

Guide: A3 Problem Solving
Author: Daniel Croft
Daniel Croft is an experienced continuous improvement manager with a Lean Six Sigma Black Belt and a Bachelor's degree in Business Management. With more than ten years of experience applying his skills across various industries, Daniel specializes in optimizing processes and improving efficiency. His approach combines practical experience with a deep understanding of business fundamentals to drive meaningful change.
Problem-solving is one of the key tools a successful business needs to structure improvements and one I have been using to solve problems in a structured way in my career at a range of businesses over the years. When there is a problem in business that is leading to increased costs, waste , quality issues, etc., it is necessary to address these problems. A3 structured problem solving is a Lean Six Sigma methodology that has been designed and developed to support continuous improvement and solve complex business problems in a logical and structured process.
The guide will give you a full understanding of what A3 Problem solving is and a breakdown of all the steps of how to apply it within your business with an example of where I have made improvements with it previously.
Importance of A3 in Lean Management
The A3 problem-solving method is a key tool in Lean Six Sigma and continuous improvement in business, and in my experience, it is often the standard approach all improvement activities must follow and is particularly popular in the automotive industry. This is because of the following:
Focus on Root Causes : Rather than applying a quick fix to a problem or jumping to conclusions and solutionizing, A3 requires gaining a deep understanding of the root causes of the problem. By addressing these root causes, the chances of recurrence is reduced.
Standardization : With a consistent format, the A3 process ensures that problems are approached in a standardized way, regardless of the team or department. This standardization creates a common language and understanding across the organization and ensures all problems are addressed to the same standard and approach.
Team Involvement : An A3 isn’t an individual process. It requires a cross-functional team to work together on problem-solving, ensuring that a range of perspectives and expertise is considered. This collective approach builds a stronger understanding of the problem and ensures that solutions are well-rounded and robust.
Visual Storytelling : The A3 report serves as a visual storyboard, making it easier for stakeholders at all levels to understand the problem, the analysis, and the countermeasures. This visualization enhances communication and drives alignment.
The 6 Steps of A3 Problem Solving (With Real Example)
The A3 problem-solving process can initially seem difficult if you have never done one before and particularly if you have never been a team member in one. To help you with this we will break down the 6 steps into manageable activities, followed by a real-life example to help you apply this method within your business.
As a side note, the A3 problem-solving process was actually one of the first Lean Six Sigma tools I learned to use three weeks into my continuous improvement career after being thrown into the deep end due to resource availability, so I can understand how difficult it can be to understand.
Step 1: Describe the problem
Problem description.
The problem description is an important first step in the process as it ensures a common understanding with the team of what the issue is that needs to be addressed. This can be done by using a technique called the 5W1H Is/Is Not method to help gain a clear understanding of the problem.
To understand the 5W1H Is/Is Not the Process, check out our guide for details of that technique. However, in short, it’s about asking key questions about the problem, for example, “What IS the problem?” and “What IS NOT the problem?”
Let’s say you have been asked to look into a problem where “Machine downtime on the automotive assembly line has increased by 30% over the past three months, leading to production delays and increased costs.”
An example of a 5W1H Is/Is Not on this may result in the following output:
5W1H | Is | Is Not |
---|---|---|
Who | Affects assembly line workers and leads | Affecting administrative staff |
What | Increased machine downtime by 30% | This affects all machinery on the floor |
When | Over the past 3 months | An issue that has been consistent over the years |
Where | Automotive assembly line No.3 | Present in assembly lines No.1 and No.2 |
Why | Lack of preventive maintenance and outdated components | Due to manual errors by operators |
How | Through interruptions in the assembly process | Through supply chain or external factors |
Based on this we can create a clear problem description as the focus of the project that give the team a clear and common understanding of the issue looking to be resolved in the next steps of the process. The problem description could then be written as:
“Over the past three months, machine downtime on Automotive Assembly Line No.3 has increased by 30%. This has predominantly affected the assembly line workers and leads, leading to production delays and higher labour costs. “
Current Condition
Next is demonstrating the current condition and demonstrating the impact on the business. This can often be done with data and charts to back up the problem that might show trends or changes in outputs.
This might look something like the below and demonstrate a good baseline for confirming the improvement at the end of the A3

Containment Actions
Next is containment actions. Since you have identified a problem, there is likely an impact on the business or the customer. As a team, you should consider what can be done to limit or eliminate this problem in the short term. Remember this is just a containment action and should not be seen as a long-term fix.
In our situation we decided to “Implement temporary overtime shifts to meet production goals, leading to an increase in labor costs.”
At this stage, the A3 should look similar to the one below; you can use charts and graphics to represent the current state as well if they fit within the limit area. Remember, we must include the content of the A3 within the 1-page A3 Document.

Step 2: Set the A3 Goals
The next step of the A3 is to, as a team, set the goal for the project. As we have a clear understanding of the current condition of the problem, we can use that as our baseline for improvement and set a realistic target for improvement.
A suggested method for setting the Target condition would be to use the SMART Target method.
If you are not familiar with SMART Targets , read our guide; it will cover the topic in much more detail. In short, a SMART target creates a goal statement that is specific, measurable, achievable, relevant and time-bound.
By doing this you make it very clear what the goal of the project is, how it will be measured, it is something that can be achieved, relevant to the needs of the business and has a deadline for when results need to be seen.
For our A3 we decided that the goal would be “Our goal is to achieve at least a 20% reduction in machine downtime on Automotive Assembly Line No.3, lowering it from 90 minutes to no more than 72 minutes per day per machine, within the next 60 days. This reduction is crucial for increasing productivity and reducing labour costs, aligning with our overall business objectives.”
I also recommend using charts in this section to visualize the benefit or improvement to ensure you have stakeholder and sponsor support. Visuals are much easier and faster for people to understand.

At this point, your A3 might look something like the one below, with the first 1/4 or section complete. The next step is to move on to the root cause analysis to get to the root of the problem and ensure the improvement does not focus on addressing the symptoms of the problem.

Step 3: Root Cause Analysis
Root cause analysis is the next step in the process, often referred to as gap analysis, as this step focuses on how to get to the goal condition from the current condition.
Tip: If at this point you find the team going off-topic and focusing on other issues, Ask the question, “Is this preventing us from hitting our goal statement?” I have found this very useful for keeping on track in my time as an A3 facilitator.
For root cause analysis, a couple of key tools are usually used: a fishbone diagram and a five-why Analysis . Again, we won’t go into the full details of these tools within this guide, as they have been covered in extensive detail in their own guides.
But the aim at this point is as a team, to brainstorm what is preventing us from achieving our target condition. This is done by allowing all members of the team to input the reasons they think it is not being achieved. These inputs are often written on sticky notes and placed on the fishbone diagram. Following this, you may have results similar to the ones below. Note: it is important that the inputs are specific so they can be understood. e.g. “Calibration” alone is not specific to how it’s causing the problem; specify it with “Calibration: Inaccurate measurements affecting machine settings.”

After the fishbone diagram has been populated and the team has exhausted all ideas, the team should then vote on the most likely cause to explore with a 5 Whys analysis. This is done because, due to resource limitations, it is unlikely all of the suggestions can be explored and actioned.
In this situation the team decided the “lack of preventative machines: machines not being serviced regularly” was the cause of increased downtime. This was explored with the 5 Whys to get to the root cause of why Assembly Line 3 did not have preventative maintenance implemented.
The result of this root cause analysis can be seen below, and you may end up with more ideas on the fishbone, as generally there are a lot of ideas generated by a diverse team during brainstorming.

Step 4: Solutions and Corrective Actions
Now that we understand what the root cause of the problem is, we need to address it with solutions and corrective actions. Again, as a team, consider the root cause of the problem and discuss what actions need to be taken by the team, who will do them, and when they will be done. The result should be an action plan, for example, like the one below:

This action plan needs to be carried out and implemented.
The result of this section will likely just be an action list and look like the below section.

Step 5: Validate Solution and Standardize
Within step 5 it is time to collect data to validate and confirm the actions that have been implemented resulting in solving the problem and meeting the target state of the problem. This is done by continuing to collect data that demonstrates the problem in the baseline to see if the problem is being reduced.
For example, below, the project team continued to collect Assembly Line 3 downtime data on a weekly basis. Initially, there was a steady reduction, likely due to the focus of the project on the problem, which had some impact. However, once the majority of the action was implemented, a huge drop in product downtime was seen, exceeding the target. This showed the actions have been successful

If, in the validation stage, you find that the improvement required is not being made, you should go back to step 3 and reconsider the root cause analysis with the team, pick another area to focus on, and create an action plan for that following the same steps.

