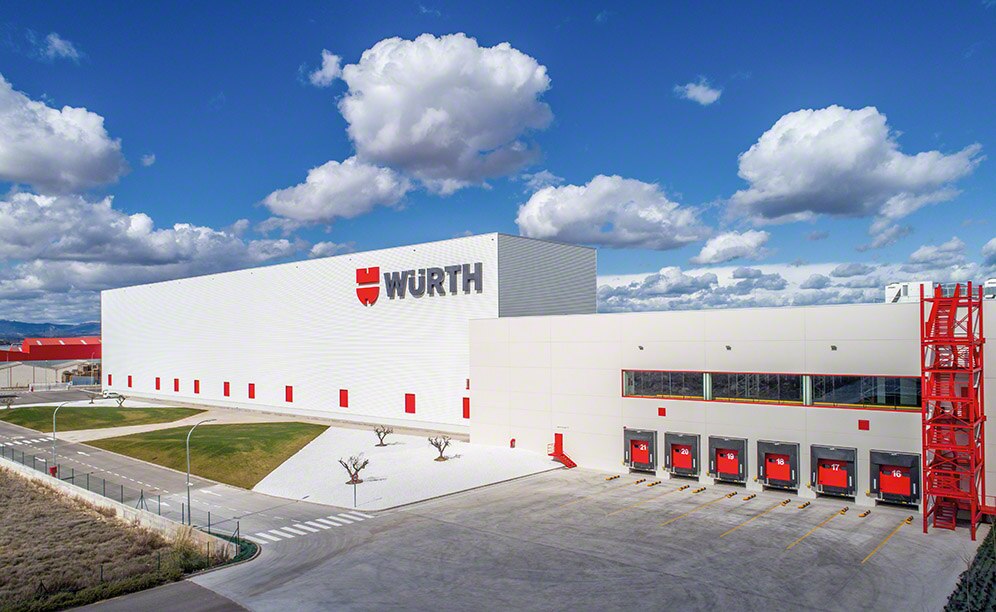
A 100% automated, turnkey warehouse for Würth in La Rioja
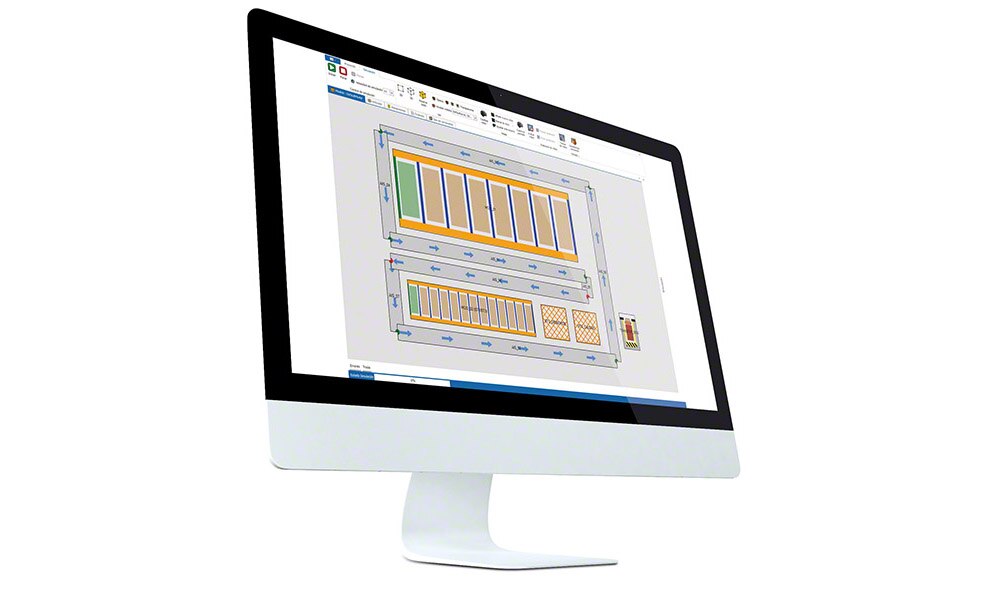
Easy WMS of Mecalux runs the warehouse of the car maker Renault
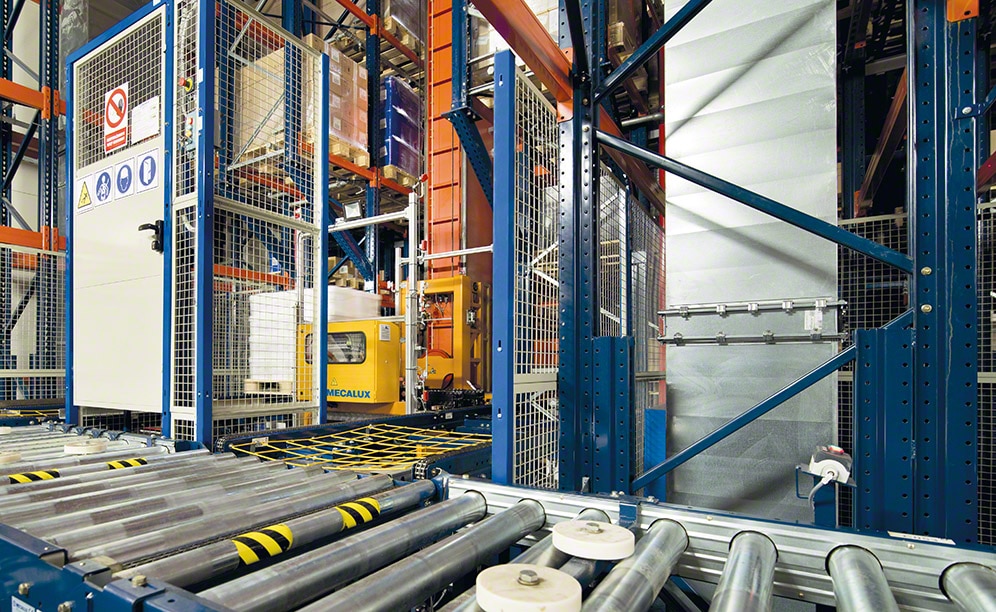
Novartis automates its supply chain in Poland
Coca-Cola Refrescos Bandeirantes
Warehouse with coca-cola soft drinks of refrescos bandeirantes in brazil.
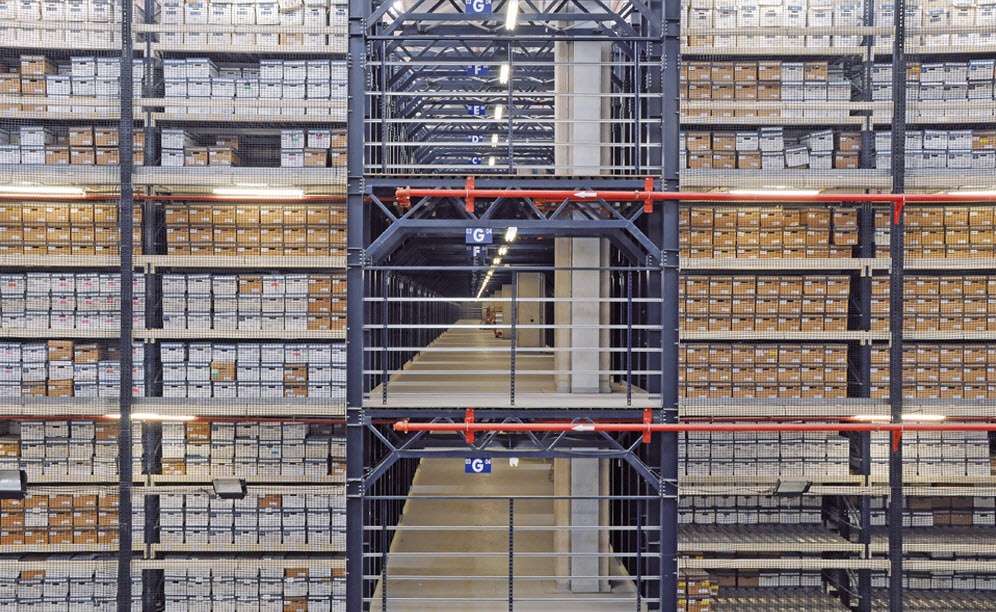
Iron Mountain
Earthquake-proof racking: warehouse with mecalux conventional racking on the pacific rim.
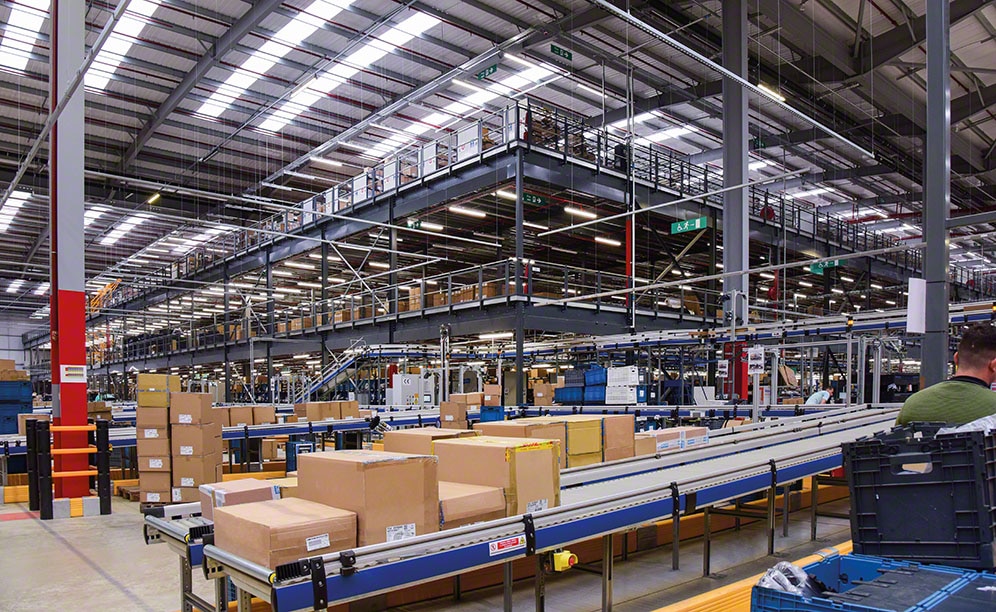
Decathlon has opened a new omnichannel warehouse in Northampton (United Kingdom)
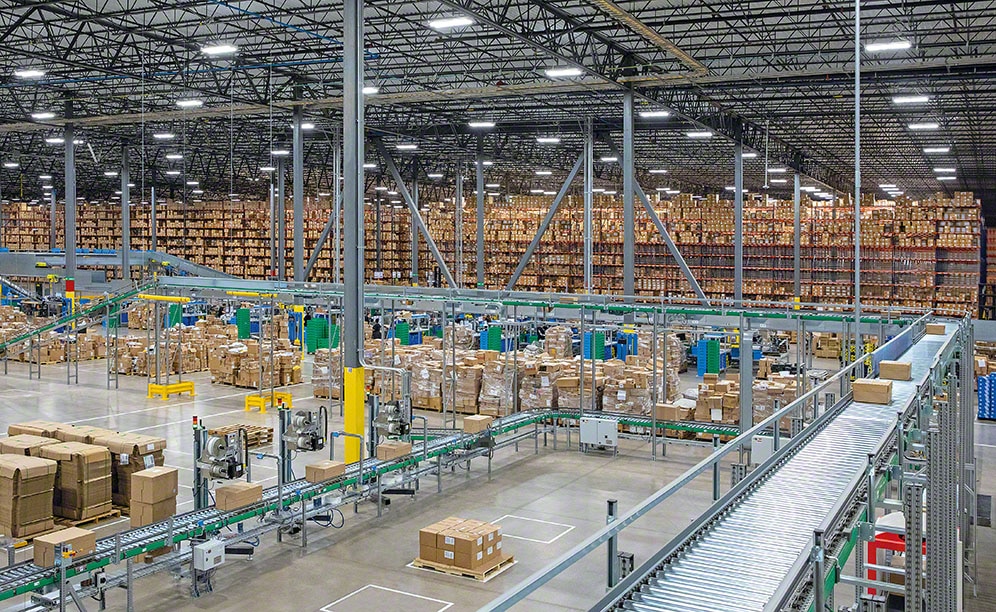
The Adidas sportswear and footwear store in Pennsylvania, USA
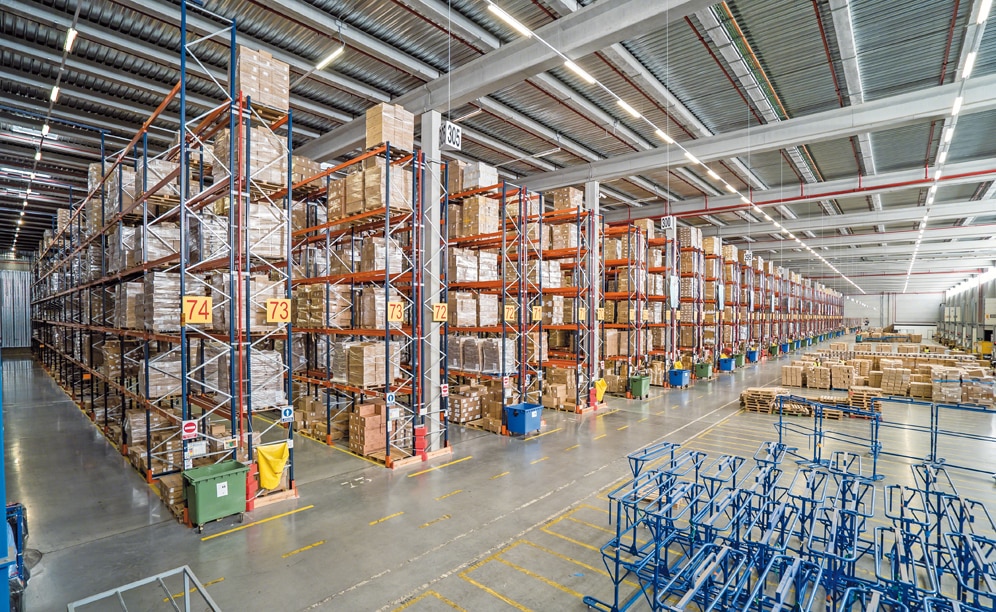
Mecalux installs a new logistics centre for DHL on the outskirts of Madrid
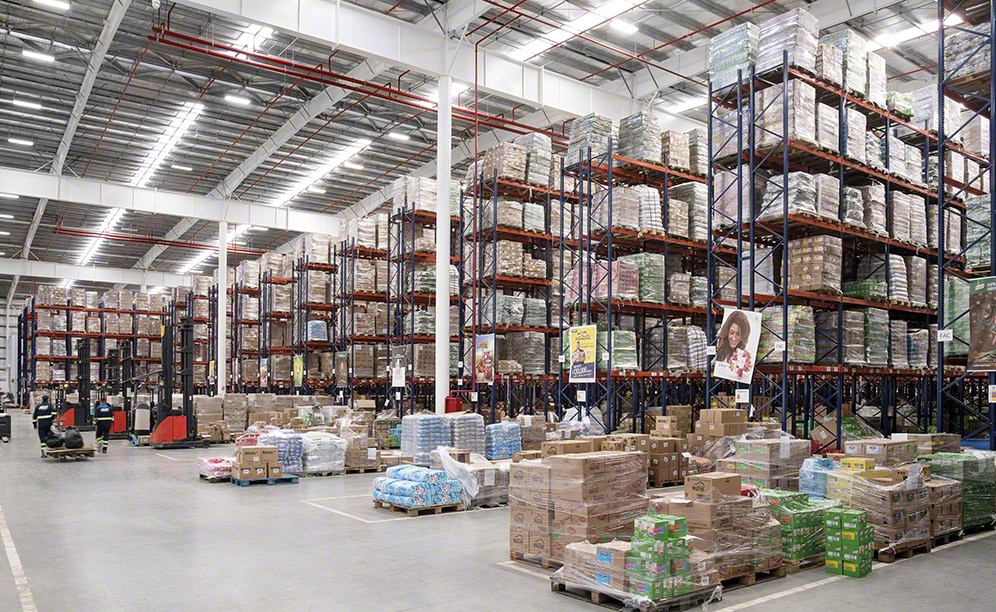
Mecalux has equipped the new Unilever distribution centre with pallet racking
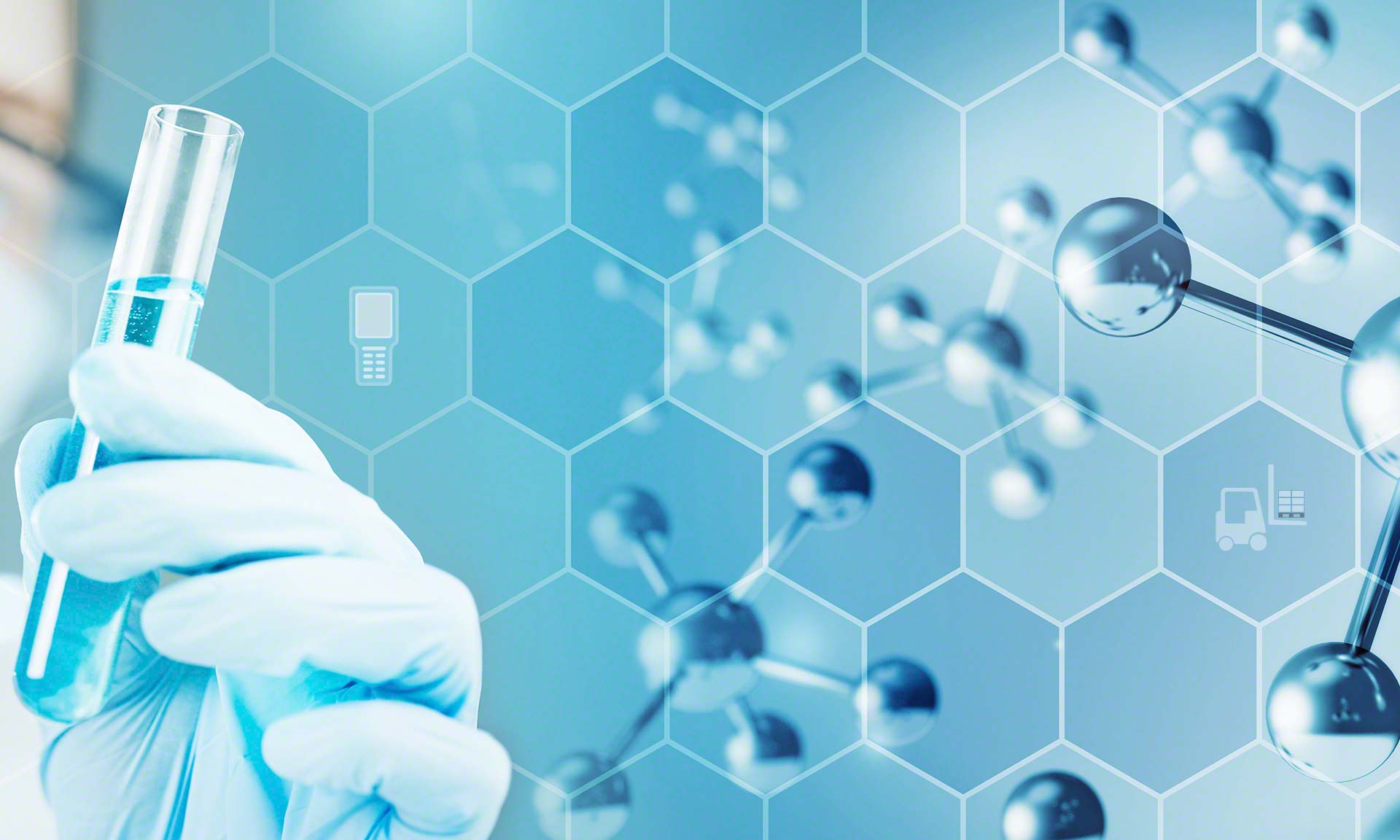
BASF: digitisation for just-in-time production
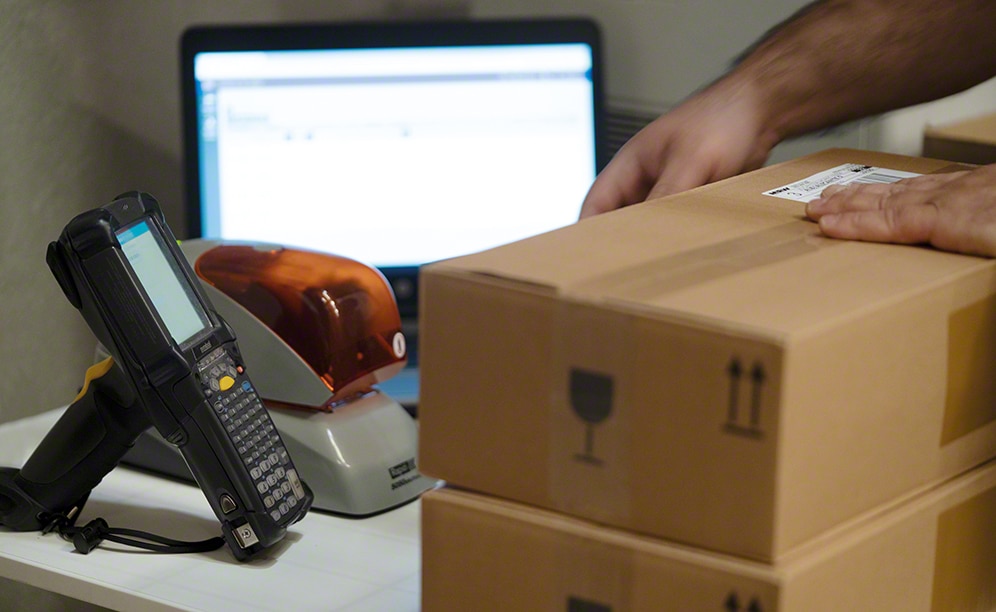
Danone’s warehouse for the infant and medical nutrition product line in Madrid
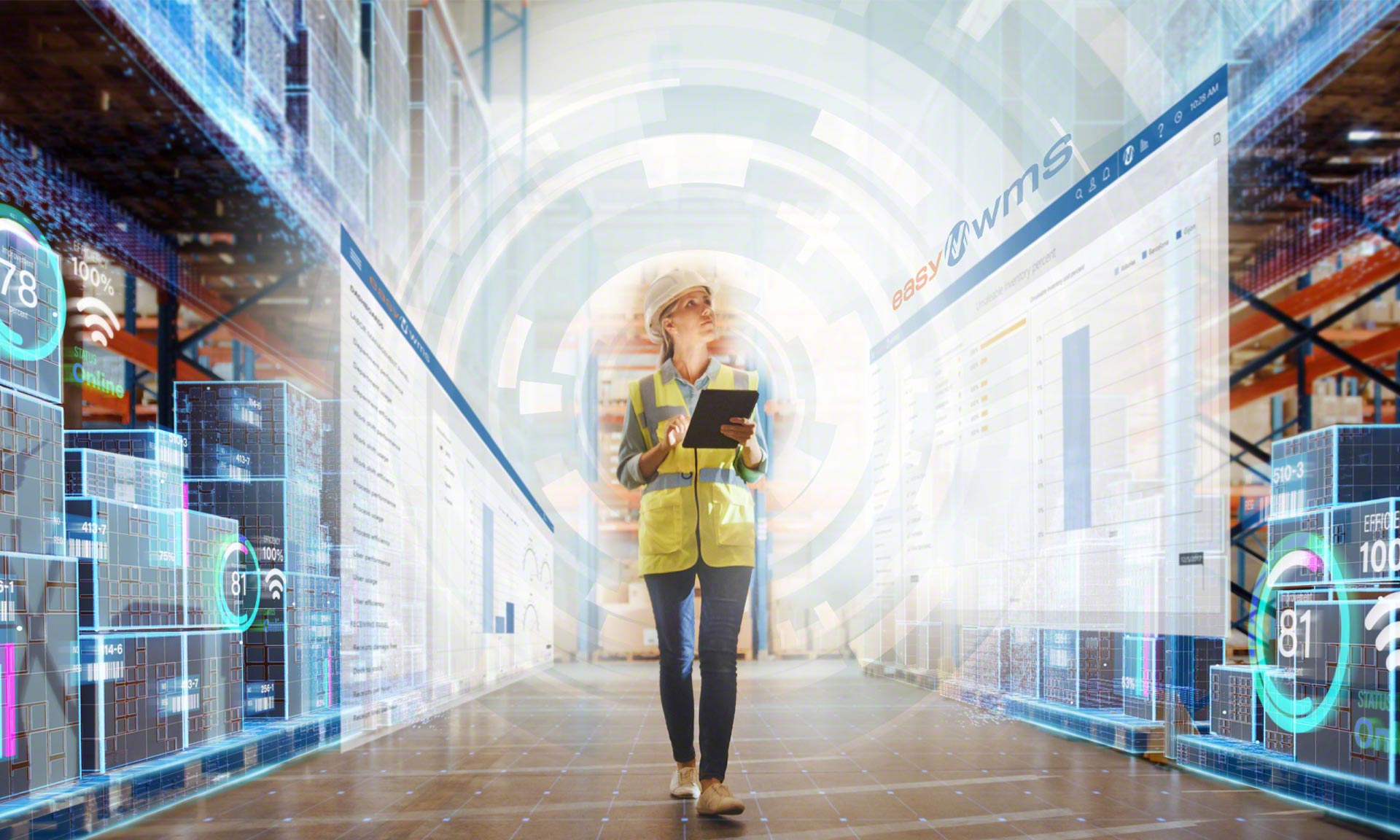
Digitisation transforms the supply chain
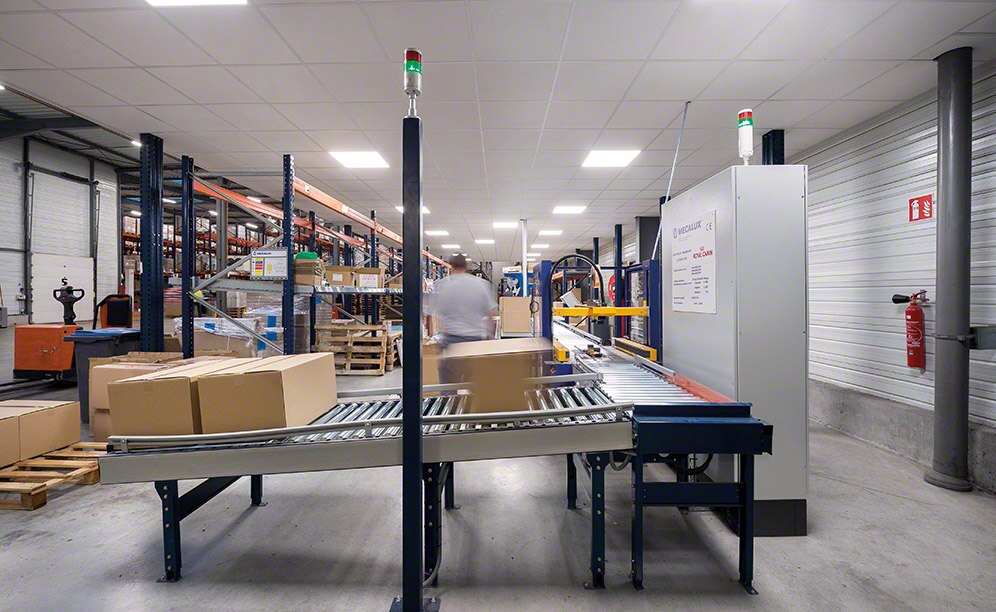
Royal Canin
Multiple solutions to manage pet food products, {{reference.name}}, {{reference.pcase.name}}.
Improving warehouse operations—digitally
Warehouse operations are increasing in complexity with time. The growth of e-commerce has led to a proliferation of SKUs, and there’s an ever-growing need to delight customers by offering super-fast fulfillment. Technology is a factor as well: as new automation systems come onto the market, operations leaders must face the challenge of keeping pace and understanding which technologies apply and what kind of impact they can generate.
Worldwide, companies spend an estimated $350 billion a year on warehousing, and that number grows each year as pick sizes shrink and costs balloon, raising pressure not just on margins but also on service levels.
The need to improve both sides of the equation may be obvious, but the question is how. Trial-and-error is not an option: companies cannot simply shut down a warehouse so they can tinker with new layouts and workflows to see what works best.
But the better news is that they don’t have to. A few companies are already able to design and visualize their warehouse operations virtually via “digital twin” simulations. The simulations allow companies to create virtual models of their existing facilities, and then test different scenarios—no shutdowns required.
This digital warehouse-design approach lets companies experiment with different floor plans, workflows, and other variables to assess the overall impact virtually. Operations leaders can see the impact of changes in a wide range of factors, including the SKU mix, order and shipment profiles, seasonal demand spikes, productivity initiatives, automation options, and a host of other issues that impact warehouse performance. This level of detail allows warehouse designs to be optimized in advance, before anyone starts moving physical assets.
The process typically takes six to ten weeks. The revamped warehouse designs that result can help companies improve efficiency by 20 to 25 percent, before spending the money to test or pilot the changes (exhibit).
Would you like to learn more about our Operations Practice ?
The power of digital simulations.
Digital warehouse design has a wide range of applications, from productivity initiatives at existing facilities to mergers, warehouse consolidations, and new warehouse construction. Across all applications, however, the benefits are reasonably consistent: sizable savings in operating expenses from productivity improvement, as well as in capital expenses from optimizing the deployment of material-handling equipment, storage assets, and targeted, right-sized automation systems.
The approach removes bottlenecks to improve efficiency and effectiveness, and enables optimal slotting and product flows to meet service requirements at the lowest possible cost. Most important, digital warehouse design identifies the full potential of a given facility, rather than forcing companies to settle for incremental improvements to the as-is layout.
Critically, the process also enables companies to gauge the potential impact of mechanization and automation options across the entire spectrum of vendors and products on the market. These technologies can be powerful tools to reduce space and increase efficiency. But in some cases, incorrect or inappropriate automation can actually create more problems than it solves. Digital modeling lets companies see what is possible from a range of technologies and applications, before they make any investment decisions.
Transcending traditional improvements
Of course, most companies know they need to improve their warehouse operations. But they struggle to identify and make the needed upgrades, due to limited data and internal expertise. Quite simply, many companies lack the full set of capabilities needed to assess various warehouse improvement options and create a business case that incorporates capex investments and running costs.
Some rely on third-party logistics providers, but even those vendors often lack the breadth of expertise to see what is truly possible with alternative warehouse designs and operations. A related problem is that most traditional methods to design or revamp warehouses use computer-aided design software (CAD)—which is resource-heavy and time-consuming, and doesn’t allow companies to calculate the impact of new changes or anticipate second-order effects. Digital warehouse design, by contrast, offers a low-risk way to visualize and optimize layouts, allowing companies to rapidly identify real, feasible solutions that deliver quick impact.
For example, a North American manufacturer decided to consolidate several regional manufacturing and warehouse locations into a single campus, with separate buildings dedicated to manufacturing and warehousing. However, it faced several challenges, including capital constraints, insufficient warehouse space, and a need to move fast.
Instead of relying on traditional tools, the company used a digital warehouse-design approach to simulate various options across warehousing, kitting (assembly of related items into a single “kit” for shipment), and value-added operations. The digital tools allowed the company to develop detailed OPEX and CAPEX estimates for both manual and automated solutions, making it far easier to evaluate various business cases. In all, the company reduced planned capex by approximately 10 percent and operating expenses by more than 30 percent.
Digital warehouse design can also help companies rethink existing facilities. For example, another company deployed digital warehouse-design and simulation tools to optimize and revamp its operations in a warehouse currently in operation. It built models to test various layouts, material-handling-flow scenarios, picking methods, and targeted automation solutions.
Starting from an optimized slotting design, the digital twin analyzed historical orders to estimate the exact labor and equipment requirements by day of the week and by hour of the day. With accurate labor-staffing models, the company was able to choose the most optimal, modular design to implement during the transition. In addition, the company could define precise, engineered standards for each operation of the warehouse, and it could monitor daily labor and equipment performance once the new system was in place. This enabled the company to reduce annual operating expenses by 18 percent.
Similarly, one business had a central regional warehouse in Eastern Europe, with annual costs of several million dollars. By constructing a digital twin, the company analyzed the potential improvements from a proposed layout change (specifically, a picking zone that enabled one-step picking). Looking at both high-season and low-season volume, the company determined that it could reduce input costs by more than 25 percent.

Supply chain risk management is back
Foundational capabilities.
As with most technology, digital warehouse design is not a turnkey solution. To capture its full potential, companies must understand their strategy not only for today and tomorrow, but also well into the future—in terms of product portfolio, customer-order profiles, and other factors. Leadership teams must assess the implications of design changes on the supply-chain network as well. And success requires new capabilities in warehouse design—typically engineers who understand the range of variations and permutations for a space. Most organizations do not yet have internal people ready for these roles, and thus need to source that expertise externally.
As a practical matter, the simulation process must involve operations and warehouse managers—those with the deep day-to-day knowledge and real-world insights that can only come from direct experience. Because these experts will be tasked with implementing any changes to the warehouse after the simulation ends, their buy-in will be essential. The more they contribute during the early stages of the process, the more willing they are likely to be to forego old habits and work in new ways.
Last, companies need to plan for repeated changes over time. Optimizing warehouse performance is a process without a finish line—it must happen again and again, as market forces, technology, and consumer preferences continue to evolve. In fact, digital warehouse-simulation tools could become a new way of setting performance expectations, with the tools embedded as part of the day-to-day management of each distribution center. Estimating daily performance targets based on daily volume, mix, and staffing can help warehouse managers manage the shift’s performance more precisely than any other traditional, static approach to setting goals.
Companies face a growing need to improve their warehouse operations. Digital warehouse design is one clear means to help them do so. The process may be virtual, but the results generate a real impact on performance, providing an edge in an ever-more-complex warehousing landscape.
Stay current on your favorite topics
Felipe Bustamante is a consultant in McKinsey’s Miami office, Ashutosh Dekhne is a partner in the Dallas office, Jörn Herrmann is a senior expert in the Zürich office, and Vedang Singh is a consultant in the New Jersey office.
The authors wish to thank Aditi Brodie for her contribution to this article.
Explore a career with us
Related articles.

Digital supply-chain transformation with a human face
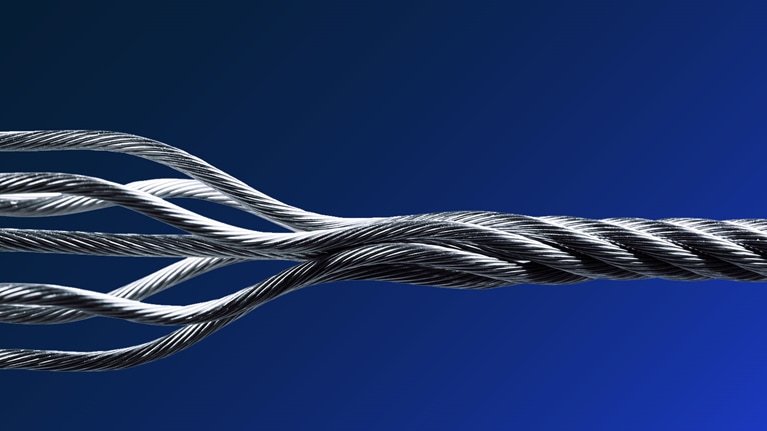
Industry’s fast-mover advantage: Enterprise value from digital factories
Know more about our vision & mission at Zenkins.
Learn more about our process and how we work?
Contact today! Ready to help you with all tech challenges.
Stay updated with latest technologies and tools.
SAAS Product Development
Empowering Your Vision with Expert SAAS Product Development Services
IT Staff Augmentation
Boosting Your IT Capabilities with Staff Augmentation Solutions
Product Engineering
Crafting Innovation Through Product Engineering Services
Platform and Infrastructure
Elevating Your Digital Foundation: Our Platform and Infrastructure Expertise
Digital Transformation
Unlocking Your Digital Potential: Transformation Services for the Modern Age
Data Engineering
Unlocking the Power of Data: Our Expert Data Engineering Services
IT Consulting
Navigating IT Excellence: Our Comprehensive Consulting Services
- Maintenance And Support
Safeguarding Your Success: Exceptional Maintenance and Support Services
Core Expertise
- .NET Development
- ASP.NET MVC Web Dev.