Step 6: Preventive Actions and Lessons Learned
In step 6 after the confirmation of project success you should look at preventive actions and lessons learned to be shared from this project:
- Preventive Action: The new preventive maintenance schedule will be standardized across all assembly lines. This will prevent other lines having similar issues and make further improvements
- Lessons Learned: A formal review will be conducted to document the process, including challenges faced and how they were overcome, which will then be archived for future reference.
In our project, this looked like the one below and will be used as a reference point in the future for similar issues.

And that is the successful completion of a structured A3 problem-solving technique.
The complete A3 looks like the below image. Yours may slightly differ as the problem and information vary between projects.

Downloadable A3 Reporting Template
To support you with your A3 problem solving, you can download our free A3 problem solving report from the template section of the website.

Problem-solving is important in businesses, specifically when faced with increased costs or quality issues. A3 Structured Problem Solving, rooted in Lean Six Sigma, addresses complex business challenges systematically.
Originally from Toyota’s lean methodology, A3, named after the 11″x17″ paper size, visually maps problem-solving processes. This method ensures concise communication and focuses on crucial details, as illustrated by the provided example.
Emphasized in Lean Management, A3 stresses understanding root causes, standardization across teams, team collaboration, and visual representation for clarity. This tool is not only a guide to understanding the issue but is a standardized format ensuring robust solutions. Particularly for novices, breaking down its six steps, from problem description to setting A3 goals and root cause analysis, provides clarity. Visual aids further enhance comprehension and alignment across stakeholders.
- Sobek II, D.K. and Jimmerson, C., 2004. A3 reports: tool for process improvement. In IIE Annual Conference. Proceedings (p. 1). Institute of Industrial and Systems Engineers (IISE).
- Matthews, D.D., 2018. The A3 workbook: unlock your problem-solving mind . CRC Press.
Q: What is A3 problem solving?
A: A3 problem solving is a structured approach used to tackle complex problems and find effective solutions. It gets its name from the A3-sized paper that is typically used to document the problem-solving process.
Q: What are the key benefits of using A3 problem solving?
A: A3 problem solving provides several benefits, including improved communication, enhanced teamwork, better problem understanding, increased problem-solving effectiveness, and the development of a culture of continuous improvement.
Q: How does A3 problem solving differ from other problem-solving methods?
A: A3 problem solving emphasizes a systematic and structured approach, focusing on problem understanding, root cause analysis, and the development and implementation of countermeasures. It promotes a holistic view of the problem and encourages collaboration and learning throughout the process.
Q: What are the main steps in the A3 problem-solving process?
A: The A3 problem-solving process typically involves the following steps: problem identification and description, current condition analysis, goal setting, root cause analysis, countermeasure development, implementation planning, action plan execution, and follow-up and evaluation.
Q: What is the purpose of the problem identification and description step?
A: The problem identification and description step is crucial for clarifying the problem, its impact, and the desired outcome. It helps establish a common understanding among the team members and ensures everyone is working towards the same goal.

Daniel Croft
Hi im Daniel continuous improvement manager with a Black Belt in Lean Six Sigma and over 10 years of real-world experience across a range sectors, I have a passion for optimizing processes and creating a culture of efficiency. I wanted to create Learn Lean Siigma to be a platform dedicated to Lean Six Sigma and process improvement insights and provide all the guides, tools, techniques and templates I looked for in one place as someone new to the world of Lean Six Sigma and Continuous improvement.

Free Lean Six Sigma Templates
Improve your Lean Six Sigma projects with our free templates. They're designed to make implementation and management easier, helping you achieve better results.
Was this helpful?