- ASP.NET Core Web Dev.
- ASP.NET Web Form Dev.
- .NET Windows App Dev.
- .NET WPF Application Dev.
- .NET Core API Development
- .NET WCF Services
- .NET CMS Development
- C# Development
- .NET Core Development
- Full-Stack Web App Dev.
- Agile, Scrum & DevOps
- Integration Services
- Mobile App Development
- AI ML Development
- Legacy .NET App Modernization
- E-Commerce Solutions
- Enterprise Application Dev.
- Database Design And Mgmt
- Cloud Integration
- Azure / AWS / GCP
- Migration Services
- Third-Party Integrations
- UI/ UX Design
- Quality Assurance & Testing
- Security And Compliance
- Consulting And Strategy
- Content Management
- Performance Optimization
- IoT Hardware & Software
- .NET Developers
- C# Developers
- VB.NET Developers
- .NET Core Developers
- Windows Desktop Application Developers
- Azure Developers
- SQL Server Developers
- ASP.NET MVC Developers
- Blazor Developers
- Angular Developers
- Full-Stack .NET Developers
- HTML / CSS Developers
- JavaScript Developers
- Xamarin Developers
- Kentico CMS Developers
- Sitecore Developers
- Umbraco Developers
- Orchard CMS Developers
- DNN (DotNetNuke) Developers
- Sitefinity Developers
- NopCommerce Developers
- mojoPortal Developers
- DevOps Engineers
- UI/UX Designers
- Quality Assurance (QA) Testers
- Security Experts
Build Your Team
We help companies transform, scale, and gain a competitive edge with robust, customized, and innovative digital solutions.
- Technologies
- Entity Framework
- Razor Pages
- Razor Views
- Microservices
- IdentityServer
- Visual Studio
- Visual Studio Code
- Azure DevOps
- SQL Server Management Studio (SSMS)
- AWS (Amazon Web Services)
- GCP (Google Cloud Platform)
- Azure Functions
- Distributed Platforms
Our expertise spans all major technologies and platforms, and advances to innovative technology trends.

Can't find what you need?
- Case Studies
Warehouse Management Software: A Case Study
- Post author: Maryliya M J
- Post published: January 11, 2024
- Reading time: 12 mins read
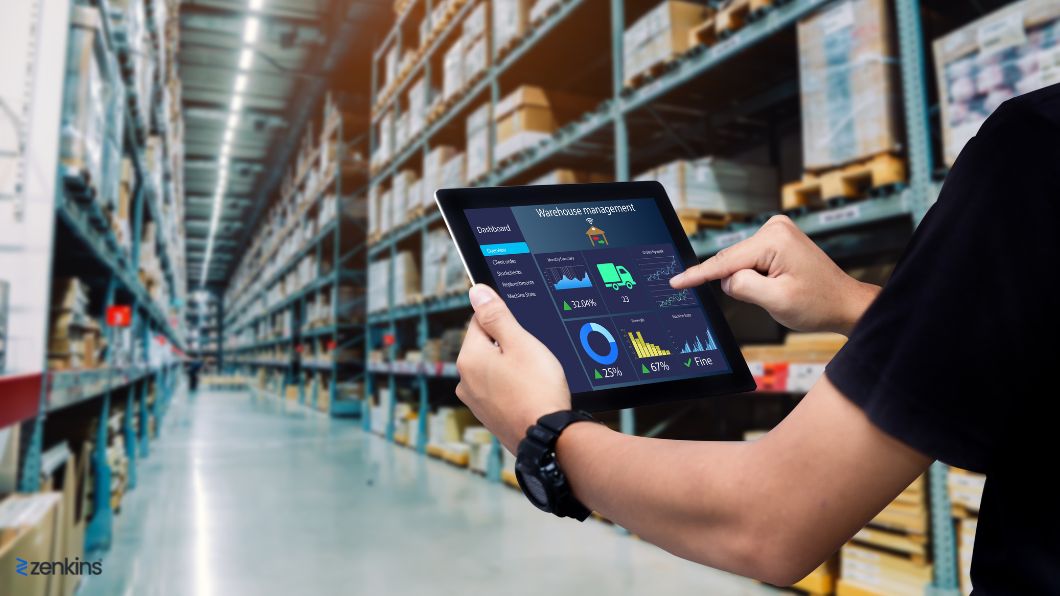
Warehouse Management Software (WMS): A Case Study
Table of contents.
Warehouse management software (WMS) has become an integral tool for modern businesses seeking to optimize their supply chain operations. With the ever-increasing complexity of managing inventory, orders, and logistics, implementing an effective WMS solution can provide significant advantages.
Introduction to Warehouse Management Software (WMS)
Understanding warehouse management systems (wms).
Warehouse Management Software ( WMS ) is like your personal assistant for managing the chaos of a warehouse. It’s a fancy computer program that helps keep track of inventory, streamline processes, and make your life a whole lot easier. Think of it as the Hermione Granger of your warehouse – organized, efficient, and always on top of things.
Evolution and Advancements in WMS
Gone are the days of scribbling inventory numbers on a piece of paper and playing detective to find that missing box of widgets. WMS has come a long way since then. It has evolved from simple spreadsheets to sophisticated systems that can handle complex tasks like inventory tracking, order processing, and even automated picking and packing. It’s like upgrading from a flip phone to the latest iPhone – everything just works better.
Benefits of Implementing WMS
Implementing a WMS might sound like a hassle, but trust me, the benefits are totally worth it. With a WMS by your side, you can say goodbye to inventory nightmares, reduce errors, and improve overall efficiency. It’s like having a superpower that makes your warehouse run smoother than a freshly oiled machine. From enhanced inventory visibility to streamlined order fulfillment, WMS has your back.
About the Client
Our client, a prominent e-commerce company, faced challenges in efficiently managing its warehouse operations. With a growing inventory and increasing order volume, they recognized the need for a robust Warehouse Management Software (WMS) to streamline inventory tracking, order fulfillment, and overall warehouse efficiency.
Project Overview
The project involved developing a .NET-based Warehouse Management Software that seamlessly integrated with the client’s existing systems. The primary objectives were to provide real-time visibility into stock levels, automate order processing, and optimize the warehouse layout for improved picking and packing processes.
The Challenges
- Inefficient Inventory Tracking: The existing systems lacked real-time visibility, leading to inaccuracies in inventory tracking.
- Manual Order Processing: Order fulfillment processes were time-consuming and prone to errors due to manual interventions.
- Suboptimal Warehouse Layout: The warehouse layout needed optimization to enhance picking and packing efficiency.
The Solution
Our team, comprising skilled developers and project managers, collaborated to design and implement a comprehensive Warehouse Management Software. Technologies such as .NET, SQL Server, and REST APIs were employed to ensure a robust and scalable solution.
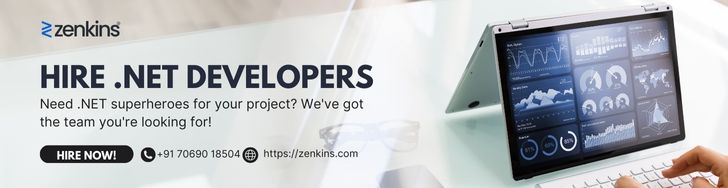
Are you struggling to keep up with your software development needs? Are you looking for a team of dedicated developers who can work on your project full-time and deliver high-quality results? So why wait? Contact us today to learn more about our services and to start the process of hiring your own dedicated development team. Let us help you take your project to the next level! Contact Now!
Key features of the wms.
- Real-time Stock Visibility: The WMS provided instant visibility into stock levels, reducing the risk of stockouts and overstock situations.
- Automated Order Processing: Orders were processed seamlessly, minimizing errors and accelerating the fulfillment process.
- Optimized Warehouse Layout: The software employed intelligent algorithms to optimize the warehouse layout, resulting in improved picking and packing efficiency.
The Outcome
The Warehouse Management Software was successfully deployed, leading to significant improvements in warehouse operations. The client reported enhanced efficiency in inventory management, reduced order processing times, and improved overall warehouse productivity.
By leveraging the benefits of WMS, such as enhanced inventory visibility, streamlined order fulfillment processes, and improved accuracy and efficiency, the company was able to overcome their warehouse management challenges and achieve remarkable results. The lessons learned from this case study provide valuable insights for businesses considering the adoption of WMS, emphasizing the importance of careful selection, thorough implementation planning, and seamless integration with existing systems. Ultimately, the successful implementation of WMS opens doors to increased productivity, cost savings, and improved customer satisfaction, making it a strategic investment for any organization looking to optimize their warehouse operations.
Our team’s expertise in developing a tailored Warehouse Management Software using cutting-edge technologies resulted in a solution that addressed the client’s challenges effectively. The implementation of real-time visibility, automated order processing, and warehouse layout optimization contributed to a more streamlined and efficient warehouse operation.
Are you facing similar challenges in warehouse management? Contact us today to explore how our expertise in WMS development can transform your warehouse operations and drive efficiency.
What is Warehouse Management Software (WMS) and why is it important?
Warehouse Management Software (WMS) is a software solution designed to efficiently manage and control various aspects of warehouse operations, including inventory management, order fulfillment, and logistics. It is important because it helps businesses optimize their warehouse processes, improve inventory accuracy, streamline operations, enhance productivity, and ultimately deliver better customer service.
How does a WMS solution benefit businesses?
A WMS solution offers numerous benefits to businesses. It provides real-time visibility into inventory levels and locations, enabling effective inventory management and reducing stockouts. It automates and streamlines order fulfillment processes, improving speed and accuracy while reducing errors. WMS also optimizes warehouse layout, resource allocation, and workflow, leading to increased operational efficiency, productivity, and cost savings.
What considerations should businesses keep in mind when selecting a WMS solution?
When selecting a WMS solution, businesses should consider factors such as scalability, ease of integration with existing systems, customization options, vendor support, and cost. It is crucial to assess specific business requirements, evaluate the software’s functionality, and determine whether it aligns with the organization’s long-term goals. Conducting thorough research, seeking recommendations, and requesting demos or trials can help make an informed decision.
Is it challenging to integrate WMS with existing systems and processes?
Integrating WMS with existing systems and processes can present challenges, mainly due to differences in data structures, formats, and compatibility. It requires careful planning, data migration, and coordination between the WMS provider and internal IT teams. However, with proper communication, collaboration, and expert guidance, businesses can overcome integration challenges and achieve seamless connectivity between WMS and other enterprise systems.
Get 50% off on your first project with us! Join our community of satisfied customers and experience the power of our software team today. Contact now and get 50% off your first software project/ product. Don’t miss out on this exclusive offer! Your Name * Your Email * Contact Number * Brief Your Requirement * 0 / 500 Claim Your Discount Please do not fill in this field.
You might also like.
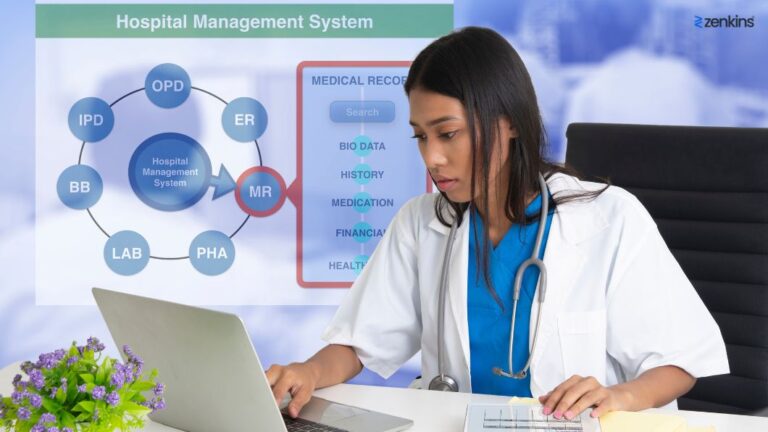
Hospital Management Software: A Case Study
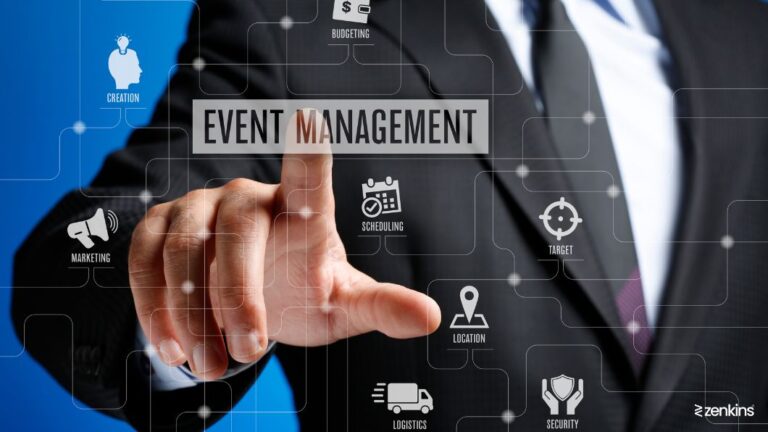
Event Management Software: A Case Study
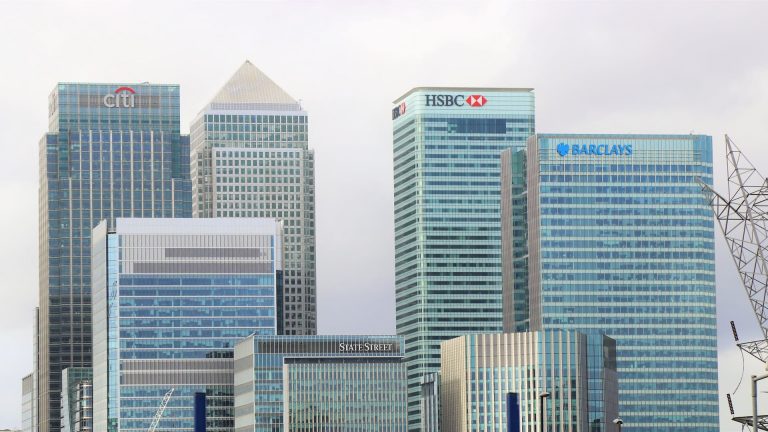
Our approach for offering our SmartX bank the greatest banking software development services
Book a free consultation.
Tailored Solutions, Expert Advice, and Project Estimates Await.
Expect a Prompt Call from one of our Account Managers.
- Top .NET Talent
- Time Zone Aligned
- Experienced Team
At Zenkins, we understand the importance of having skilled and dedicated .NET professionals on your side. Our team consists of top .NET talent with a proven track record of delivering high-quality solutions. Whether you need custom .NET application development or require expertise in ASP.NET, C#, or .NET Core, our talented developers are ready to bring your vision to life.
We recognize that time zone differences can often be a challenge in global collaborations. Zenkins addresses this issue by ensuring that our development teams are time zone-aligned with your operations. This means you can expect real-time communication, rapid responses, and a seamless workflow, reducing project delays and ensuring effective collaboration, no matter where you are in the world.
Experience matters in the world of software development, and our team has it in abundance. Zenkins’ experienced team brings a wealth of knowledge and expertise to the table. From legacy .NET application modernization to building cutting-edge cloud-native solutions using the .NET framework, our team has successfully handled a wide array of projects. You can trust us to navigate your software development journey with precision and care.
+91 70690 18504
[email protected]
Zenkins is a leading .NET development company in India, with over 10 years of experience in developing high-quality, scalable, and secure .NET applications. The company has a team of experienced and certified .NET developers who are experts in all aspects of .NET development, including ASP.NET, WPF, Windows Forms, WCF, Xamarin, and more.
- Methodologies
- Our Services
- IT Staffing Services
- Software Outsourcing
- Careers @Zenkins
- Current Openings
- Technology Insights
- Careers Insights
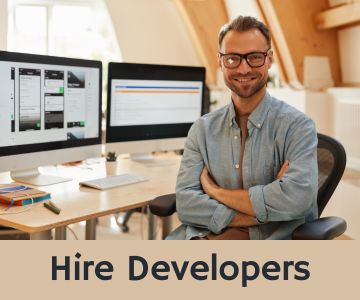
326, Naroda Business Point, Vasant Vihar 2, Nava Naroda, Ahmedabad, Gujarat 382330
Opening soon in Pune Baner, Pune, Maharashtra 411045 - India
Opening soon in Bangalore Vasanth Nagar, Bengaluru, Karnataka, 560020 - India
Privacy Overview
Get 50% off your first project with us.
Join our community of satisfied customers and experience the power of our software team today. Contact now and get 50% off your first software project/ product. Don’t miss out on this exclusive offer!
- Back to Blog
Case Studies of Successful Custom WMS Implementations
Commonly, we study the success stories of others to get inspiration and find new ideas for improving our business or personal efficiency. As a custom WMS development partner, we at HQSofware, also follow best practices and trends to deliver top-notch solutions to our clients. However, based on our WMS development experience, we can already share our own examples of winning warehouse management systems.
In this article, we’ll take a look at 5 successful examples of WMS software to understand how to implement such a system to enhance warehouse productivity.
What is a Custom WMS?
Developing an E-3PL System for Warehouse Automation
Implementing Predictive Analytics for Smart Inventory Management
Providing Warehouse Navigation to Speed Up Order Picking
Improving Supply Management with a WMS
Developing a WMS Module to Boost Marketplace Operations
How to Maximize WMS Efficiency?
A warehouse management system (WMS) is a powerful tool that optimizes and streamlines warehouse operations, including inventory management, picking and packing processes, shipping management, etc. A custom WMS, designed according to your unique workflow, eliminates unnecessary features and offers a user-friendly interface. With custom WMS development , you can prioritize factors that are crucial for your organization, ensuring that the system aligns perfectly with your unique business needs.
Let’s take a look at some custom WMS examples and how they’ve helped to overcome warehouse challenges for their respective owners.