A3 Thinking in Action: A Step-by-Step Guide to Effective Problem Solving

Leansimplified
In the dynamic landscape of business and continuous improvement, A3 thinking has emerged as a powerful tool, providing a structured and systematic approach to problem-solving. Originating from Lean manufacturing principles, the A3 methodology has transcended its manufacturing roots to become a widely adopted framework in various industries. For the best A3 Thinking templates , visit lean simplified.
Step 1: Define the Problem Clearly
The first step in A3 problem-solving is to clearly define the problem at hand. This involves understanding the current situation, identifying the gap between the current state and the desired state, and framing the problem in a concise and specific manner. Clarity in problem definition sets the foundation for effective problem-solving efforts.
Step 2: Grasp the Current Situation
Once the problem is defined, the next step is to thoroughly grasp the current situation. This involves collecting relevant data, conducting root cause analysis, and creating a visual representation of the current state. Visual tools such as process maps, fishbone diagrams, or Pareto charts can be employed to enhance understanding and communication.
Step 3: Set a Target and Goal
With a clear understanding of the current situation, it’s time to set a target and goal for improvement. Define what success looks like and establish measurable objectives that will guide the problem-solving process. This step provides a clear direction and purpose for the team, aligning efforts with organizational objectives.
Step 4: Analyze Root Causes
Digging deeper into the problem, the fourth step involves identifying and analyzing the root causes. A variety of problem-solving tools such as the “5 Whys” or cause-and-effect diagrams can be used to systematically explore the underlying issues contributing to the problem. This critical analysis helps in addressing the core issues rather than just treating symptoms.
Step 5: Develop Countermeasures
Armed with a comprehensive understanding of the problem and its root causes, it’s time to develop countermeasures. These are specific actions and strategies designed to eliminate or mitigate the identified root causes. The focus is on creating effective solutions that align with the set target and goals.
Step 6: Implement Countermeasures
Implementation is a pivotal phase in A3 thinking. It involves executing the identified countermeasures and monitoring their impact on the problem. Effective communication and collaboration within the team are crucial during this phase to ensure a smooth and coordinated implementation process.
Step 7: Evaluate Results
After implementation, evaluate the results against the established goals and targets. This step involves measuring the effectiveness of the countermeasures and assessing whether the problem has been successfully addressed. Data-driven evaluation provides valuable insights for ongoing improvement efforts.
Step 8: Standardize Successful Processes
To sustain improvements, the final step is to standardize successful processes. Document the new standard procedures, update training materials, and ensure that the changes become an integral part of the organization’s practices. Standardization fosters consistency and prevents the recurrence of similar problems.
Benefits of A3 Problem-Solving
The A3 problem-solving process offers several benefits to organizations:
- Structured Approach: A3 thinking provides a structured and systematic approach to problem-solving, guiding teams through a logical sequence of steps.
- Visual Communication: The use of visual tools in A3 reports enhances communication and understanding, making complex issues more accessible to team members and stakeholders.
- Data-Driven Decision-Making: A3 thinking encourages data collection and analysis, promoting informed and data-driven decision-making.
- Continuous Improvement: By addressing root causes and implementing effective countermeasures, A3 problem-solving contributes to a culture of continuous improvement within organizations.
Conclusion: Empowering Organizations Through A3 Thinking
A3 thinking, when effectively applied, empowers organizations to tackle challenges with clarity, precision, and strategic intent. By following the step-by-step guide outlined above, organizations can harness the full potential of A3 problem-solving, fostering a culture of continuous improvement and resilience in the face of complex problems. As organizations navigate the ever-evolving landscape of business, A3 thinking stands as a reliable compass, guiding them toward effective solutions and sustainable success. Lean simplified also offers the best lean training online , visit their website to learn more.
Key Takeaways
- C larity in Problem Definition: A3 thinking begins with a clear and concise definition of the problem, setting the stage for effective problem-solving efforts.
- Thorough Understanding of the Current Situation: Grasping the current situation involves data collection, root cause analysis, and visual representation to enhance understanding and communication within the team.
- Setting Clear Targets and Goals: Establishing measurable objectives provides a clear direction for the problem-solving process, aligning efforts with organizational objectives.
- Root Cause Analysis: A3 thinking emphasizes the importance of identifying and analyzing root causes, going beyond surface-level issues to address the core factors contributing to the problem.
- Development and Implementation of Countermeasures: Effective solutions are developed based on the identified root causes, and a coordinated implementation plan is executed to address the problem.
- Results Evaluation: After implementation, the results are rigorously evaluated against set goals and targets, providing valuable insights for ongoing improvement efforts.
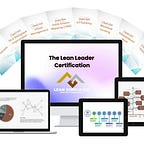
Written by Leansimplified
Text to speech
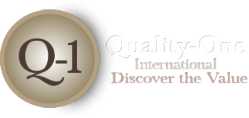
A3 Problem Solving
– The A3 Report –
⇓ Introduction to A3
⇓ What is A3
⇓ Why Implement A3
⇓ How to Implement A3
⇓ A3 Services
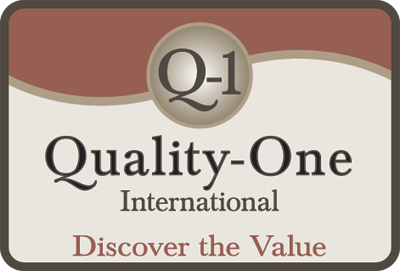
Introduction to A3 Problem Solving
In order for any business to be successful, they must strive to improve quality and efficiency as well as build a problem solving continuous improvement culture. The A3 Report is a very useful problem solving and continuous improvement tool. It was first used by Toyota and is quickly gaining popularity in industry today. Companies must start to view problems as opportunities for improvement. The A3 Report format allows the entire problem identification, clarification, analysis and resolution steps to be documented on one single sheet of paper.
What is A3 Problem Solving
The name “A3” is actually derived from a standard European paper size similar to 11” by 17”. The A3 Report is based upon the Plan, Do, Check, Act (PDCA) Method. The PDCA process is sometimes referred to as the Deming Wheel or Deming Circle. The A3 Report incorporates this basic premise to problem solving and continuous improvement.
Why Implement A3 Problem Solving
Some problem solving tools involve numerous pages of information, multiple charts and graphs and lengthy reports. The A3 Report format can be used to more effectively communicate all of the pertinent information with greater visual impact. While the A3 Report is an effective communication tool, it is actually much more valuable as a problem solving and critical thinking tool that can be used to drive continuous improvement. The A3 Report fosters a problem solving / continuous improvement mindset within the participating team members. It is an excellent tool for managers and supervisors to share problem solving techniques with their teams. With resources being limited, completion of a formal A3 Report may not be applicable to every problem. Its use should be determined based upon the size of the problem and its impact on the business or organization. The A3 Report and the A3 way of thinking are valuable tools for Lean initiatives and for integrating a problem solving culture throughout the organization.
How to Implement A3 Problem Solving
The A3 Report usually consists of multiple steps following a PDCA structure of Plan, Do, Check, Act. The number of steps can vary due to the different formats being used for the A3 Report. The exact number of steps used is not as important as the end result. The A3 Report can utilize various forms depending upon the organizations needs and preferences. The following paragraphs provide information regarding the basic steps and some tools used to complete the A3. One thing that all of the forms seem to have in common is that they follow the PDCA problem solving process. The basic steps and where they fall into the PDCA structure are listed below:
- Define the Problem:
The first step is to define the problem or identify the need for improvement:
- Define the ideal state, the operational standard or the desired condition
- Describe the current situation or status
- How is the current status different from the desired state or operational standard?
- What value will be realized by completion of the A3 exercise?
- Containment:
In some A3 formats, a section is included for immediate countermeasures or containment actions. The purpose of containment is to prevent further problems from occurring or prevent the current problem from causing negative effects to other processes, products or departments.
- Breakdown the Problem:
Next, the team should breakdown or further define the problem. Ask any relevant 5W (What, When, Where, Who, Why) and 2H (How, How many / How often) questions. There also may be more than one issue contributing to the problem or more detail required to properly address the problem. Prioritize the issues and identify the point of occurrence or escape point.
- Define goals:
The A3 team should set goals regarding the improvement desired as a result of the exercise. This could include a percentage of improvement in process throughput, reduction in number of defects per unit or processing time. The goals should be specific, measureable, realistic, achievable and timely. Many companies are adopting the SMART goal approach.
- Root Cause Analysis:
The team should perform a Root Cause Analysis (RCA) of the problem by using various quality tools. The tools could include, but are not limited to data analysis or completing a Cause and Effect or Ishikawa diagram followed by a 5 Why exercise. Whatever method selected, it is important to get past the symptoms of the problem and down to the root cause.
- Countermeasures:
Permanent countermeasures or corrective actions must then be determined to address the root cause. The countermeasures must be clearly defined, achievable by the person responsible and have a due date. Corrective actions that do not have an owner or due date are seldom achieved.
- Implementation:
A plan for implementation of the corrective actions should be developed. The plan should include the team members, resources and time required to complete each task. In some cases, support from outside resources or test facilities are required. Some countermeasures may require repair or replacement of tooling or other capital expenditures. Therefore, proper levels of management should be kept informed throughout the process to assure adequate resources are available for implementing any corrective actions.
- Monitoring and Validation:
The A3 team should next confirm the effectiveness of the countermeasures. This can be accomplished in many ways, including but not limited to additional quality checks, Statistical Process Control (SPC) data, process or product audits and customer feedback.
- Standardize and Improve:
During this phase of the A3, the team should take action to standardize the process changes or improvements. The team must update all standard work, work instructions and process control plans, etc. In addition, it is a good practice to perform a short Things Gone Right / Things Gone Wrong (TGR/TGW) exercise and document in the A3 report what went well during the process and what could use improvement. The management team should also promote continuous improvement of the A3 tool within the organization.
Common problems to avoid with the A3 Report:
- The background is not well developed
- The problem statement is not well defined or unclear
- The ideal state or target condition is actually an action item, not the desired result
- Analysis does not drill down to the root cause(s)
- Ineffective countermeasures that will not prevent the problem from re-occurring
- Validation and monitoring methods are not well documented or there is a lack of evidence of improvement
Always remember that the A3 process and report are about fostering critical thinking. Encourage A3 thinking within your organization. The A3 process should be focused on improvement through developing the skills of the people. A3 thinking promotes problem solving, communication and mentoring of the teams.
The A3 Report is an effective visual tool for driving improvement and promoting a problem solving way of thinking. The format can and does vary depending upon the company or organization. The format you select is not as important as the results of the exercise. As long as the form contains the basic steps for problem identification, root cause analysis, corrective action and monitoring improvement or performance, it will be a very effective tool. The A3 Report has its roots in the automotive industry but is branching out into many different applications and industries from manufacturing to healthcare.
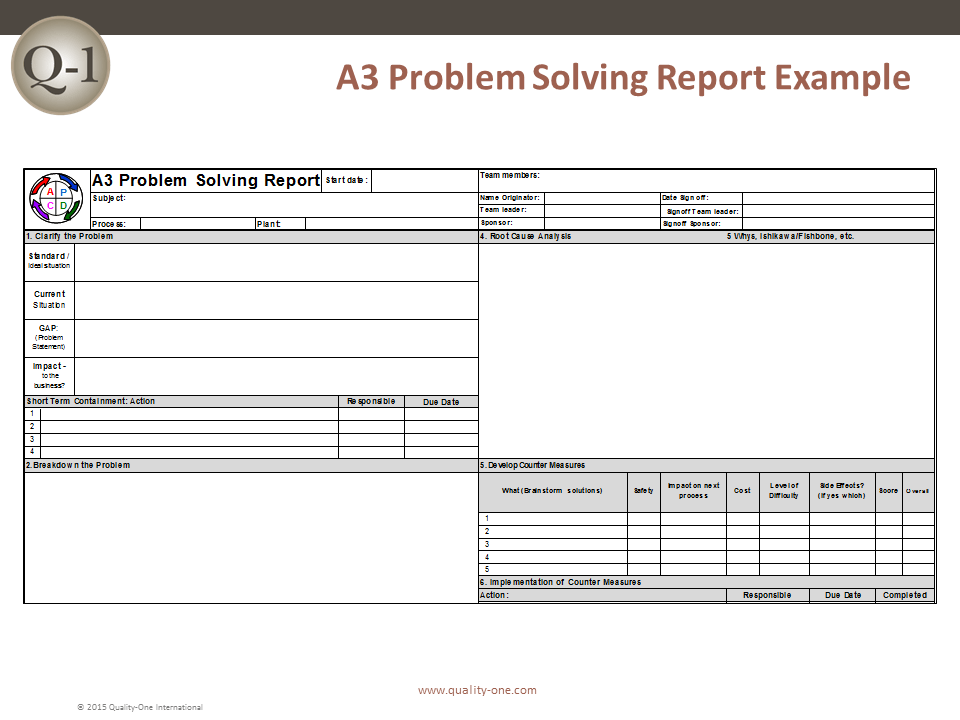
A3 Problem Solving Services
A3 Services from Quality-One include A3 Problem Solving Consulting, A3 Problem Solving Training and A3 Problem Solving Project Support, such as Facilitation and Auditing. Our experienced team of highly trained professionals will provide a customized approach for developing your people and processes based on your unique needs. Whether you need Consulting to assist in the design of your A3 process, Training to help understand and drive improvement through the A3 report, or hands-on Project Support for building and implementing your A3 process by utilizing our experienced Subject Matter Experts (SME) to work with your teams, Quality-One can help you promote A3 thinking in your organization.
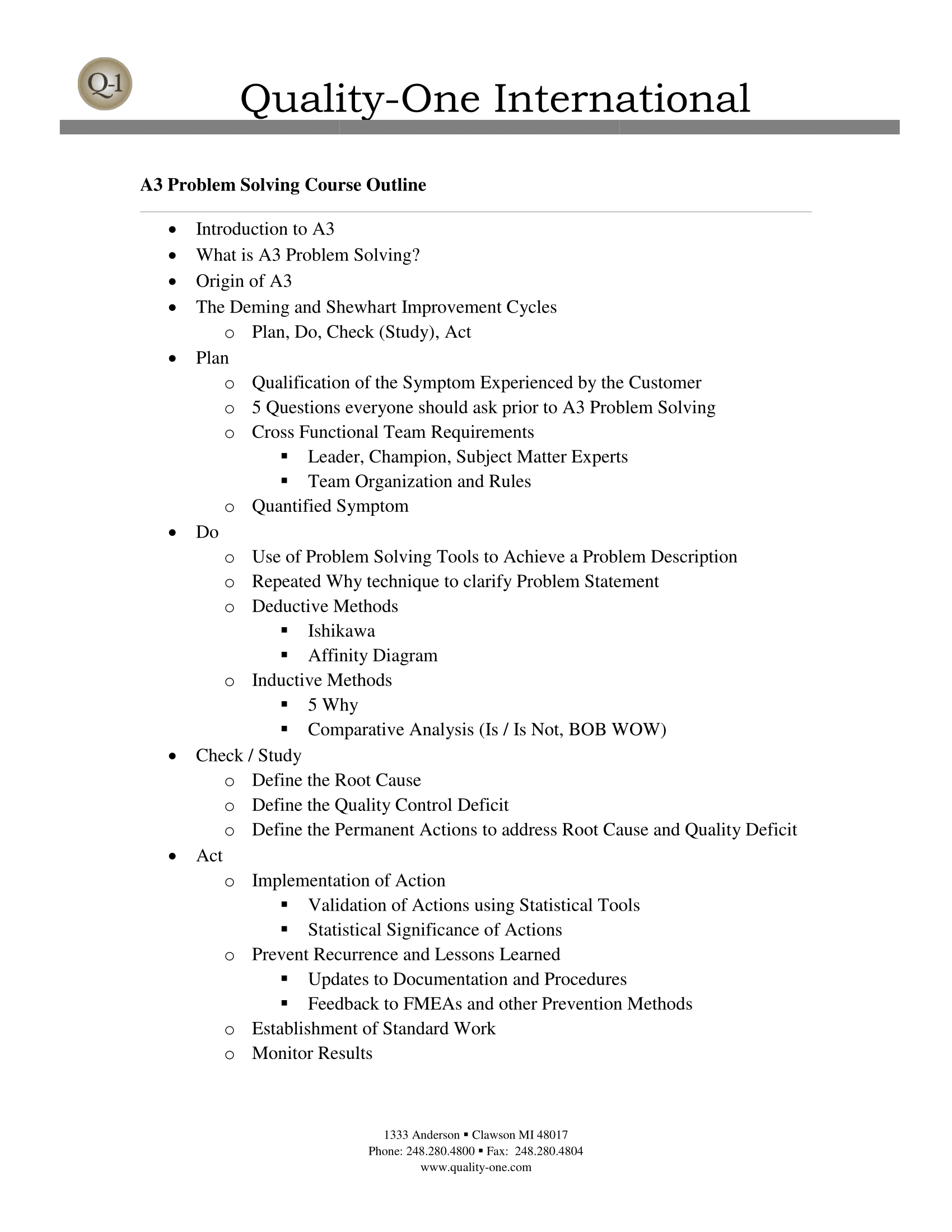
Learn More About A3 Problem Solving
Quality-One offers Quality and Reliability Support for Product and Process Development through Consulting, Training and Project Support. Quality-One provides Knowledge, Guidance and Direction in Quality and Reliability activities, tailored to your unique wants, needs and desires. Let us help you Discover the Value of A3 Consulting, A3 Training or A3 Project Support.
Contact Us | Discover the Value!
(248) 280-4800 | [email protected]
Remember Me

Continuous Improvement Toolkit
Effective Tools for Business and Life!
A3 Thinking: A Structured Approach to Problem Solving
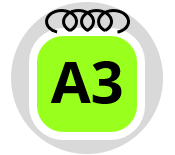
- 5 MINUTES READ
Also known as A3 Problem Solving.
Variants include 8D and CAPA.
A significant part of a leader’s role involves addressing problems as they arise. Various approaches and tools are available to facilitate problem-solving which is the driving force behind continuous improvement. These methods range from the advanced and more complex methodologies like Six Sigma to the simpler and more straightforward A3 thinking approach.
The power of the A3 approach lies in its systematic and structured approach to problem-solving. Although it appears to be a step-by-step process, A3 is built around the PDCA philosophy. It relies on the principle that it is much better to address the real root-cause rather than trying to find a solution. Hence, it’s important not to jump to the solution when solving a problem as it is likely to be less effective.
A3 thinking provides an effective way to bring together many of the problem-solving tools into one place. For example, techniques such as the 5 Whys and fishbone analysis can be used during the ‘Analysis’ stage to help identifying the root causes. Additionally, visual aids and graphs are highly recommended in the A3 report, as they are more effective than text in communicating ideas and providing concise project updates.
A3 thinking involves the practice of consolidating the problem, analysis, countermeasures, and action plan onto a single sheet of paper, commonly an A3-sized sheet. This brief document serves as a summary of the project at hand and is regarded as a valuable storytelling tool for project communication. Utilizing the A3 approach doesn’t require any specialized software or advanced computer skills. You may however use readily available A3 templates , or rely on basic tools such as paper, pencil and an eraser as you will need to erase and rewrite several times.

One of the characteristics of the A3 approach is that it does not get into specific details. Detailed documents are usually attached to the A3 report to prevent overwhelming the reader with an excess of information.
The A3 process is typically structured in multiple stages based on the PDCA model. The primary focus is on developing understanding of the current situation and defining the desired outcome before thinking about the solution. While the exact number of stages may vary depending on the preference of the company, what truly matters is adhering to a structured approach to problem-solving.
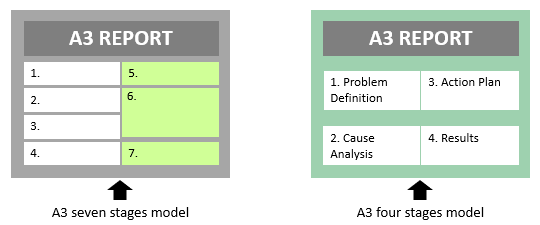
A3 Seven Stages Model
An A3 process is often managed by an individual who should own and maintain the A3 report. This individual takes the lead in steering the process, facilitating team involvement, and preparing the A3 report with team input. One of the most common models for A3 thinking is the seven stages model which is described in the following.
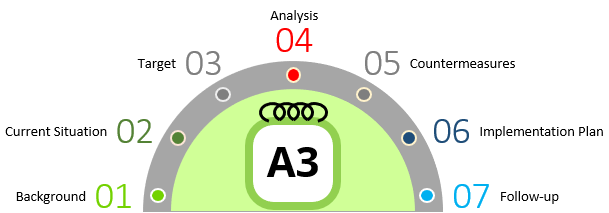
1. Background – The first step is to identify the business reason for choosing this problem or opportunity. In this stage, you need to identify the gap in performance and the extent of the problem.
2. Current situation – The purpose of this stage is to document the current state of the problem. You may need to refer to the process map or go to the Gemba to truly understand the current situation.
3. Target – The purpose of this stage is to define the desired future state. Clearly identify the expected benefits from solving the problem, the scope, and the key metrics that will help measure the success of the project.
4. Analysis – The objective of this stage is to conduct an in-depth analysis of the problem and understand why it’s happening. It might involve tools like the 5 Whys and cause-and-effect analysis, as well as advanced statistical methods.
5. Countermeasures – Countermeasures are the actions to be taken to eliminate root causes or reduce their effects. The team should brainstorm and evaluate possible countermeasures based on the analysis conducted earlier.
6. Implementation Plan – To achieve the target, develop a workable plan to implement the countermeasures. Gantt charts are great ways to manage implementation plans very simply and easily. Once the action plan is finalized, the team should begin working on the activities needed to implement the countermeasures.
7. Follow-up – The final stage involves evaluating the implementation of the plan and the results achieved. Follow-up actions are important to ensure the benefits extend beyond the project’s completion.