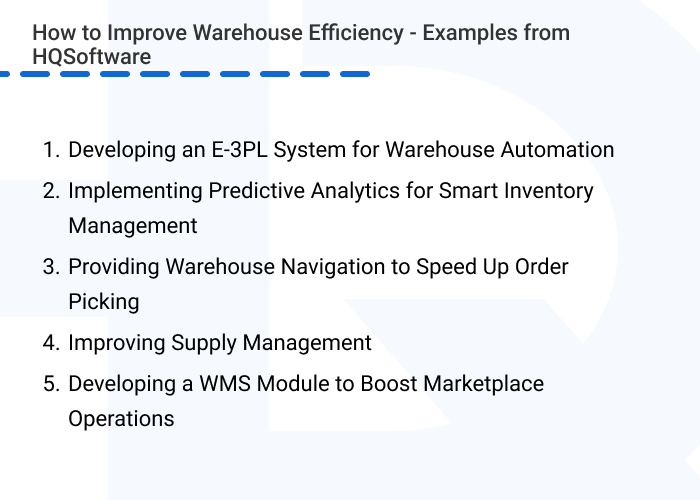
It’s no longer enough for a modern warehouse management system to merely provide inventory visibility and assist in order picking and packing. Companies are now striving to maximize operational efficiency by choosing smart systems with advanced features that can simultaneously address a wide range of issues.
In line with this trend, a US-based startup embarked on the development of comprehensive WMS software that adheres to modern requirements. A large international team of developers, including HQSoftware specialists, was involved in the project.
The main goal was to create an advanced system that can automate and optimize many logistics processes and perform some of them autonomously. For example: automatically generate replenishment orders based on customer demand forecasts, or update goods availability and price for buyers in real-time.
In addition, the system facilitates warehouse audits, provides enhanced navigation, integrates with numerous third-party systems, and enables express picking and receiving. With all its innovative features, the E-3PL platform boasts an impressive 99.9% order accuracy and 99.4% same-day order delivery.
This WMS implementation case study highlights the potential for comprehensive software to enhance virtually any warehouse operation. Achieving this requires a thorough analysis of every process within your warehouse and careful consideration of how advanced technology can drive improvements. This is especially beneficial if you decide to turn to custom WMS software development , as this allows you to build a system that meets your business needs in the best possible way.
Not wasting financial resources and being able to meet changing customer demand are deeply desired by every business and a must-have feature of modern WMS software.
Our client approached us with just such a request. They needed to upgrade a legacy WMS and implement predictive analytics capabilities to optimize warehouse inventory.
To accomplish this, our development team carefully selected the most suitable Machine Learning models capable of analyzing both historical and real-time operational data. The system provides data-driven replenishment recommendations tailored to specific parameters such as supplier delivery terms and minimum stock quantities. As a result, the client was able to reduce inventory costs by 15%.
The power of predictive analytics lies in its ability to learn and adapt to your unique business characteristics, offering personalized recommendations on how to improve it. So, you can benefit from optimal stock levels, excess-cost elimination, efficient space utilization, and a proactive response to customer needs, gaining a strong competitive edge in the market.
Since goods in a warehouse are not arranged as in a supermarket but are stored in boxes with numerical location identifiers, finding the right item can be a daunting task for pickers.
To address this WMS challenge and streamline order picking, our client — a retail company from Germany — decided to implement enhanced warehouse navigation . The feature creates optimized picking routes according to the picker and other items’ location and warehouse configuration.
The solution is delivered as a cross-platform mobile app that provides a map with a picking route and offers voice and visual guidance. With the app, pickers now spend 25% less time on order picking .
Even if you have many large warehouses with different layouts, this is no reason to overlook such a feature. Our developers can create an intuitive graphical interface that allows you to create any warehouse layout, as was implemented in this WMS case study.
Want to create a WMS solution to improve your warehouse operations? We’re ready to help! HQSoftware has a team of skilled professionals ready to tackle the project. Let’s talk! Anna Halias Business Development Manager Get a Free Quote
In an ideal world, all suppliers would have compatible systems that seamlessly integrate with your WMS. However, in reality, you may encounter scenarios where a vendor relies on Google Spreadsheets for inventory tracking or where having a large number of suppliers makes collaboration within a single WMS challenging.
Well, we know several examples of WMSs that include a separate platform for onboarding and communicating with suppliers. We’ve developed such a platform as well . It enables a US retailer to connect with all suppliers in a single interface. Here, suppliers can upload product catalogs, manage item availability, and set prices, while the customer can place purchase orders and establish collaborative agreements.
An important feature of this platform is its ability to handle various data formats, enabling suppliers to post catalogs in their preferred format, which was quite a challenge for our development team. We also ensured system scalability, enabling the customer to expand their network of suppliers.
With this platform, the customer now enjoys seamless order placement, improved supply management, and a 37% reduction in product delivery delays.
The process of publishing and updating items on a single marketplace is relatively straightforward. You fill out the product details, add images, and configure display settings. This is true for several products or catalogs hosted on a single platform. But when you’re a 3PL provider responsible for hosting hundreds of clients with thousands of items on multiple marketplaces, it’s more like a nightmare.
Therefore, for one of the 3PL providers, the HQSoftware team has developed a module for the company’s custom supply chain software system that can automatically publish and update catalogs on several marketplaces and allows for manual item updates within one interface. By synchronizing with the customer’s system, the module ensures consistent and accurate data across platforms.
Within the module, the customer can also customize the display of different products according to specific parameters, such as particular display times, different prices for different times of the day, etc. With robust data exchange mechanisms implemented by our team, the module seamlessly uploads files with all data, speeding up product management tasks by 30%.
Even if you’re not a 3PL provider, such a feature can greatly simplify marketplace management. You no longer have to manually navigate through each product listing on every platform to make changes. All this can be done with a few clicks through a user-friendly interface.
Based on the expertise we’ve gained from our WMS implementation case studies, we understand that leveraging the advantages of WMS software takes more than simply finding or developing a suitable system. It’s also important to focus on proper WMS implementation . Consider the following actions.
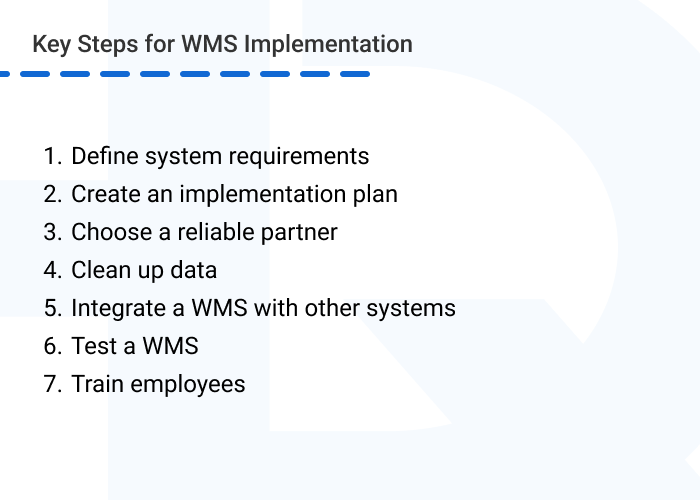
- Define system requirements . Conduct a thorough analysis of your warehouse operations to understand how a new system can automate and improve established processes. This analysis will help you define the specific requirements for your WMS.
- Create an implementation plan. The step-by-step plan will help you overview the whole cycle of WMS implementation and control the progress. A common WMS implementation project plan example includes several key phases, starting with planning, then analysis, then implementation, testing, training, and finally, deployment.
- Clean up data. It’s a good idea to get rid of outdated or duplicate information that can lead to errors and slow down the process of migrating data to the new WMS.
- Integrate a WMS with other systems. This greatly enriches WMS functionality and allows you to get valuable insights from both internal and external platforms.
- Test a WMS. Verify that the system can process all your data smoothly without any interruptions or delays. It is important to test the system’s interaction with third-party systems and ensure it meets the needs of end-users.
- Train employees. Comprehensive training ensures that your employees know how to use the system effectively and helps overcome potential resistance to change. Create visual and interactive manuals and step-by-step tutorials that employees can refer to when they encounter difficulties.
But one of the most important factors in successfully implementing a WMS is choosing a reliable and trusted WMS provider, especially if you opt for a custom WMS. The capabilities of your system and its successful implementation will depend directly on the expertise of your development partner.
At HQSoftware, we have extensive experience not only in creating comprehensive WMS systems but also in working with cutting-edge technologies that can enhance WMS functionality, such as Artificial Intelligence , Machine Learning , IoT , etc. Contact us to learn more about our WMS development services.
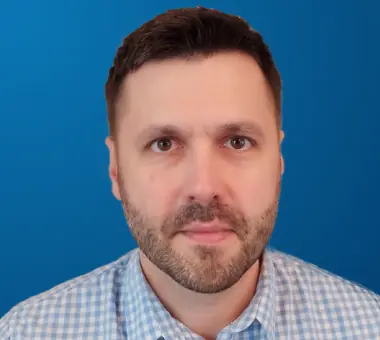
Head of Production
To ensure the outstanding quality of HQSoftware’s solutions and services, I took the position of Head of Production and manager of the Quality Assurance department. Turn to me with any questions regarding our tech expertise.
Related Posts
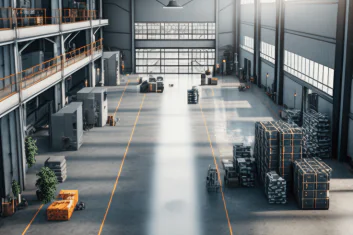
Your Name *
Your Email *
How Can We Help You? *
* Required Fields
Attach File
NDA required
I accept your privacy policy *
We are open to seeing your business needs and determining the best solution. Complete this form, and receive a free personalized proposal from your dedicated manager.
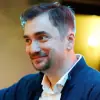
Sergei Vardomatski
We use cookies to analyze traffic, personalize site content, and for social media features. We share this data with our ad and social media partners. You can change your cookie settings and learn more here. By browsing the website you consent to our rules.
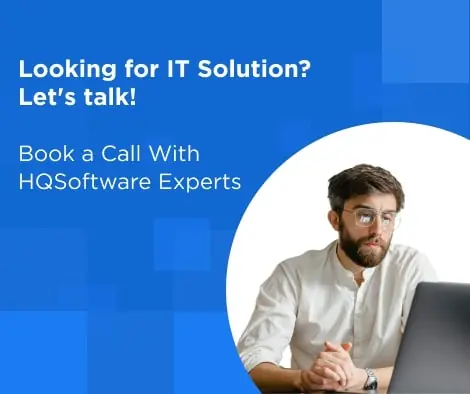
To read this content please select one of the options below:
Please note you do not have access to teaching notes, improving the effectiveness of warehousing operations: a case study.
Industrial Management & Data Systems
ISSN : 0263-5577
Article publication date: 1 December 1999
The warehouse is the interface area for production lines, market, customers and suppliers, and the business environment in general. Goods inwards (GI), constituting part of the warehouse activities, is the department responsible for booking‐in the incoming parts from external suppliers. After the production process is improved, the resources in the warehouse are balanced to link the internal/ external transfer of physical items. With a broader view of the GI activities, and a look into its future, the actual problems may become clear, understandable, and hence easy to solve. The aim of this paper is to study the problem areas in GI and provide solutions to increase the performance of warehousing operations. First, a conceptual framework has been developed to improve the effectiveness of warehousing operations. Second, a case study has been conducted with the help of the model to minimize the through‐put time in warehousing operations. Finally, a summary of findings and recommendations are presented.
- Warehousing
- Case studies
- Through‐put time
- Just‐in‐time
Gunasekaran, A. , Marri, H.B. and Menci, F. (1999), "Improving the effectiveness of warehousing operations: a case study", Industrial Management & Data Systems , Vol. 99 No. 8, pp. 328-339. https://doi.org/10.1108/02635579910291975
Copyright © 1999, MCB UP Limited
Related articles
We’re listening — tell us what you think, something didn’t work….
Report bugs here
All feedback is valuable
Please share your general feedback
Join us on our journey
Platform update page.
Visit emeraldpublishing.com/platformupdate to discover the latest news and updates
Questions & More Information
Answers to the most commonly asked questions here

Read our customer success stories
Read on to understand how Hopstack's customers improved its warehousing and fulfillment activities, and grew their businesses while minimizing operational costs.
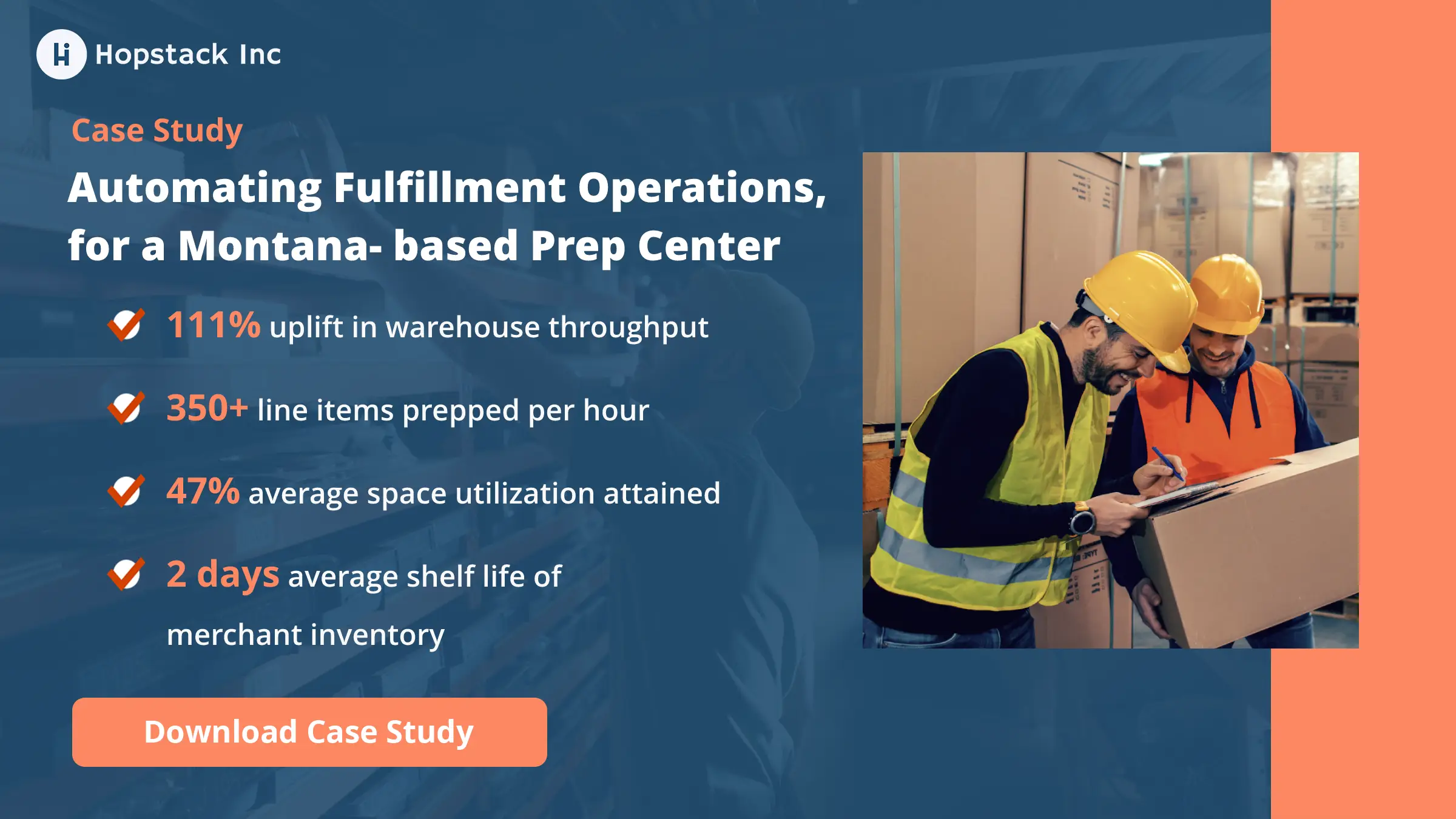
Automating Fulfillment Operations, for a Montana-based Prep Center
Here's how Hopstack transformed this Prep Center's inbound, prepping, and outbound operations and helped improve the merchant experience.
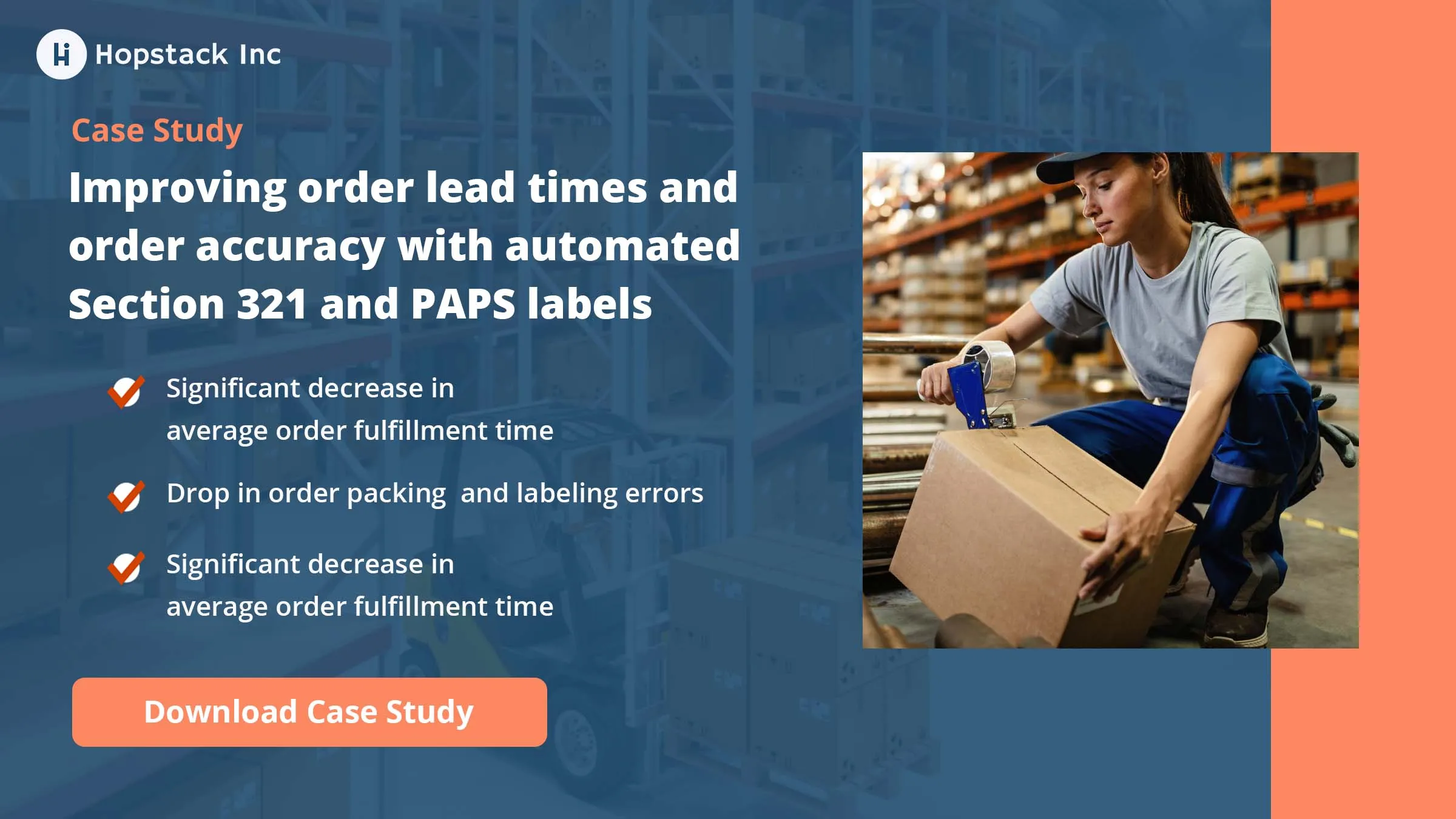
Enabling Section 321 and PAPS for North American Brands for International Fulfillment
Here’s how Hopstack enabled this North American consumer retail brand to automate the packing and labeling process around Section 321 and PAPS and make its cross-border fulfillment more efficient.