A3 thinking is considered to be the practical form of the PDCA model.
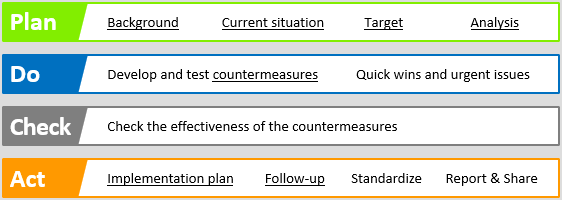
There are many online templates that can be used to manage your problem-solving efforts. One of the simplest and most straightforward ways is to use this A3 problem solving template .
Wrapping Up
A3 thinking represents a logical and structured approach for problem solving and continuous improvement. This approach can be used for most kinds of problems and in any part of the business. Originating from the Toyota Production System (TPS), it has been adopted by many Lean organizations around the world.
A3 thinking not only provides a systematic approach for problem-solving. The development of a continuous improvement culture is at the core of A3 thinking. It has become one of the most popular Lean tools today where people and teams work together to solve problems, share results and learn from each other.
Other Formats
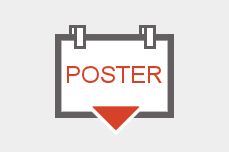
Do you want to use the slides in your training courses?

A3 Thinking Training Material – $18.85
Related Articles
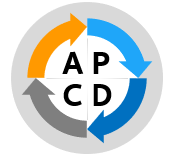
Project Charter
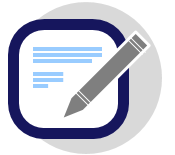
Gantt Chart