.webp)
Solving Combined Orders for North America’s Brands and Fulfillment Providers
Here's how Hopstack's algorithmic and highly flexible 'Combined Orders' functionality helped this North American luxury consumer goods seller cut down packaging and shipping costs and improve order lead time.
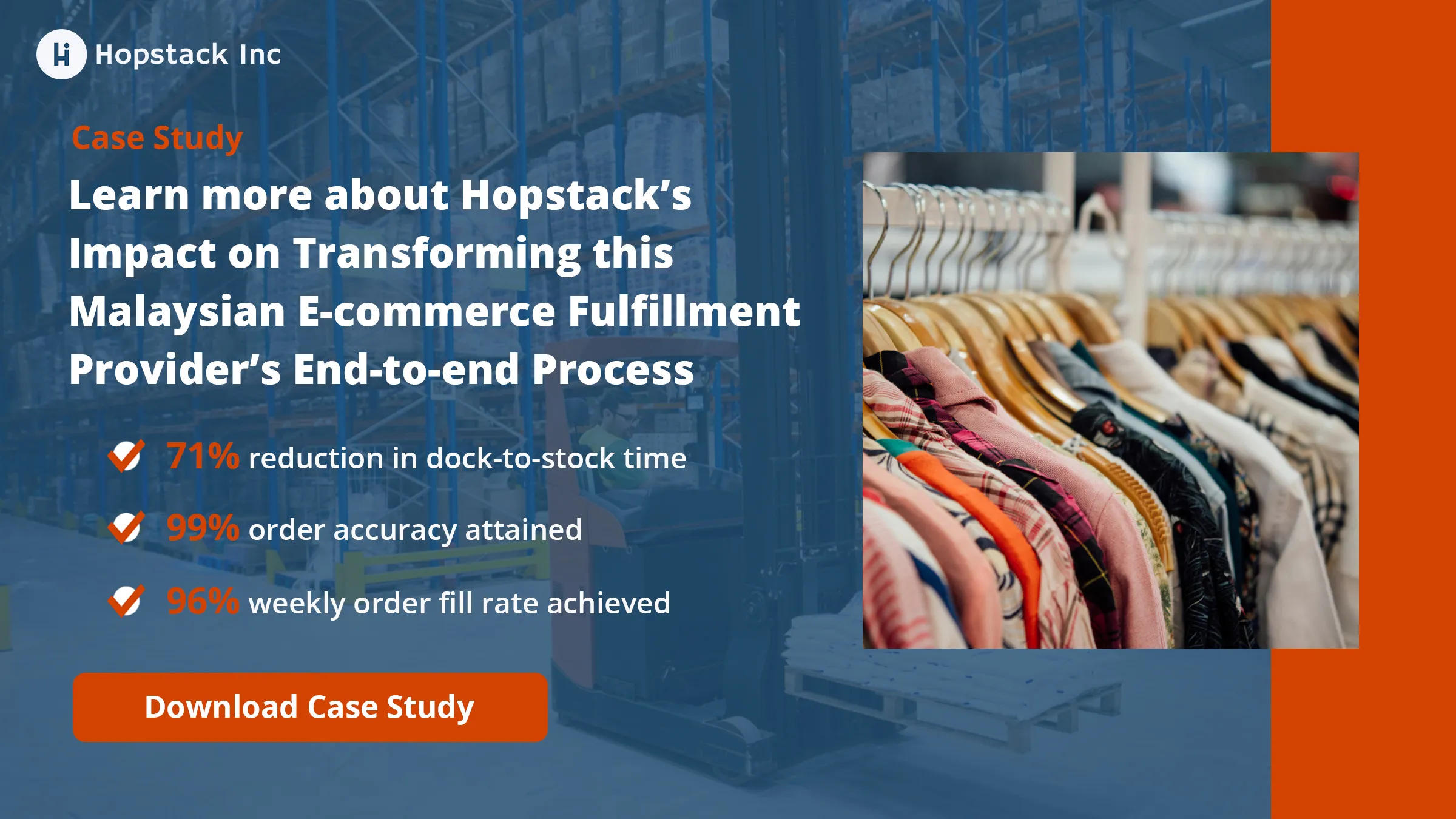
How this Apparel-Focused Malaysian Ecommerce Fulfillment Provider Transformed its End-to-End Process using Hopstack
How one of the fastest growing 3PLs in Malaysia improved performance visibility and transformed its end-to-end inbound and outbound processes to better serve its fast-fashion customers.
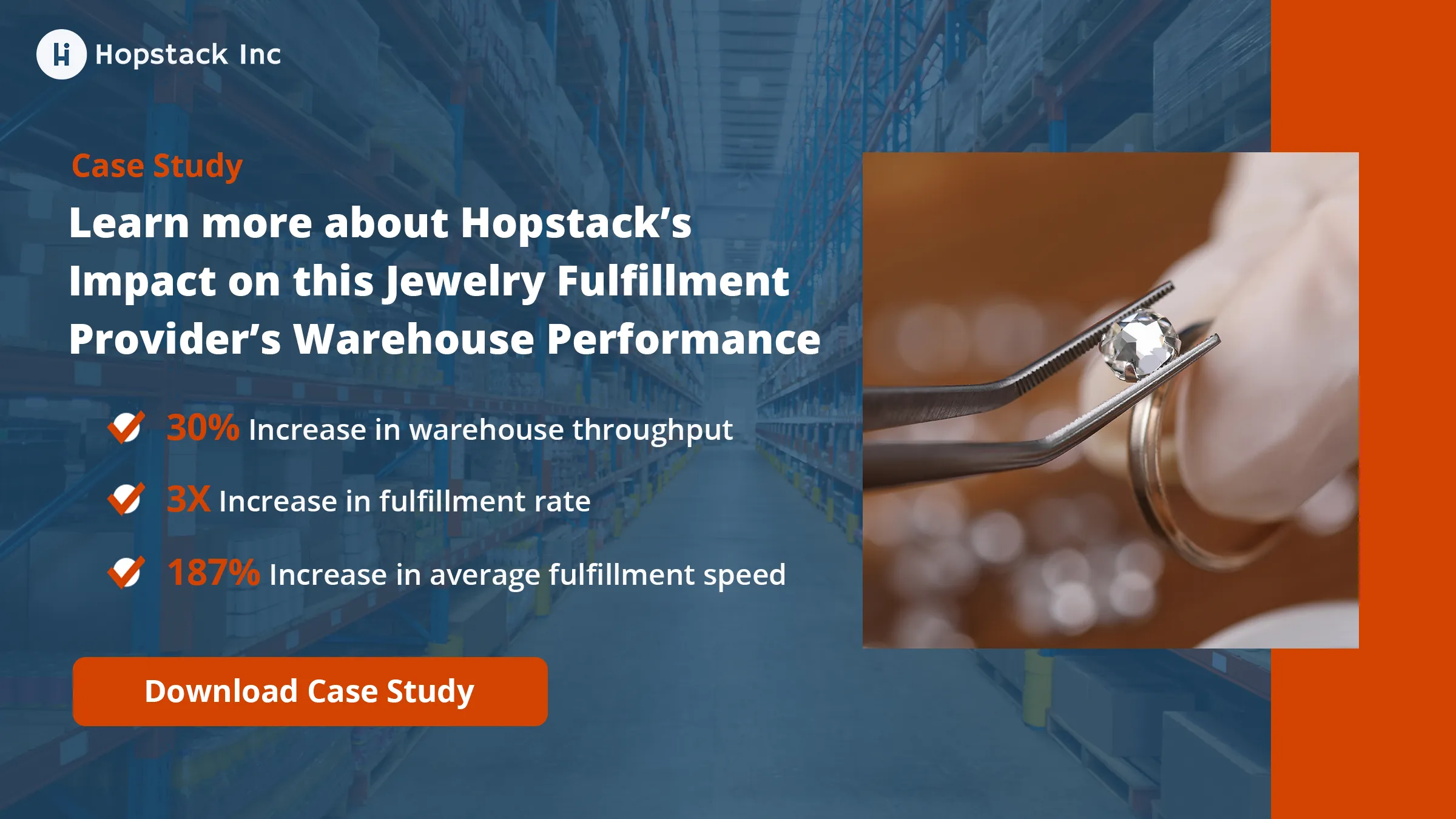
How this Jewelry Fulfilment Provider Grew its Warehouse Throughput by 30%
How one of the leading jewelry fulfilment providers solved the challenge of peak seasonal demand by replacing manual processes with Hopstack's warehouse automation and execution system.
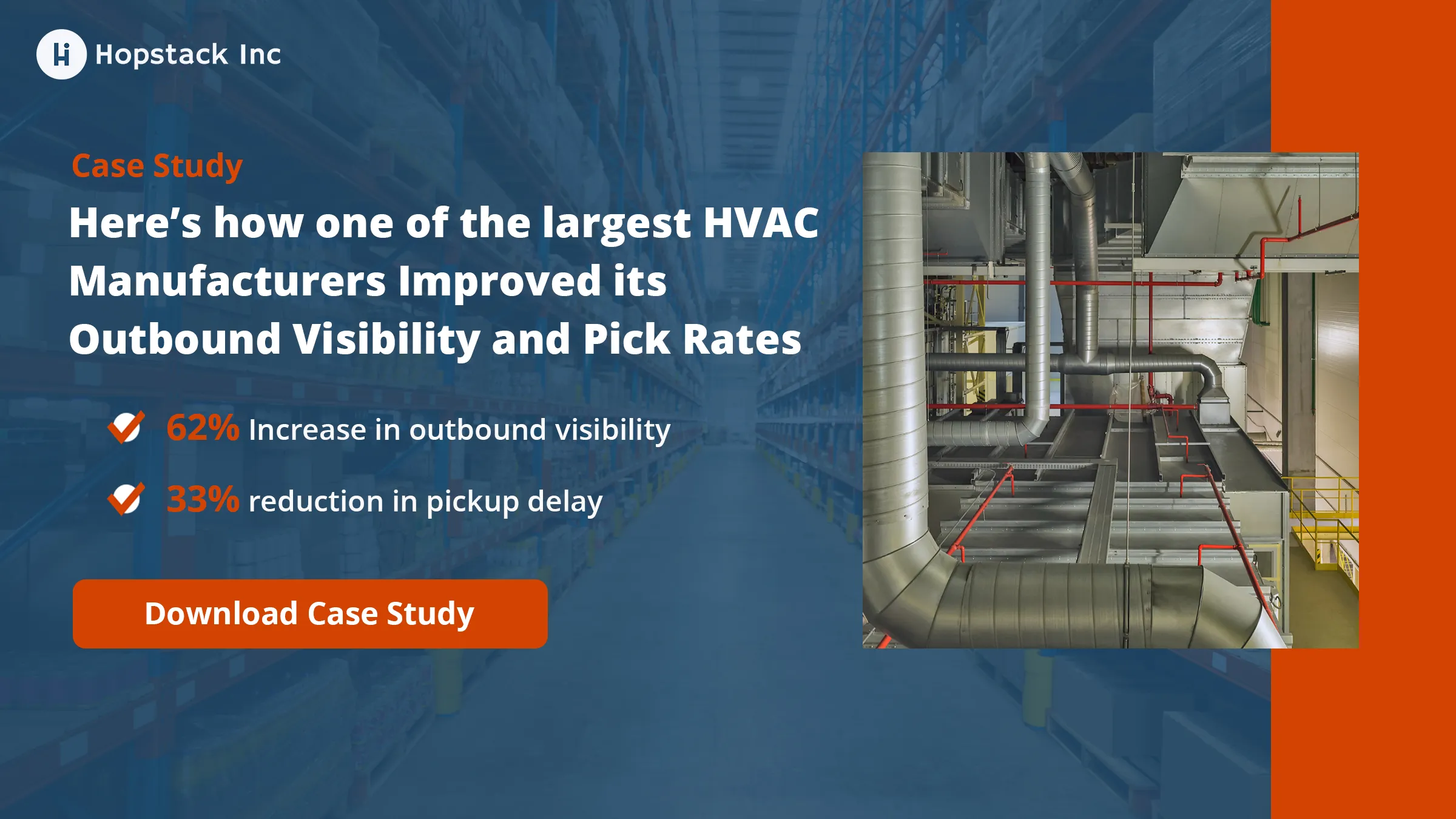
How Hopstack Helped this HVAC Manufacturer in Increasing the Outbound Visibility by 62%
How one of the world's largest HVAC (Heating, Ventilation, and Air Conditioning) manufacturers adopted Hopstack's Digital Warehouse platform leading to 62% increase in outbound visibility and 25% reduction in pickup delay.
What is Warehouse Management? Benefits, Processes, & Strategies

Any business that stores items in a warehouse knows that effective management is the difference between fulfilling customer orders quickly and accurately while keeping costs down versus hearing complaints about delayed or inaccurate shipments and higher operating costs.
Video: What Is a Warehouse Management System?
What is warehouse management.
Warehouse management encompasses the principles and processes involved in running the day-to-day operations of a warehouse. At a high level, this includes receiving and organizing warehouse space, scheduling labor, managing inventory and fulfilling orders. Zoom in closer and you’ll see that effective warehouse management involves optimizing and integrating each of those processes to ensure all aspects of a warehouse operation work together to increase productivity and keep costs low.
Benefits of Warehouse Management
Warehouse operations are generally invisible to customers, but they play a vital behind-the-scenes role in ensuring on-time delivery. To achieve this goal, good warehouse management ensures all warehouse processes run as efficiently and accurately as possible. For example, warehouse management involves optimizing the use of warehouse space to maximize inventory storage; making inventory easy for staff to find; ensuring adequate staffing; efficiently fulfilling orders; and coordinating communication with suppliers and transportation companies so materials arrive and orders ship on time.
The benefits of good warehouse management—namely fast, high-quality service at low cost—can ripple out to the entire supply chain, strengthening relationships with suppliers as well as customers.
But given the many elements involved, optimizing warehouse management can be a complex task. That’s why many organizations are turning to warehouse management systems for help.
What Is a Warehouse Management System?
A warehouse management system (WMS) is a software solution that aims to simplify the complexity of managing a warehouse. Often provided as part of an integrated enterprise resource planning (ERP) suite of business applications, a WMS can support and help to optimize every aspect of warehouse management. For example, a WMS can:
- Leverage data and automation to conduct demand analyses, forecast sales and create efficient daily operating plans.
- Provide real-time insight into inventory location and quantity.
- Share data with other ERP modules or standalone software products, such as accounting software and transportation management solutions, to increase the efficiency of business operations.
- Monitor and report productivity to offer a deeper understanding of how efficiently your warehouse is operating and where you can make improvements to warehouse geography and optimize space.
- Create step by step directions to guide users through daily processes—such as receiving, picking and packing orders—using predefined rules.
Inventory Management vs Warehouse Management
Before getting into the details of warehouse management, it may help to understand a few common terms. For example, the terms inventory management and warehouse management are often used interchangeably, but there are key differences:
Inventory management
Inventory Management is centered on efficiently and effectively ordering, storing, moving, and picking the materials needed to make products or fulfill orders.
Warehouse management
Warehouse Management is a broader term that includes other aspects of warehouse operations, such as warehouse organization and design, labor, order fulfillment, warehouse monitoring and reporting.
Stock Management
Stock management is often used as another term for inventory management, but it’s important to recognize the difference between “stock” and “inventory,” particularly for companies involved in manufacturing products. Stock generally refers to finished product ready for sale or distribution. Inventory, however, includes everything in the warehouse: raw materials, materials that are in the process of being built into products and finished products (stock).
Stock management is therefore a subset of inventory management that focuses specifically on holding as little stock as possible—to save space and costs—while still being able to meet customer demand.
Principles of Warehouse Management
Understanding the general principles of warehouse management can help you focus your efforts to optimize the way your warehouse operates. These principles include:
Know your purpose . A warehouse operation must first and foremost know its objectives. For example, do your customers have specific delivery requirements? Does your inventory need specialized storage? Additionally, all warehouse operations aim to use warehouse space, labor and equipment as efficiently as possible.
Comprehensive control. Warehouse management involves coordinating complex processes involving many moving parts: people, equipment, orders and inventory. Warehouse managers need to be able to track each process in order to ensure it’s running smoothly and solve the problems that inevitably occur. Quality control is critical to ensure orders are fulfilled accurately.
Flexibility and resilience. Warehouse managers have to be able to change plans on the fly, whether it’s because materials have arrived damaged or because inclement weather is delaying shipments. It’s also important to be able to adjust workflows to maximize efficiency, whether that involves rearranging warehouse space or reimagining picking processes.