Related Templates
A3 Problem Solving
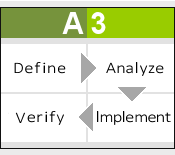
Written by:
CIToolkit Content Team
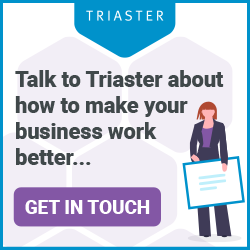
- Consultancy
- Online Courses
- Lean , Lean Culture , Lean Training , Lean Wiki , Tools
A Deep Dive into the A3 Problem-Solving Approach
- 11 mins to read
- June 20, 2023
- By Reagan Pannell
In today’s fast-paced and fiercely competitive business world, organisations must find ways to continuously adapt, evolve, and excel. Amidst the myriad methods and techniques for achieving improvements and driving continuous improvement , few have proven as profound and transformative as Toyota’s A3 problem-solving approach.
A significant driving force behind the company’s rise to global prominence, the A3 process fosters a culture where problems are embraced as opportunities for growth and learning. In this article, we’ll explore the origins and underlying principles of the A3 approach and uncover the secrets to its success in unlocking the power of improvements.
Understanding the A3 Approach
The A3 methodology is an integral part of the Toyota Production System (TPS), a set of principles and practices that have shaped the company’s approach to manufacturing, management, and continuous improvement over the years. Named after the A3 sheet of paper that was historically used to capture the plan, analysis, and follow-up on a single sheet of paper, typically an A3-sized sheet, the A3 process represents a simple, yet powerful, tool for addressing complex challenges and discovering lasting solutions.
At its core, the A3 approach is rooted in three key elements:
Thorough problem analysis : The foundation of the A3 process lies in digging deep to diagnose the true nature and root cause of an issue, rather than jumping to hastily devised fixes that merely address symptoms.
Structured documentation: The A3 report serves as both a communication tool and an iterative planning device, with each section building on the previous ones to guide problem solvers through a comprehensive analysis, solution development, and execution process. It’s the foundation of good continuous improvement.
Cyclical learning and improvement: Leadership and employees alike are encouraged to commit to hypothesis-driven inquiry, observation, experimentation, and reflection, leading to a culture that actively seeks and leverages opportunities for growth by solving problems.
How to Implement the A3 Process in Your Organisation
The Lean Thinking A3 approach can be distilled into seven essential steps:
1. Identify the problem:
Clearly articulate and define the issue at hand, avoiding the temptation to jump to solutions or assume important facts to be self-evident..
When identifying the problem, it is important to ensure that all relevant stakeholders in the organisation are consulted. This helps to ensure that the issue is accurately described and understood from multiple perspectives. A thorough problem analysis should also include conducting research into possible causes or root issues, and clearly documenting any observed symptoms of the problem. Additionally, it is essential to identify any major risks associated with not finding a solution and recognise any constraints (both external and internal) that may exist which could limit potential solutions. Lastly, it is important to consider any potential opportunities which may arise from addressing the issue that may have been overlooked at first glance. This is the problem statement part which is a critical component that identifies the difference between the current condition and the target condition.
At this stage, we are not looking at how to solve problems being faced or at the potential solution to solving problems. It’s about developing a good understanding of how the actual results differ from the expected results and providing an in-depth systematic approach to process improvement and developing problem-solving skills.
2. Establish the context and background:
Provide a high-level overview of the problem, describing the stakeholders involved, relevant data, and the broader organisational context in which the challenge has arisen..
It is important to ensure that all stakeholders are properly considered when identifying any potential solutions as their perspectives can play a vital role in determining an effective solution. All related data should be thoroughly analysed to understand the full scope of potential solutions. This includes resources, costs, timelines, and any legal or regulatory issues that may need to be considered. Additionally, it is important to consider how well-proposed solutions fit within existing organisational policies and procedures as this could impact implementation success. Finally, understanding how proposed solutions would interact with other initiatives or processes currently taking place in the organisation can help inform decisions about whether or not they are viable options. It may include conducting some value stream mapping to dig deeper into the current state.
It is important to fully explore any underlying factors that may be contributing to the issue at hand and ensure in-depth problem analysis. This includes looking deeper into existing systems, structures, and processes related to the problem in order to identify potential areas of improvement or optimisation. Additionally, it is essential to consider any relevant industry trends or external influences that could impact how the problem manifests within the organisation.
When analysing a problem, collecting data from various sources is important to get a more comprehensive understanding of how a particular issue can be addressed. This includes mapping the current process using the VSM, SIPOC , Process Mapping or Flowcharting techniques. Additionally, interviews and surveys can be conducted with stakeholders to gain insights into how they perceive the issue and their perspectives on potential solutions. Lastly, it is important to observe any real-world activities related to the problem to uncover key areas where time, effort, resources, money etc is being wasted. This is the time improvement that may not have been identified otherwise.
GB MASTERCLASS COURSE
Get access to our free gb mastercourse classes, free course previews, fundamentals of lean.
Ready to start your journey into the world of Lean with this free course?
FREE COURSE
Lean Thinking
A Lean focused continious improvement certification course
LSS Yellow Belt
Propel your career forward, tackle complex problems and drive change
LEAN SIX SIGMA GREEN BELT
Get 3-days free access to our green belt course, accelerate your career, 3. set a goal:, now that you have identified the problem and outlined the relevant context, it is time to set a project goal or outcome..
This involves clearly articulating the desired state of affairs and any key deliverables of the proposed solution. Whether it is reducing operational costs, increasing efficiency, improving customer experience, or something else entirely – defining specific objectives with measurable metrics can help ensure that project teams stay focused and remain aligned on their ultimate destination.
At this stage, it is also important to consider how long it will take to reach the desired outcome. Establishing an implementation timeline will help safeguard progress and provide a framework for tracking results along the way. Setting milestones for achieving particular goals at certain points in time can be especially helpful in keeping teams accountable throughout the process. Additionally, having a plan for evaluating success after reaching the end target will allow stakeholders to gain further insights into how effective their approach has been in addressing underlying problems, as well as how well-proposed solutions have fared once implemented.
4. Investigate root causes:
Use a variety of techniques (e.g., the 5 whys, fishbone diagrams, pareto charts) to probe the problem’s underlying causes and avoid settling on proximate reasons..
The process of identifying root causes is essential when using data-driven tools. We always want to find the simplest root cause approach.
One of the most widely used methods for root cause analysis is the ‘5 Whys’ technique. This method involves asking a series of ‘why’ questions to determine the underlying cause of a particular symptom or issue. The goal is to keep asking “Why?” until you reach an answer that can provide insight into how to address the problem and prevent it from occurring in the future.
Another commonly used tool for root cause analysis is the fishbone diagram (also known as Ishikawa diagrams). This approach involves visualising all potential causes which could be causing a symptom or issue in a logical format, allowing users to identify patterns and uncover links between root causes and their respective effects. This technique can be helpful in identifying and focusing on key areas for improvement, as well as helping to identify interdependencies between components within an organisation’s systems.
Finally, Pareto Charts are useful for analysing data collected from surveys, interviews, observations, etc., concerning the severity or frequency of occurrence. This type of chart helps users quickly identify which factors are contributing most significantly towards an issue, allowing them to focus resources towards addressing those areas first and foremost. Additionally, Pareto charts can also be used to prioritise different solutions based on their estimated effectiveness in addressing an issue.
In conclusion, understanding the root cause of an issue through rigorous techniques such as 5 Whys, fishbone diagrams, and Pareto charts provides invaluable insight into how best to address it effectively while preventing it from reoccurring in the future. By leveraging these tools along with other data-led approaches such as process mapping and flowcharting, organisations can ensure that any proposed solutions are well-informed by both qualitative and quantitative data sources as well as ensure they are building consensus across the entire organisation.
5. Countermeasures:
Identify the right countermeasures (corrective actions) to implement that will directly impact the root causes identified..
Brainstorming is a useful tool for identifying potential improvements. It involves coming up with ideas and solutions in an open and collaborative manner, without judgement or criticism. By allowing team members to share their thoughts freely, brainstorming can help uncover innovative solutions that may have otherwise gone unnoticed. Additionally, looking at how waste reduction, flow and pull can be used to improve processes can also provide valuable insights into where improvement opportunities lie.
Brainstorm potential solutions that directly target the root causes and create detailed action plans for implementation, complete with assigned roles, responsibilities, and timelines.
Once the countermeasures are identified, it is important to design an implementation plan and assign roles & responsibilities. This will help ensure that all stakeholders understand their part in the implementation and can work together to achieve the desired outcome. Additionally, it is important to track progress along the way – setting measurable milestones that can be tracked against goals established during the initial problem-solving phase will help keep teams accountable and allow for course corrections if needed.
By utilising A3 Problem Solving Tools such as a template, organisations can easily document and share their analyses with relevant stakeholders throughout each stage of the project. Having detailed record-keeping like this also helps teams stay on target over time while providing insights into how proposed solutions may need to be re-evaluated down the line. This implementation plan provides the entire organisation with a clear project status on a one-page report.
6. Evaluate the results:
Measure the impact of your countermeasures against the problem, using well-defined success criteria, key performance indicators, or other relevant metrics..
Once the countermeasures have been implemented, it is essential to measure and evaluate their success. This can be done by tracking performance against the initial objectives established during the goal phase, as well as establishing key performance indicators to gauge how well the proposed solutions have fared.
Additionally, stakeholders should also consider conducting a post-implementation evaluation in order to assess how successful their approach has been in addressing underlying issues and determining what lessons can be learned from the experience. This will enable teams to identify strengths and weaknesses within their existing processes and make any necessary adjustments going forward. By understanding the outcomes of their improvements, organisations are able to gain valuable insights into how well they’ve succeeded in achieving their goals and ensure continued success moving forward.
Once the countermeasures have been implemented and their success measured, it is important to compare the results against the initial objective. This can be done in a variety of ways, including graphical analysis such as charts, process maps or flow diagrams. Graphical analysis helps to visualise the differences between results achieved before and after the implementation of new measures in a meaningful way. It also provides an increased level of clarity when assessing whether the desired outcomes have been achieved or not.
Process maps can be useful in understanding how changes made during the improvement phase have impacted processes within an organisation. By mapping out existing processes and then comparing them against those following implementation of countermeasures, teams can easily pinpoint where improvements were made and analyse how they led to improved performance overall.
Charts, on the other hand, enable users to quickly identify trends that may have emerged from data collected during the project. For example, if performance metrics are tracked before and after countermeasures are implemented, users can use charts and graphs to more clearly observe any patterns that may indicate an improvement or regression in performance over time – providing further insights into which areas need further attention or adjustment moving forward.
Finally, dashboard views provide an effective means of displaying results at a glance while highlighting any anomalies that might warrant further investigation. Dashboards allow stakeholders to gain access to important information quickly and easily while also helping them keep track of progress towards goals set out during initial problem-solving phases. Additionally, because dashboards support data visualisation capabilities they offer a highly interactive user experience which can help teams understand underlying trends with greater clarity and precision.
7. Standardise and share:
If a countermeasure proves successful, integrate it into the organisation’s standard operating procedures and share it with other teams as a best practice..