Customer focus. On-time delivery, with the correct product, is one of the most important metrics when it comes to customer service and satisfaction. To deliver on time, you need to be able to fulfill orders quickly and accurately.
Data-driven decision making . Even if every warehouse process appears to be running without a hitch, it doesn’t mean processes are operating as efficiently as possible. A WMS can help you pinpoint and analyze areas that need improvement.
Warehouse Management Processes
Warehouse management includes six core processes. Each process influences the efficiency of the next, so every step must be optimized for the warehouse operation to run like a well-oiled machine:
- Receiving. Check in and log incoming items. Verify that you’re receiving the right quantity, in the right condition, at the right time.
- Put-away. Move items from the receiving dock to their correct storage locations.
- Storage. Safely store and logically arrange inventory to enable fast and accurate picking.
- Picking. Collect the items needed to fulfill sales orders.
- Packing. Prepare the picked items for shipment. They must be safely packed into the correct packaging with an accurate packing slip.
- Shipping. Send out the finalized sales orders, ensuring that they are on the right vehicle, at the right time, with the correct documentation, so customers receive their orders on time.
Warehouse Optimization
Optimizing your warehouse operation involves fine-tuning each of these warehouse management processes. For example, when receiving goods, an organization can label items with mobile barcodes or attach RFID tags to make them easier to find when picking. During put-away, a well-managed warehouse operation stores items in the minimum amount of space to maximize the capacity of the warehouse. Other best practices for warehouse optimization include storing popular items in easily accessible areas and separating items that can easily be mistaken for one another.
Warehouse Management Fulfillment Strategies
Selecting fulfillment strategies that match the business’s size and the volume and type of orders it receives can help the organization ship products faster, minimize waste and improve customer satisfaction. Applying picking strategies that match the type of orders that you receive can help maintain the most effective workflow. For example:
- Batch picking is a technique that can help you quickly fulfill multiple orders for the same product without wasting time by continually revisiting the same inventory location.
- Zone picking assigns pickers to different zones of SKUs. For each order, pickers are resonpsible for picking all SKUs from their designated zone.
- First expired, first out (FEFO) picking ensures perishable products and items make it to customers before specified expiration or sell-by dates. With FEFO, the products set to expire first are shipped first.
- First in, first out (FIFO) picking ensures the first products to come into the warehouse are the first to be distributed, which can help make sure older items are shipped before they can become obsolete.
Technology is also an important part of any warehouse management fulfillment strategy. Handheld mobile devices that display packing lists with item locations, serial numbers and lot numbers can help increase picking speed and accuracy. Software can recommend safe and cost-effective packing based on product dimensions to ensure each item gets shipped securely, with as little waste—and wasted space—as possible.
Warehouse Monitoring & Reporting
Measuring and tracking key performance indicators (KPIs)—operational statistics that indicate how well the warehouse is operating—can help pinpoint problems and highlight opportunities to improve efficiency and fulfill customer orders more quickly and accurately. For example, you can set a target for improved picking and packing accuracy, then make changes to your picking processes and measure whether those changes are effective in helping you achieve your goal.
Warehouse KPIs
Warehouse managers often track the following KPIs, among others:
- Receiving efficiency or productivity : The volume of goods received per warehouse operator, per hour. Higher scores indicate greater receiving efficiency, while lower scores indicate that there may be problems that should be investigated.
- Picking accuracy : The number of orders accurately picked divided by the total number of orders picked (including incorrect or short orders). The closer to 100% accuracy, the better.
- Order lead time : The average time it takes for an order to reach a customer once the order has been placed. For the highest customer satisfaction, the shorter the lead time, the better.
- Rate of product return : The rate at which sold goods are returned by customers, calculated by dividing the number of items returned by the number of items sold. To get a full picture of this KPI, it’s important to consider why products are being returned—a customer accidentally ordering the wrong product might not signify warehouse operation issues, but there is room for improvement if customers often receive incorrect products or damaged goods.
- Inventory turnover : How much inventory is sold and replaced in a given period of time. It’s calculated by dividing the total cost of goods sold during the period by the average cost of inventory during that period. This KPI reflects how efficiently a warehouse manages inventory to meet demand. In general, higher inventory turnover is better. If a warehouse overestimates demand, inventory turnover may be low. Too much slow-selling inventory can be costly—especially for businesses dealing with goods that have a predetermined shelf life.
Award Winning Warehouse Management Software
Warehouse Management Statistics
Global ecommerce has grown rapidly in recent years, and is expected to top $29 trillion by 2023 —accelerating a need for more warehouse space to match growing consumer demands. Ecommerce growth is expected to increase demands for U.S. warehouse space by 1 billion square feet by 2025. It’s not surprising that one survey, by trade publication Logistics Management , found 79% of warehouse operations were planning some type of expansion plan.
Given this growth, a top challenge faced by warehouse operations is the inability to attract and retain a qualified hourly workforce. To improve productivity, reduce operating costs and keep up with customer demand—all while combatting tight space and a tight labor market—warehouse operations are increasingly using technology to automate processes, with 85% using WMS according to the Logistics Management survey.
Choosing a Warehouse Management System (WMS)
Choosing the right WMS will depend on the specifics of your warehousing operation and what you want to achieve. Above all, the right WMS should help your organization achieve greater efficiency and fulfill orders more accurately so you can do more at a lower cost. Since a primary goal is to save money, ROI is key.
Additionally, a WMS should act as a guide to help all warehouse staff become more efficient in the workplace. To do so, the right WMS will provide real-time actionable insights into each aspect of your warehousing operation to help staff be more efficient and programmatic, including receiving, shipping, inventory, order fulfillment, and labor—while providing easy-to-understand statistics and reports that managers and workers can easily understand and then use to improve daily and long-term processes. A WMS should also be scalable so it can help your business grow and adapt to changing market conditions.
The right WMS can take your warehouse operations to a higher level of efficiency, speed and order accuracy, helping to improve your company’s competitiveness and increase customer satisfaction while keeping operating costs down.
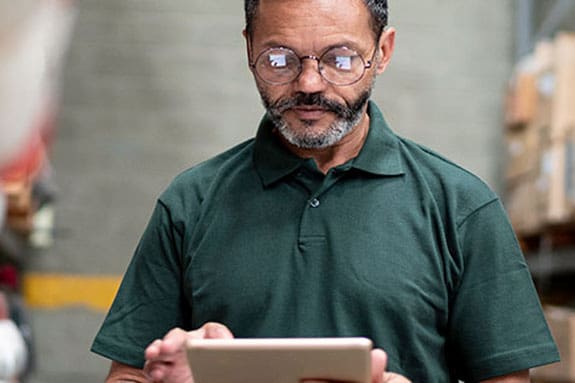
What Is a Warehouse Management System (WMS)?
In an era of booming global digital commerce, the limits of traditional warehouse management processes are constantly tested. To keep up with customer expectations for fast, accurate, on-time shipping—without…

Trending Articles
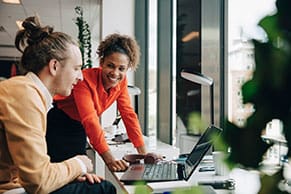
Learn How NetSuite Can Streamline Your Business
NetSuite has packaged the experience gained from tens of thousands of worldwide deployments over two decades into a set of leading practices that pave a clear path to success and are proven to deliver rapid business value. With NetSuite, you go live in a predictable timeframe — smart, stepped implementations begin with sales and span the entire customer lifecycle, so there’s continuity from sales to services to support.
Before you go...
Discover the products that 37,000+ customers depend on to fuel their growth.
Before you go. Talk with our team or check out these resources.
Want to set up a chat later? Let us do the lifting.
NetSuite ERP
Explore what NetSuite ERP can do for you.
Business Guide
Complete Guide to Cloud ERP Implementation
- Our Industry Solutions
- Our Logistic Solutions
- Our Customer Solutions
- Our Additional Services
- Cruise Control Login
- Shipment information
- About us About us
- Career Career
- Insights Insights
- Contact Contact
Case Study | Warehouse Management
Case study about the Warehouse Management at Fr. Meyer's Sohn
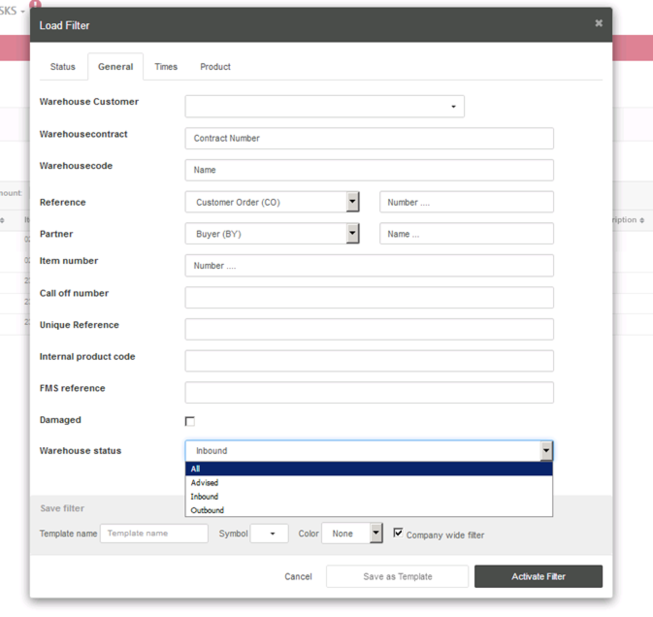
Initial Situation
Late 2019 one of the world’s largest paper producer approached FMS to set up a warehousing solution in Los Angeles | USA for large tissue paper rolls being imported from the Far East. One of the key customer requirements was providing real-time reporting on inventory status of each individual paper roll and on paperwork such as receiving reports and packing lists for trucks shipped from the warehouse.
The Warehouse module in Cruise Control FMS fitted the customer expectations and in January 2020 first containers started to arrive at our warehouse.
At that time the volume was forecasted at 40 containers per month. But then COVID-19 happened. Quickly the demand for tissue paper exploded and more inventory in the US was needed to support Just-in-Time deliveries demanded by service sensitive US buyers.
Within 6 months FMS set up additional warehousing solutions near the ports of Houston, Norfolk and New York, all covered by Cruise Control. The monthly volume has increased to 250 import containers per month.
The customer’s US based sales & logistics team uses the Cruise Control platform for all communications regarding warehouse receiving, inventory reports, packing lists, and Proofs of Deliveries (POD) to final receivers.
The customer is now calling us the one-stop-shop for all his tissue paper warehousing needs in the US.
We are happy that our tools make life easy for our customer. Would you like more information? Write a mail to our Cruise Control Team
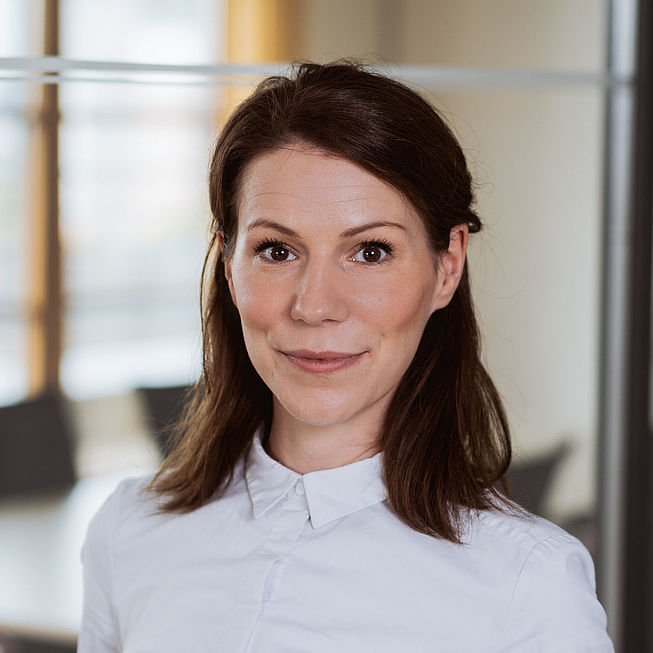
Corporate Head of Marketing at Fr. Meyer's Sohn
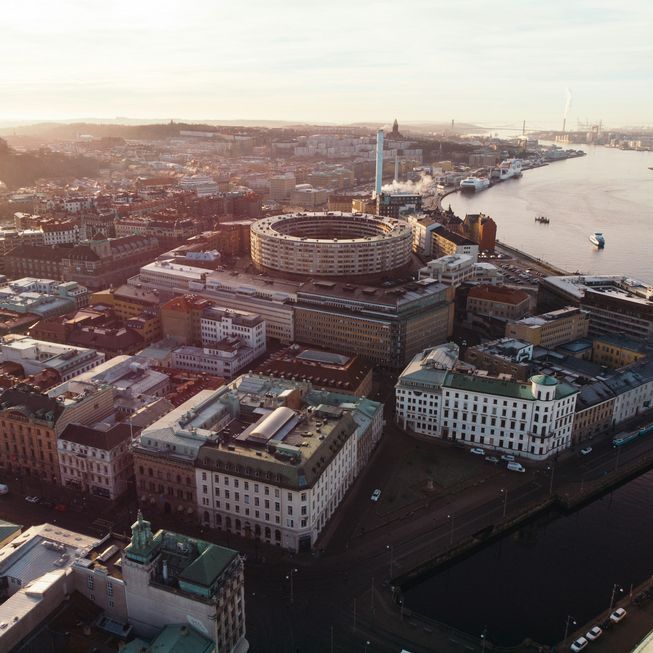
Fr. Meyer's Sohn strengthens its network in Northern Europe. The Hamburg-based logistics company has completed the acquisition of the Swedish freight fowarder C Land Logistic.
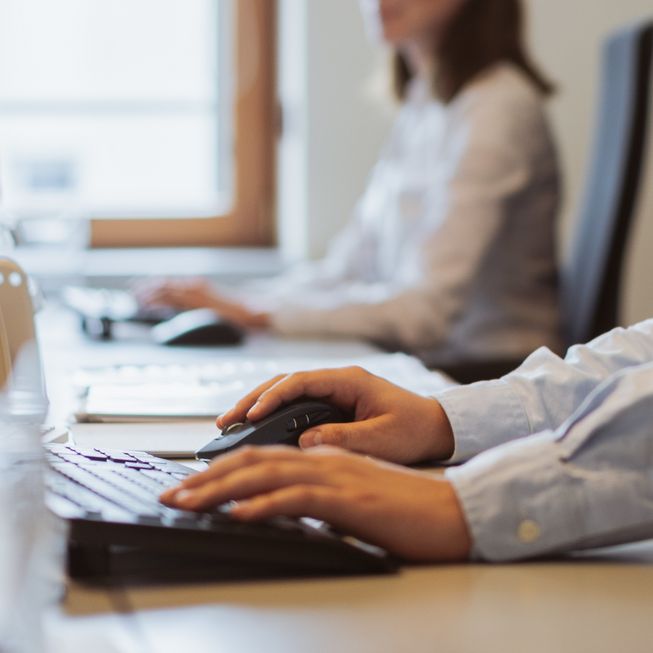
Streamlining Information Extraction with GPT-Powered Solution through our partner theBlue.ai GmbH.
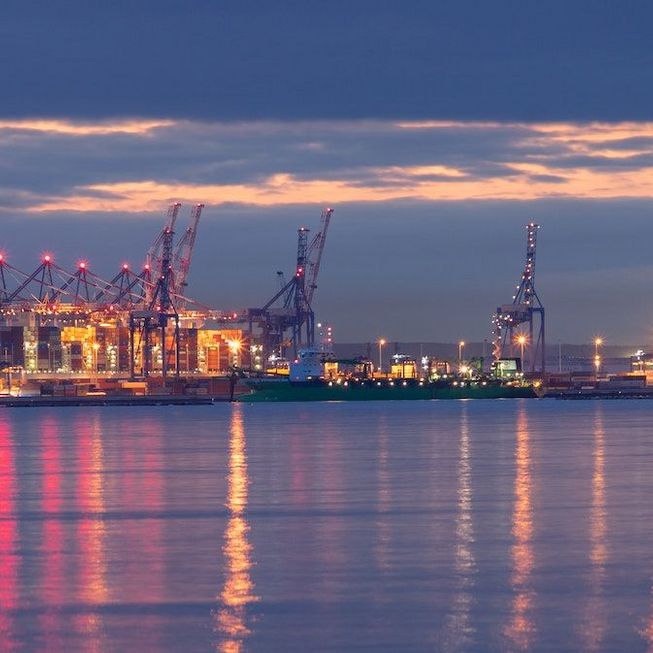
Opening of FMS Gdansk | Poland
- Contact sales
Start free trial
How to Improve the Warehouse Operations of Your Organization

The better a business’ warehouse operations, the more successful the business is. Warehouse management ensures that stock matches customer demand. Warehouse operations take into account the supply chain and work towards being cost-effective and efficient.
To understand effective warehouse operations, you must first be clear on the warehouse operations process and how it plays into the larger warehouse operations management. Read about that and how to improve the efficiency of warehouse operations.
What Are Warehouse Operations?
Warehouse operations consist of the processes used when managing the activities associated with receiving, storing, packing and distributing goods in a company’s stockroom. This includes warehouse management systems (WMS), workflow processes, human and nonhuman resource management and more.
Warehouse operations aim to satisfy customer needs and requirements while optimizing space, equipment and labor as effectively as possible. That means that stored goods must be accessible and protected from damage. Achieving these goals requires ongoing planning and being able to quickly adapt to change.
Project management software can help manage the warehouse operations process to reach its objectives. ProjectManager is award-winning project and portfolio management software with powerful kanban boards that help control the inventory life cycle. Kanban boards can be set up to reflect the warehouse operations process, while kanban cards can capture data from individual orders. Each card can track planned versus actual progress, schedule resources and more to keep warehouse operations running smoothly. Get started with ProjectManager today for free.