Once the countermeasures have been successfully implemented and measured against the initial objectives, these changes need to be integrated into the organisation’s standard operating procedures (SOPs) and shared with other teams as best practices. This will ensure that any improvements made during the problem-solving phase are consistently applied across all teams within the organisation.
In order to ensure that these improvements become part of the organisation’s long-term strategy, process maps should be updated to reflect the new improved way of working. Process maps provide a visual representation of how workflows are structured within an organisation, and by updating them in line with newly-implemented countermeasures, organisations can ensure that their processes continue to remain up-to-date and efficient moving forward. It may also be necessary to build a follow-up plan if not all tasks are fully completed as well as develop a Lean-focused PDCA cycle to ensure long-term effective collaboration on the solutions that were implemented.
Process documentation should also be updated in order to keep track of changes made during problem-solving. By documenting not just the solutions that were proposed but also why they were proposed, teams can gain valuable insights into their decision-making process which they can leverage for similar future problems.
Furthermore, it is important to update key performance indicators (KPIs) to accurately reflect any progress made during problem-solving. By tracking performance against objectives established before and after countermeasures were implemented, organisations will be able to identify any areas that may still need improvement or require further adjustment going forward. Additionally, tracking KPIs over time will help teams understand whether or not their current strategies are leading them towards meeting their goals in a timely manner or if additional measures may need to be taken in order to achieve desired results more quickly.
Finally, organisations should share successful solutions with other teams in order to promote collaboration and knowledge sharing amongst stakeholders throughout different parts of the business. This will allow for ideas generated through one team’s problem-solving efforts to benefit multiple departments – helping foster creativity and innovation while ensuring that everyone is on board with necessary changes being made throughout the organisation. The last step is key to Toyota’s PDCA management system designed for the entire organisation.
By breaking down the problem-solving process into these seven discrete stages, the A3 method offers practitioners a comprehensive, end-to-end framework for tackling complex challenges and driving improvements in any organisation.
- Lean Consultancy
- Corporate Training
Training the team on A3
To get A3 started, everyone in the entire organisation needs to learn how to use this single-sheet or single-page document. This means training people across all parts of the company so that everyone knows how to use the A3 Problem Solving Tool and A3 template. Training will help make sure that everyone follows a structured approach when using an A3 problem solving method, which is derived from Lean management and Six Sigma methodologies.
Getting the organisation fully onboard with A3 Problem Solving is not an easy task and will require a dedicated effort to ensure its successful implementation. To this end, it is important to start with specific areas of the business – whether it be operations, finance or marketing – by setting up targeted training sessions for both operational teams and senior managers. This will help everyone understand how and why A3 is used, as well as the potential benefits it can bring to their business.
Once everyone has mastered the basics of working with an A3 template, companies should look to regularly review and evaluate its effectiveness. This could include setting up quarterly reviews or running workshops where teams discuss successes and areas for improvement when using the A3 tool. Doing this will ensure that any issues are identified early on, allowing the team to quickly adjust accordingly.
At Leanscape, we understand that transitioning to A3 Problem Solving can be a daunting task. With our team of specialists, we can provide your teams with the necessary training and coaching to ensure that they are able to adapt quickly and efficiently. Our comprehensive approach to A3 will equip your team with the knowledge and skills needed to successfully use this powerful tool for improving performance in all areas of your business.
We are committed to helping you develop a culture of continuous improvement within your organisation by teaching best practices and providing guidance through every step of the problem-solving process. Through our specialised training programs, we will help your teams learn how to use the A3 template more effectively, as well as how to interpret data visualisations quickly and accurately – enabling them to take action swiftly when required. Our experienced coaches will also share insights from industry experts on how best to integrate countermeasures into standard operating procedures (SOPs) and process maps, keeping up-to-date with industry trends in order to stay ahead of the competition.
By leveraging Leanscape’s expertise in A3 Problem Solving, you can rest assured knowing that your team is in good hands. Our team is dedicated to providing you with the support needed for successful implementation so that you can achieve sustained performance improvements over time.
100% Free Fundamentals of Lean COURSE
Take our free course.
JOIN FOR FREE
Lean Six Sigma Yellow Belt Certification Course
The implementation of A3 Problem Solving provides a comprehensive framework for organisations looking to successfully address complex problems in an efficient and cost-effective manner. By breaking down the problem-solving process into seven distinct stages, users can structure their approach and track the progress of their countermeasures over time.
In order to ensure successful implementation, organisations should dedicate time towards training their teams on how to use the A3 Problem Solving Tool and A3 template. This will give everyone a solid foundation for carrying out future problem-solving activities more effectively, as well as provide insights into the effectiveness of certain countermeasures over time.
Through Leanscape’s specialised training programs, you can ensure that your team is fully equipped with the necessary skills to successfully adopt and incorporate A3 problem-solving into all areas of your business. Our experienced coaches are committed to helping you develop a culture of continuous improvement within your organisation – providing guidance through every step of the process.
Final Thoughts
The A3 approach is an invaluable tool for unlocking the power of improvements within any organisation. By leveraging its structured framework and cyclical learning approach, businesses can remain agile and responsive to ever-changing conditions, allowing them to navigate change more successfully and emerge stronger than ever before. Ultimately, this makes Toyota’s A3 problem-solving process one of the most effective ways to ensure long-term success in today’s fast-paced and competitive market.
Stay current with our latest insights
- Lean Six Sigma Yellow Belt Course
Our Training Courses
- Lean Six Sigma White Belt Course
- Lean Thinking Business Course
- Lean Six Sigma Green Belt Course
- Lean Six Sigma Black Belt Course
Yellow Belt Course
View all courses, recent articles, 2024 recommended reads for transformative thinking, 10 best books on agile, scrum and design thinking, the ultimate guide to lean and manufacturing: boosting efficiency and productivity, 10 best management books for leaders and change makers, mastering software development agile: a practical guide, the most popular tools of six sigma, view all articles, green belt course, other articles, 5 essential problem-solving strategies every business leader should know, understanding the difference: project sponsor vs project champion in lean six sigma, why the fmea is a great tool for all project managers, 2 proportion test: the basics, a comprehensive guide to integrating hoshin kanri into strategic planning, principle 1: use long term goals to drive short term decisions, financial services company takes bold steps to improve productivity, what is the 1 proportion test in lean six sigma, small steps, big gains: the case for incremental improvement, issue #10 | never start with a solution, managing the project: 10 tips for project managers, what is lean six sigma.
- | lean , lean thinking , problem solving , toolkit , tools
Related Articles
The box-cox transformation: what it is and how to use it, principle 7: visual management in lean | the 3 second rule, benefits of online business courses, project management key skills: a lean perspective, 10 reasons operational excellence deployments fail, lean six sigma online courses.
FREE COURSE | YELLOW BELT | GREEN BELT | BLACK BELT | MASTERCLASS | WORKSHOPS
Lean Accelerator Progam
A Lean Six Sigma Green Belt Masterclass
LSS Green Belt
The ultimate fast-track for future leadership
LSS Black Belt
Become an expert in change management and complex problem-solving.
Subscribe to Newsletter
Keep up to date to the latest insights, courses, training, webinars and more. Join our newsletter today.
Lean Accelerator Program
Discover the power of problem-solving, 15 min per day | 3-months | only €999 | learn from experts.
- Project management
How to use Toyota’s legendary A3 problem-solving technique
Georgina Guthrie
February 21, 2020
If you came home one day and found your kitchen taps on full-blast and your house full of water, what’s the first thing you’d do? Grab a bucket and start scooping — or turn off the tap?
When it comes to problem-solving, many of us take a rushed, reactionary approach rather than fixing the issue at the source. So in other words, we see the water, panic, and start scooping. If this sounds like something you’ve done recently, then don’t feel too bad: when the pressure’s high, we often jump towards the quickest fix, as opposed to the most effective one.
This is where the A3 technique comes in. It’s a problem-solving approach designed to efficiently address the root cause of issues.
What is the A3 technique?
The A3 technique is a structured way to solve problems. It’s part of the Lean methodology , developed by Toyota back in the mid-’40s. This doesn’t mean you need to implement a Lean way of working to take advantage of this process — it can work as a standalone exercise.
Granted, A3 isn’t an inspiring name, but the story of its origins is actually pretty interesting. Rumour has it that Taiichi Ohno, inventor of the Toyota Production System, refused to read past the first page of any report. In response, his team created A3 address and summarize problem-solving on one side of A3-sized paper. The A3 technique played a huge part in Toyota’s success and all kinds of industries have since adopted it. Here’s how to get started.
How to solve a problem with A3
The first thing to remember is this: A3 is collaborative and relies on good communication. It’s not something you should do by yourself.
There are three main roles involved:
- Owner (that’s you or someone under your charge)
As you’ve probably guessed, these aren’t roles that already exist in your company; you must create them for the purpose of this process. Here’s what they mean.
The owner is responsible for leading the exercise. They are the lynchpin between the two other roles, fostering good communication and keeping documents up to date. It’s tempting to think of the owner as the head of this trio, but that’s not true: everyone is equal here.
The mentor is someone with solid problem-solving experience. It’s their job to coach the owner and steer them towards finding a solution. It’s not their job to find the answers themselves.
And finally, there are the responders . This is someone (or a group of people) who have a vested interest in the outcome of the A3 project. Responders might include the client, stakeholders, or managers. A potential problem here is gaining access to them: if you work somewhere with a strict hierarchy — and you’re somewhere near the bottom of that structure — you may face challenges. There’s no easy way around this. Essentially, you need your organization to support this way of working and make it easy for you to access those at the top if needed.
How to create an A3 report
True to its origins, the A3 report is a one-page document. It typically contains 5-7 sections that systematically lead you towards a solution. These are the most commonly used steps, but feel free to modify them.
- Background: Explain your project in a few sentences, including its context.
- Problem statement: Explain the current problem. You can use process mapping to see the different tasks that surround the issue. This isn’t essential, but it will make it easier for you to locate the root cause.
- Goals: Define your desired outcome, and include metrics for measuring success. You won’t know everything until you reach the end, so you may find you need to come back and refine stages 1-3.
- Root cause analysis: This is a big stage of the process. You need to work out what you think the root problem is. You can use different methods to help you here, including 5 whys or a fault tree analysis .
- Countermeasures: Once you’ve worked out your root cause, you can start proposing solutions.
- Implementation: Work out how you’ll implement these solutions, including an action list with clearly defined roles and responsibilities. Project management software is a useful tool here because it can help everyone on the team track each other’s progress in real-time.
- Follow-up: Using your metrics for success, decide whether the problem was solved. Report your results back to the team/organization. In the spirit of Lean (continuous improvement), you should go back and modify your plan if the results weren’t as expected. And if they were, you should make this process the new standard.
Final thoughts
A3 is an efficient, methodical way to solve problems at their source. When issues rear their head, rising stress can lead people to panic. Having a clearly designed system in place to guide you towards a solution minimizes the chances of people settling for a ‘quick fix’ or failing to act altogether.
Beyond being a guiding light in times of pressure, A3 is a great team-building exercise because it encourages individuals to work together towards a common goal — across all areas of the organization. Combine this with collaborative tools designed to help teams track progress and work together more effectively, and you’ll be unstoppable.
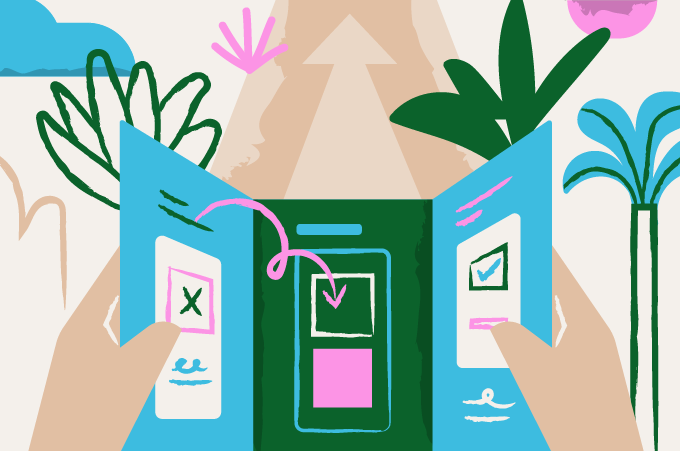
How to do a value stream map with Kanban
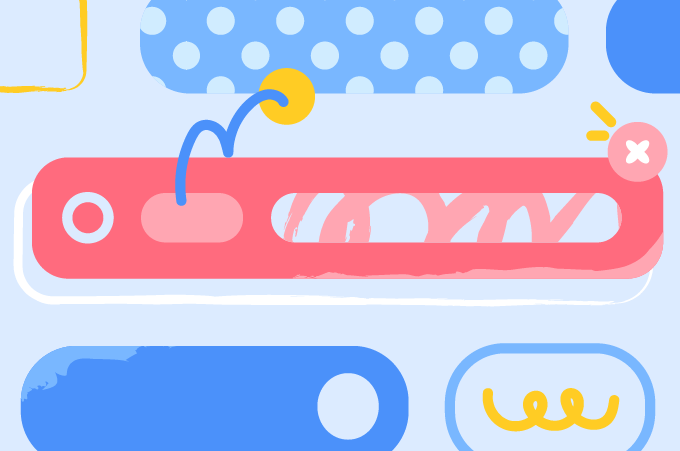
Solve problems like a pro with Root Cause Corrective Action
Subscribe to our newsletter.
Learn with Nulab to bring your best ideas to life
Lean Manufacturing Tools
Lean manufacturing tools, techniques and philosophy | lean and related business improvement ideas.