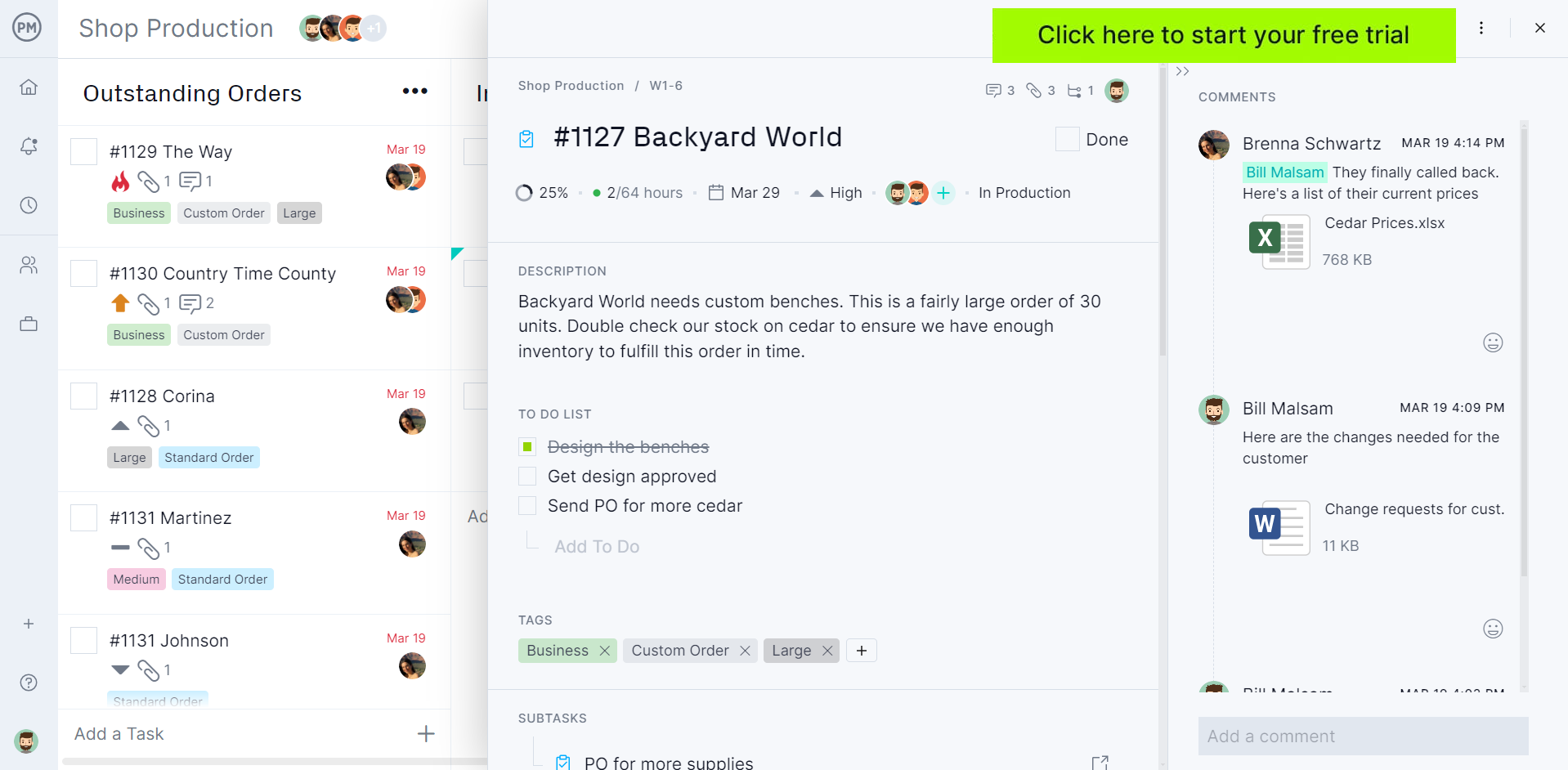
The Warehouse Operations Process
Project management software will help control the warehouse operations process. However, this requires an intimate understanding of the warehouse operations process. There are six fundamental processes to warehouse operations: receiving, storing, picking, packing, shipping and returning. Being able to optimize these seven processes streamlines warehouse operations and reduces costs and errors, which leads to a higher perfect order rate.
This is the first warehouse operations process, also one of the most important to perform properly. It starts by verifying that the right product in the right quantity and without damage was delivered. The responsibility of the goods is then transferred to the responsibility of the warehouse, which is now tasked with maintaining the condition of the goods as received until shipped. Doing this allows warehouses to filter out damaged goods and avoid liability.
Once received, the goods must be taken from the receiving dock to their warehouse storage location. Not putting goods in their proper place interferes with warehouse operations and reduces productivity. Putting away goods also allows them to be stored more efficiently, reduces travel time, ensures safety for goods and employees, utilizes space better and makes it easier to find, track and retrieve when needed.
This leads to the next warehouse operations process, storing the goods. Put-away moves the goods from where they’re received to the warehouse. Storing is finding the opportune site to store each of the goods that are received. As noted, this helps optimize space and increase labor efficiency.
When a customer order comes in , goods must be retrieved, which is the picking process in warehouse operations. This is the most expensive process in warehouse operations and can be over half of the total operating expense for the warehouse. Therefore, being as efficient as possible with the picking process can save money and increase warehouse efficiency. Another advantage of streamlining the picking process is it increases accuracy as errors negatively impact customer satisfaction.
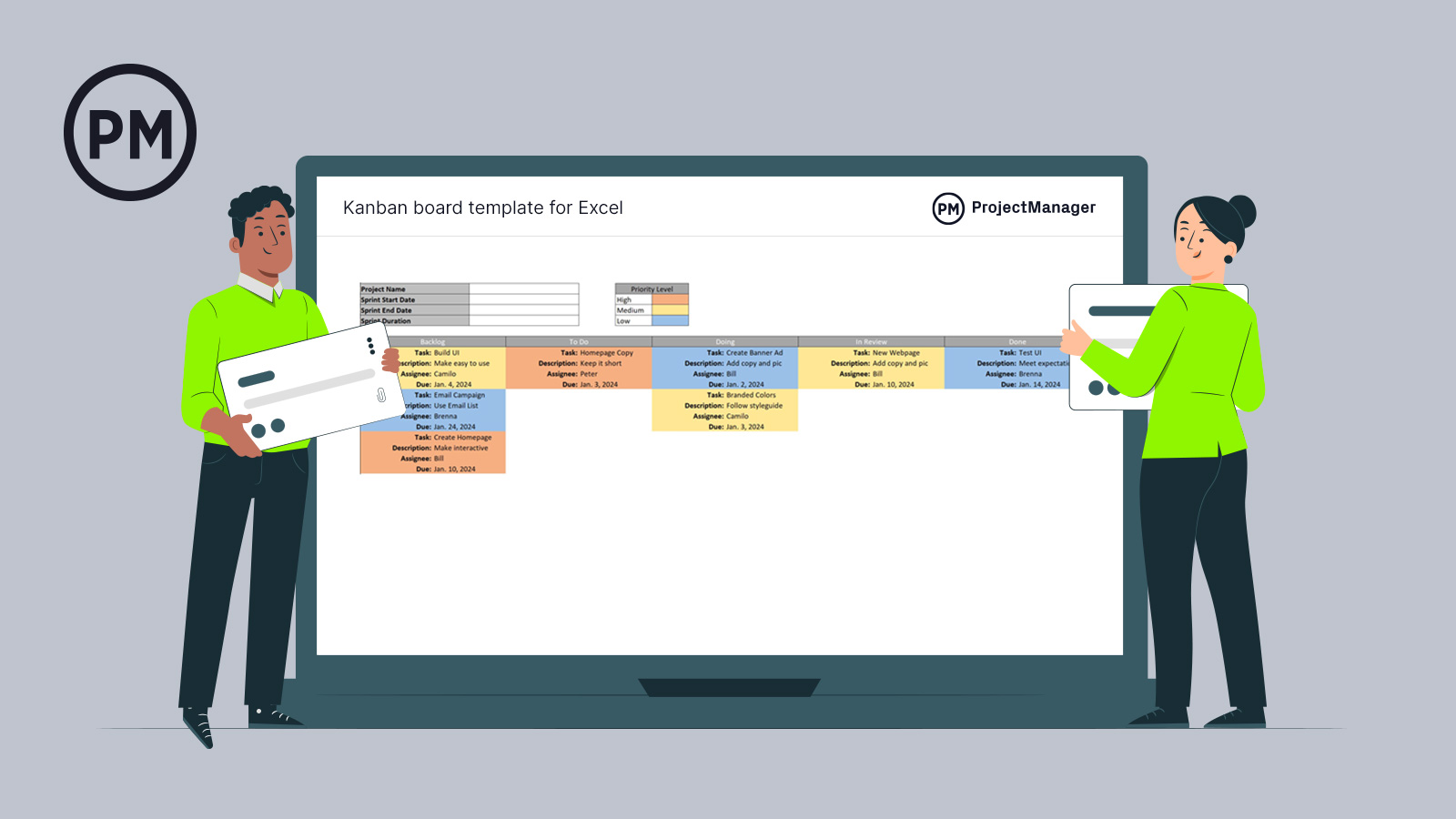
Get your free
Kanban Board Template
Use this free Kanban Board Template for Excel to manage your projects better.
Once picked, the goods must be packaged. Packing is the consolidation of picked goods from the customer’s sales order that’s then prepared for shipment, such as putting them in boxes and adding address labels. It’s important to avoid damages during this process and when packing use lightweight materials that protect the goods but don’t add undue costs to shipping.
The final step in the warehouse operations process is shipping (unless goods are returned, but we’ll get to that in a moment). If all the other processes have been done correctly, all that’s needed is to ensure that the package is delivered to the right address and customer when it’s expected and without damage. Also, shipping should be as economical as possible for the shipper without impacting the delivery for the customer.
Occasionally, goods will be returned due to damage or an error. This process begins with the prior process. When shipping, a return label should be included in the packaging. Once the return is delivered to the warehouse, staff should inspect it for damage, review the reasons for its return and scan it back into the tracking system. If the item isn’t damaged or expired, it can be returned to its place in the warehouse, otherwise, it should be discarded or salvaged. Detailed records of this process should be kept.
What Is Warehouse Operations Management?
Warehouse operations management is simply the principles and processes involved in running the day-to-day operations of a warehouse. This includes all processes defined above, but also the scheduling of labor and the management of inventory and order fulfillment. Warehouse operations management seeks to have all these aspects of running a warehouse’s operations work together as efficiently as possible to increase productivity and reduce costs.
How to Improve the Efficiency of Warehouse Operations
It’s clear that improving the efficiency of warehouse operations is key to running a successful business, but what are some practical things that can be done to increase efficiency? Below are some of the things that warehouse operations will benefit from employing.
Use a Warehouse Management System
A warehouse management system is made to increase efficiency and accuracy in the warehouse operations processes. The software can be found in businesses working in retail space, distribution and manufacturing. That’s because the WMS improves the flow of goods through automation, which eliminates human error, reduces labor costs and can track orders.
Automate or Outsource Warehouse Operations
Automated workflows will help streamline warehouse operations processes, but businesses can also remove the entire process by partnering with a third-party vendor. This provides companies with a more experienced and likely better service at a lower risk to them. It can also reduce costs, help with compliance with current guidelines and keep organizations focused on their core strengths.
Use Kanban Pull System for Inventory Management
Kanban pull system is ideally suited for warehouse operations because of its lean approach similar to just-in-time stock control. It means that work starts only when the customer submits a purchase order . This is a visual workflow tool designed to reduce waste, minimize inventory levels to just what’s needed at the moment and improve inventory control. This leads to cost savings and greater efficiency and the dividends are more customer satisfaction.
Optimize the Warehouse Layout
The better a warehouse is laid out, the more streamlined its processes. The benefits include less time wasted having to retrieve or pick goods, quicker turnaround times and it gives a warehouse capacity to handle a larger volume of orders. All this leads to greater customer satisfaction as well as loyalty, as they appreciate getting orders on time and in good condition.
Implement Lean Manufacturing Principles and Techniques
Lean manufacturing is all about reducing waste and increasing productivity and customer satisfaction. Running a lead warehouse does all that by taking advantage of opportunities for improvement and focusing on value creation for customers. It streamlines warehouse operations processes. It’s based on the lean manufacturing principles of eliminating waste, reducing inventory levels and improving operational efficiency.
Warehouse Operations Roles and Responsibilities
Many warehouse professionals manage and run the warehouse operations processes. Each has a distinct role and responsibility, which together keeps the warehouse operating efficiently. The following are the three basic categories of people who ensure the warehouse is working as it should.
- Warehouse Operations Manager: Oversees all daily activities of the warehouse. As part of the supply chain , they must be adaptable, open-minded, have strong communication skills and build and manage a self-sufficient team.
- Warehouse Supervisor: Also oversees the general operations of the warehouse and its staff, including recording and maintaining inventory, advising receiving and shipping as well providing training. They work under the warehouse operations manager.
- Warehouse Workers: The team responsible for managing customer orders , overseeing and processing incoming stock, picking, packing and shipping orders as well as dealing with returns.
Why Are Warehouse Operations Important for Businesses?
As stated at the start, a company involved in selling goods lives and dies by the success or failure of its warehouse operations. It’s that important for business. It satisfies customer demand and builds customer loyalty. Effective warehouse operations will increase productivity and much more. Here’s a short list.
Order Fulfillment Process
The order fulfillment process starts with receiving a customer’s order and ends with delivering the goods to that customer. Along the way, goods are stored and managed to avoid overstocking and shortages. Warehouse operations play a critical role in this process, ensuring that orders are accurately picked, packed and prepared for shipping.
Supply Chain and Logistics Management
The warehouse is a bridge between production and distribution in the supply chain. Warehouses store goods after they’re produced or procured until they’re shipped to the customer. That shipping is where logistics management comes into play. It ensures that goods are delivered to the right place, on time and in proper condition, while keeping costs low and maximizing efficiency.
Inventory Management
A warehouse serves to store inventory, which is why inventory management is forever tied to warehouse operations. That’s because inventory management controls the warehouse operations process from order to storing and selling of goods. It manages supplies and the floor of raw materials from procurement to finished products in production .
Operational and Production Costs
Without managing warehouse operations, costs are likely to get out of control. Operation costs include the cost of the goods being made and stored, but also all operating expenses, called selling, general and administrative (SG&A) expenses. Production costs are direct and indirect costs from manufacturing a product, such as labor, raw materials, etc.
How ProjectManager Helps With Warehouse Operations Management
Considering the importance of warehouse operations, businesses seek the best software to help them manage the warehouse operations process. ProjectManager is award-winning project and portfolio management software with the features to plan, schedule and track warehouse operations activities in real time. Resource management tools and cost-tracking features ensure that warehouse operations stay within budget and customers receive their orders on time.
Plan, Schedule and Track Warehouse Operations Activities
Warehouse operations include activities such as receiving, storing, packing and shipping, to name only a few. Planning out those activities on a robust Gantt chart makes sure that all those tasks are organized and assigned. Managers can see the whole plan in one place but also link all four types of task dependencies to avoid delays. When the schedule is complete, set a baseline to capture it and associated costs. This allows managers to track the planned effort against the actual effort in real time to stay on schedule.
Manage Resources and Monitor the Costs of Warehouse Operations
To keep to that schedule requires constant monitoring. Human resources are responsible for the day-to-day warehouse operations and their tasks can be viewed in one place on the team page or color-coded workload chart. If someone is over- or underallocated, balance their workload to keep everyone working at capacity. For a high-level overview, toggle to the real-time dashboard , with easy-to-read graphs and charts showing time, costs, workload and more.

When more detail is called for, use the customizable reporting features . Reports on timesheets, project or portfolio status, variance, workload and more can be generated with a keystroke. All reports can be filtered to show only what’s important and then shared in a variety of formats with stakeholders to keep them updated.
ProjectManager is online project and portfolio management software that connects teams whether they’re in the office, in the factory or warehouse floor. They can share files, comment at the task level and stay up to date with email and in-app notifications. Join teams at Avis, Nestle and Siemens who use our software to deliver success. Get started with ProjectManager today for free.

Deliver your projects on time and under budget
Start planning your projects.
Manage consent
Details cookies, important margin product information.
CFDs are complex instruments and come with a high risk of losing money rapidly due to leverage. 65% of retail investor accounts lose money when trading CFDs with this provider. You should consider whether you understand how CFDs, FX or any of our other products work and whether you can afford to take the high risk of losing your money.
Cookie policy
Our websites use cookies to offer you a better browsing experience by enabling, optimising, and analysing site operations, as well as to provide personalised ad content and allow you to connect to social media. By choosing “Accept all” you consent to the use of cookies and the related processing of personal data. Select “Manage consent” to manage your consent preferences. You can change your preferences or retract your consent at any time via the cookie policy page. Please view our cookie policy and our privacy policy .
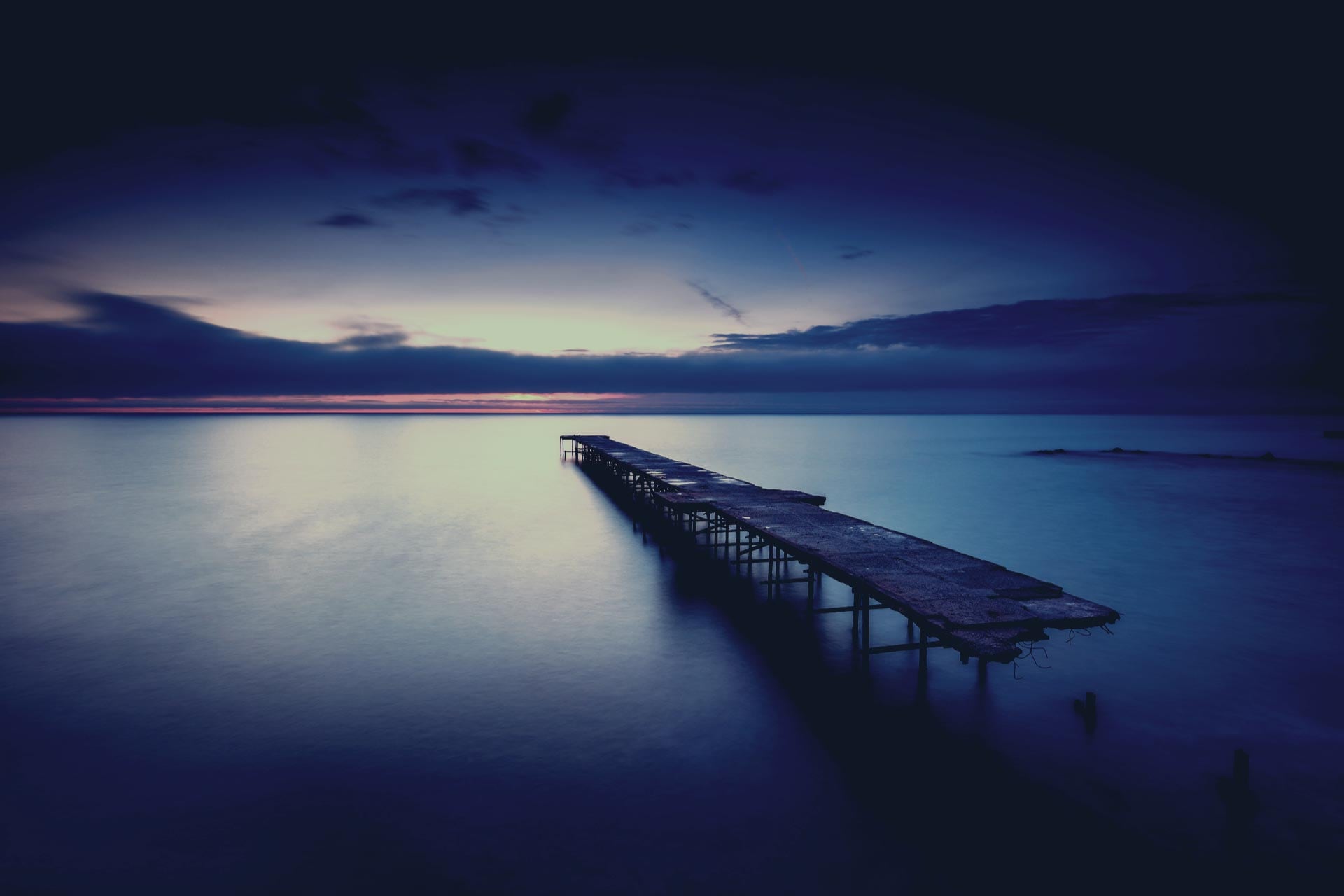
Case study: Smartly reducing your investment while maintaining market exposure
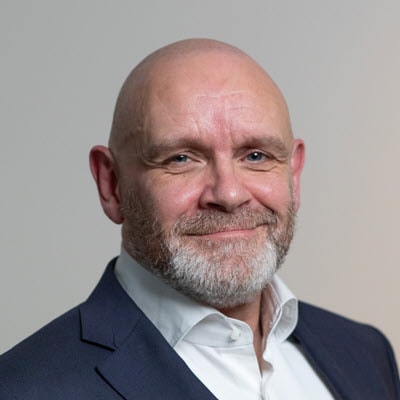
Koen Hoorelbeke
Options Strategist
Summary: This case study illustrates how Alex strategically employs long-term call options to both realize profits and maintain exposure to NVIDIA stock. By adjusting his holdings through these options, he secures gains while keeping potential for future growth, showcasing effective risk management and investment foresight.
Introduction:
In the dynamic world of investing, the ability to adapt strategies to changing market conditions is crucial for maximizing returns while managing risks. For buy-and-hold investors like Alex, who have seen substantial gains in certain stocks, the challenge often lies in realizing profits without losing potential future growth. This case study explores how strategic use of long-term call options can provide an innovative solution to this dilemma, allowing investors to secure gains and maintain market exposure simultaneously.
Background:
Meet Alex, an investor with a portfolio valued at $153,319, showing a profit of $44,534 from an initial investment of $108,785. His holdings include various stocks, but a significant portion of his profit comes from his investment in NVIDIA Corporation (nvda), which currently constitutes 55% of his portfolio's total value.
Alex's NVIDIA shares have appreciated significantly, and he's looking to realize some of these gains. However, he wants to maintain his market exposure to NVIDIA due to its potential for further growth.
Solution: Using a long-term call option:
To achieve his goals, Alex decides to buy a long-term call option on NVIDIA. This option will allow him to buy NVIDIA shares at a set price of $850 each anytime until the option expires in June 2025, regardless of how high the stock price goes. This option costs him $20,300 for one contract, which covers 100 shares.
Portfolio overview:
Here is a breakdown of Alex's current portfolio before any transactions:
- NVIDIA (nvda) : 100 shares at a buy price of $496, now valued at $847.2 each, totaling $84,720.
- Other holdings : Includes stocks like PayPal (pypl), Nike (nke), and Palantir (pltr), with various performances and allocations within the portfolio.
Financial mechanics simplified:
- Current stock position : Alex holds 100 shares of NVIDIA.
- Option purchase : The call option has a cost of $20,300 and provides similar market exposure to owning approximately 66 shares of NVIDIA.
How many shares can Alex sell?
By purchasing the call option, Alex can sell about 66 shares of NVIDIA without reducing his effective market exposure to NVIDIA's future price movements. This is because the option helps maintain a similar level of investment influence as the shares he plans to sell. Specifically, the call option has a delta of 0.66, which means that one contract of the option (covering 100 shares) effectively corresponds to the exposure of owning 66 shares of the stock (0.66 * 100 = 66).
- Reduced direct investment : Alex can reduce his direct exposure by selling 66 shares, which would secure approximately $56,000 (66 shares × $847.20/share). After accounting for the cost of the option ($20,300), the net amount secured is about $35,700. This allows him to use these funds for other investment opportunities or to diversify his portfolio further.
- Maintained market exposure : The long-term option ensures that Alex still benefits from potential price increases in NVIDIA's stock.
- Flexibility and security : This strategy allows Alex to lock in profits while keeping the flexibility to participate in future growth, providing a balanced approach to managing his successful investment.
While using long-term options can offer significant advantages, there are inherent risks to consider:
- Premium cost : The initial cost of the option ($20,300) is a sunk cost, meaning it is not recoverable if the option expires worthless. This represents a fixed loss if NVIDIA's stock price does not perform as expected.
- Volatility and time decay : Options are sensitive to changes in market volatility and lose value over time as they approach expiration — a phenomenon known as time decay. If NVIDIA's stock price remains below the strike price as the expiration date nears, the value of the option could decrease significantly.
Conclusion:
This approach allows Alex to capitalize on his gains in a high-performing stock while strategically maintaining his position for future growth. By using a long-term call option, Alex smartly adjusts his portfolio to reduce risk and secure profits, demonstrating a prudent method of portfolio management in a rising market. However, it's essential for Alex to consider the risks associated with options trading and monitor his investments accordingly.
Latest Market Insights
Fund selling exacerbates softening crude outlook
Technical Update - SP500 and Nasdaq 100 struggling to confirm uptrends. See here why
Special episode: How either US presidency may affect the financial markets
Bank of England preview: Rate cuts in mind, but patience required.
Grains see bumpy start to 2024 crop year
Technical Update - DAX/GER40 in confirmed uptrends with 3% upside potential. EuroStoxx50/EU50 testing resistance
Global Market Quick Take: Europe – 8 May 2024
Global Market Quick Take: Asia – May 8, 2024
Quarterly Outlook 2024 Q2
2024: The wasted year
Macro: It’s all about elections and keeping status quo
Markets are driven by election optimism, overshadowing growing debt and liquidity concerns. The 2024 elections loom large, but economic fundamentals and debt issues warrant cautious investment.
FX: The rate cut race shifts into high gear
As US economic slowdown hints at a shift away from exceptionalism, USD faces downside with looming Fed cuts. AUD and NZD set to outperform as their rate cuts lag. JPY gains on carry unwind bets and BOJ pivot.
Equities: The AI and obesity rally is defying gravity
Amid AI and obesity drug excitement, equities see varied prospects: neutral on overvalued US stocks, negative on Japan due to JPY risks, positive on Europe. European defence stocks gain appeal.
Fixed income: Keep calm, seize the moment
With the economic slowdown, quality assets will gain favour, especially sovereign bonds up to 5 years. Central banks' potential rate cuts in Q2 suggest extending duration, despite policy and inflation concerns.
Commodities: Is the correction over?
Commodities poised for rebound. The "Year of the Metal" boosts gold and silver, copper awaits rate cuts. Grains may recover, natural gas stabilises. Gold targets $2,300-$2,500/oz, copper's breakout could signal growth.
You can access both of our platforms from a single Saxo account. Preview platform Open Account
Disclaimer The Saxo Bank Group entities each provide execution-only service and access to Analysis permitting a person to view and/or use content available on or via the website. This content is not intended to and does not change or expand on the execution-only service. Such access and use are at all times subject to (i) The Terms of Use; (ii) Full Disclaimer; (iii) The Risk Warning; (iv) the Rules of Engagement and (v) Notices applying to Saxo News & Research and/or its content in addition (where relevant) to the terms governing the use of hyperlinks on the website of a member of the Saxo Bank Group by which access to Saxo News & Research is gained. Such content is therefore provided as no more than information. In particular no advice is intended to be provided or to be relied on as provided nor endorsed by any Saxo Bank Group entity; nor is it to be construed as solicitation or an incentive provided to subscribe for or sell or purchase any financial instrument. All trading or investments you make must be pursuant to your own unprompted and informed self-directed decision. As such no Saxo Bank Group entity will have or be liable for any losses that you may sustain as a result of any investment decision made in reliance on information which is available on Saxo News & Research or as a result of the use of the Saxo News & Research. Orders given and trades effected are deemed intended to be given or effected for the account of the customer with the Saxo Bank Group entity operating in the jurisdiction in which the customer resides and/or with whom the customer opened and maintains his/her trading account. Saxo News & Research does not contain (and should not be construed as containing) financial, investment, tax or trading advice or advice of any sort offered, recommended or endorsed by Saxo Bank Group and should not be construed as a record of our trading prices, or as an offer, incentive or solicitation for the subscription, sale or purchase in any financial instrument. To the extent that any content is construed as investment research, you must note and accept that the content was not intended to and has not been prepared in accordance with legal requirements designed to promote the independence of investment research and as such, would be considered as a marketing communication under relevant laws.
Please read our disclaimers: Notification on Non-Independent Investment Research (https://www.home.saxo/legal/niird/notification) Full disclaimer (https://www.home.saxo/legal/disclaimer/saxo-disclaimer) Full disclaimer (https://www.home.saxo/legal/saxoselect-disclaimer/disclaimer)
Your browser cannot display this website correctly.
Our website is optimised to be browsed by a system running iOS 9.X and on desktop IE 10 or newer. If you are using an older system or browser, the website may look strange. To improve your experience on our site, please update your browser or system.

IMAGES
VIDEO
COMMENTS
Successful WMS Implementation Case Studies. Warehouse Management Systems (WMS) represent a major investment in your supply chain and operational efficiency. While it can be difficult to gauge your estimated time to value, these four cases featuring enVista clients provide a warehouse management system business case and showcase outcomes after successful WMS implementations.
Warehouse management is becoming an increasingly important task and responsibility for employers whose goal is to maximize the profitability of the whole business. In this paper, a comparative analysis of warehouse processes was made on selected case studies of three companies by the methodology that is divided into several phases: the current ...
n Implemented a warehouse management system bringing the retail and e-commerce inventories together n Setting holistic productivity goals whilst being flexible with resource n Working with employees to continuously improve BENEFITS: n Inbound and outbound capacity almost doubled to 220,000 units daily n Online sales have more than doubled
Implementing Warehouse Management Systems (WM S) in Logistics: A Case Study 1 Natesan Andiyappillai, 2 Dr.T.Prakash 1 Senior Business Analyst, NFI Industries,1005 Laurel Oak Rd,Voorhees, NJ, 08043 ...
The Amazon Fulfillment Technologies (AFT) team builds and maintains the company's Warehouse Management Systems. Among these are Inventory Management Services (IMS), which facilitate warehouse processes, including inbound and outbound shipments, item picking, sorting, packaging, and inventory storage. These are essential for on-time delivery ...
Warehouse Simulation for Choosing Optimal Picking Algorithm. Kuehne+Nagel, a leading global provider of logistics solutions, was involved in planning a new warehouse for one of their clients. The warehouse would process 13K order lines or 750 picking cartons per day. The project included the development of the best algorithm for multi-order ...
Decathlon has chosen Mecalux's shelving for picking once again to manage its omnichannel logistics. After equipping its warehouses in France, Germany, Italy and Poland, it is Northampton's (UK) turn. With 35,000 SKUs, the warehouse preps and ships out 3,000 order... View case study.
In fact, digital warehouse-simulation tools could become a new way of setting performance expectations, with the tools embedded as part of the day-to-day management of each distribution center. Estimating daily performance targets based on daily volume, mix, and staffing can help warehouse managers manage the shift's performance more ...
Warehouse Management Software ( WMS) is like your personal assistant for managing the chaos of a warehouse. It's a fancy computer program that helps keep track of inventory, streamline processes, and make your life a whole lot easier. Think of it as the Hermione Granger of your warehouse - organized, efficient, and always on top of things.
Figure 4 shows that some countries in the world are behind in reporting Industry 4.0 technology implementation case studies in warehouse management. In Africa and North America, only one country has a relevant study. A part of Europe shows a slight increase compared to the previously mentioned continents in the studies of this topic.
Journal of Logistics, Supply Chain and Retail Management Volume 2 Issue 1 Implementing Warehouse Management Systems in Logistics: A Case Study Natesan Andiyappillai*, Dr. T. Prakash** Senior Business Analyst*, Professor** Department of IT*, Department of Mechanical Engineering** NFI Industries, 1005 Laurel Oak Rd, Voorhees, NJ, 08043, USA*
This WMS implementation case study highlights the potential for comprehensive software to enhance virtually any warehouse operation. Achieving this requires a thorough analysis of every process within your warehouse and careful consideration of how advanced technology can drive improvements. This is especially beneficial if you decide to turn ...
The aim of this paper is to study the problem areas in GI and provide solutions to increase the performance of warehousing operations. First, a conceptual framework has been developed to improve the effectiveness of warehousing operations. Second, a case study has been conducted with the help of the model to minimize the through‐put time in ...
How one of the world's largest HVAC (Heating, Ventilation, and Air Conditioning) manufacturers adopted Hopstack's Digital Warehouse platform leading to 62% increase in outbound visibility and 25% reduction in pickup delay. Read Case Study. Here's a small glimpse of our latest case studies of Warehouse, Inventory & Order Management Solutions.
2 | Warehousing and Logistics Case Study Warehouse and Distribution Practices Among States During COVID-19 In the 21st century, public organizations have increasingly shifted to an on-demand just-in-time model of procurement and supply chain management.This model has been useful for shrinking bud-
Case Study Overview. In this case study, Company X, a leading logistics provider, embarked on a cloud transformation journey to modernize its warehouse management operations. The company ...
Warehouse Management Statistics. Global ecommerce has grown rapidly in recent years, and is expected to top $29 trillion by 2023—accelerating a need for more warehouse space to match growing consumer demands. Ecommerce growth is expected to increase demands for U.S. warehouse space by 1 billion square feet by 2025. It's not surprising that one survey, by trade publication Logistics ...
Existing research shows that understanding warehouse design and management principles can play a pivotal role in improving the efficiency of operations; reducing employee fatigue and turnover; and improving customer service levels. ... Their results, based on a multi-case study, support the proposition that maverick picking is a major ...
This case study uses the Global Bike Inc. (G.B.I.) data set, which was created exclusively for SAP UA global curricula. Warehouse Management (WM) Case Study IV . This case study explains the integrated warehouse management process of the physical inventory. A storage bin is checked by means of a continuous physical inventory.
this case study, it is not necessary to have finished the WM exercises. However, it is recommended. NOTES This case study uses the Global Bike Inc. (G.B.I.) data set, which has exclusively been created for SAP UA . Warehouse Management (WM) Case Study II . This case study explains an integrated warehousemanagement process which is
this case study, it is not necessary to have finished the WM exercises. However, it is recommended. NOTES This case study uses the Global Bike Inc. (G.B.I.) data set, which has exclusively been created for SAP UA . Warehouse Management (WM) Case Study III . This case study explains an integrated warehouse management process which is
Case Study | Warehouse Management . Case study about the Warehouse Management at Fr. Meyer's Sohn Initial Situation. Late 2019 one of the world's largest paper producer approached FMS to set up a warehousing solution in Los Angeles | USA for large tissue paper rolls being imported from the Far East. One of the key customer requirements was ...
Warehouse Management will put the goods into stock. In conclusion, you will check if the goods were sorted into the correct storage bins. Because this case study focuses on Warehouse Management detailed instructions of how to receive the invoice and how to pay the vendor are not included.
Warehouse management ensures that stock matches customer demand. Warehouse operations take into account the supply chain and work towards being cost-effective and efficient. To understand effective warehouse operations, you must first be clear on the warehouse operations process and how it plays into the larger warehouse operations management.
After researching many different mixed case palletizing solutions, I would list the main benefits of ACPaQ over alternative technologies as follows: Best in class flexibility - the ability to get any case from and to any station gives unrivalled flexibility. The ability to add goods-to-person picking technology is simple and easily integrated.
Part of the challenge may be that these organizations fail to fully consider the hidden costs of maintaining the status quo. From falling behind competitors to rising costs to unpredictable service levels, carefully considering the costs of inaction should always be considered as part of the business case for warehouse automation.
This case study illustrates how Alex strategically employs long-term call options to both realize profits and maintain exposure to NVIDIA stock. By adjusting his holdings through these options, he secures gains while keeping potential for future growth, showcasing effective risk management and investment foresight.
As part of its consulting services, Cloud 9 Infosystems offers a two-week engagement to integrate Office 365, Microsoft Entra ID, Azure Rights Management, and Azure Monitor Log Analytics in clients' environments. Continue reading here **Explore all case studies or submit your own**
Discover new extension capabilities for TimescaleDB, pgvector, PostGIS, and more, alongside a case study demonstrating the substantial performance enhancements and cost efficiency of migrating to Flexible Server. These updates are designed to improve database management and security for better operational resilience and efficiency.
A Case Study of Prioritizing Real Integration in School Mergers: Arts and Letters 305 United Introduction and History. As noted above, school mergers in the New York City public school system often solve for the operational, enrollment, and financial needs of each school.