A3 Problem Solving | A3 Root Cause Analysis
Problems are inevitable, no matter how hard we plan and what precautions we take, they will eventually creep up and bite us. Rushing in and trying to fix the problems quickly, however, rarely seems to truly make these problems go away. Often, they come back time after time. The reason for this is that we fail to use a methodical approach to identify the true root causes of the problems and fail to put in a robust fix that will prevent the problem reoccurring.
A3 problem solving is one easy way to put in place a process that will help you to solve problems permanently as well as making improvements to your processes.
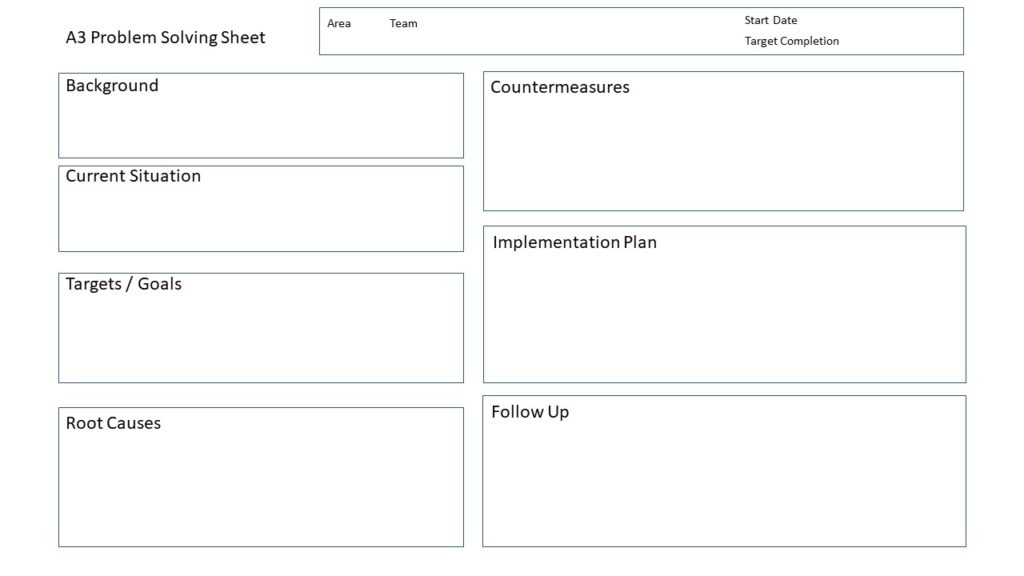
What is A3 Problem Solving
As with many things from Toyota, A3 problem solving attempts to make things as simple and as visual as possible. A3 refers to the paper size used for the reporting and all the process is contained within the confines of this single sheet of 11” by 17” paper. Some suggest that the reason for the single piece of paper is down to the rumored refusal of Taiichi Ohno to read any more than a single page of any report.
There is nothing magical or revolutionary about the process either. It simply follows the Deming’s Plan-Do-Check-Act Cycle or PDCA. It is also very similar to other processes and layouts that other companies have used over the years such as Ford’s 8D process for problem solving.
The effectiveness of the form however lays more in the attitude of the teams implementing the A3 process than the form itself. Problems are opportunities to improve what you are doing and should never simply be seen as just a “problem”.
A3 problem solving sheets are not going to be a magic wand that you can wave over your problems to solve them. Without a dedicated team to follow the process they are unlikely to help you.
The A3 Problem Solving Process
The A3 root cause analysis process is usually broken down into 7 steps, some break it down into 8 or 9, however the total number of steps and what they are called are not important as long as you follow the idea behind them. The steps follow the PDCA process and take you through a logical step by step route to clearly identify:
- What is the problem
- Why we need to fix it
- What is the actual root cause
- How we will contain the problem in the short term
- Plan how we fix the root cause
- Confirmation that the countermeasures fix the issue
- Changes to standardized work to fix the issue permanently
- Share any changes within the company
Often these steps are broken down under the following headings on the A3 worksheet:
Current Situation
- Targets or Goals
Root Cause Analysis
Countermeasures.
- Implementation Plan
This is what should be considered and detailed within each section:
- What is the actual issue that you are looking to correct?
- How does it impact the business objectives? Why do we need to fix it?
It is always best to take your team to where the problem is occurring to see the problem firsthand. Talking about something in a remote location is never going to be as effective as actually observing at the Gemba (Workplace).
The team should carefully detail the problem. This should cover all relevant information such as how often something happens, when, where, etc. Depending on the complexity of the issue it may be necessary to collect data in the form of graphs and control charts or to conduct process mapping exercises to understand what is happening.
Targets / Goals
What does the team see as the ideal solution to the problem? What are we going to achieve? Your objectives should be clearly stated, and a time frame agreed so that all can agree on what you hope to do through your team.
There are of course many ways that you can arrive at the root cause of your problems depending on the complexity of the problem that you face. The right quality improvement tools should be selected and used from Pareto charts to fishbone diagrams or the 5 whys.
Ensure that your A3 root cause analysis comes up with agreed reasons for your problems. Remember, that there are often multiple causes that may need to be fixed.
Once you have your root cause(s) identified you can get to work to brainstorm the changes that you need to make to fix the problems. Remember that all fixes should aim to achieve the goals that you have identified earlier in the process.
Action Plan
This is your plan of action to fix the problem that you have identified. This plan should be detailed and include what is to be done, who is responsible, and of course when it will be done by. You should also consider the expected outcome from each action so that you will have a clear idea of whether the action has had any effect on your issue.
Once the plan has been detailed it should be implemented effectively by the team.
Too often teams will stop at the plan implementation stage. They make the changes that they have suggested and then fail to check if those actions have been effective. You must verify the effectiveness of your actions to confirm that they have fixed the root causes that you have identified. Otherwise the problems could easily return.
If the changes have not managed to fix the problem, then the process needs to be revisited. The team needs to work through the cycle once again to see what they have missed and to make alternative plans to fix the problems.
Changes should be made permanent if they are found to be effective through changes to standardized work and other procedural documentation.
Teams should also share what they have learned and implemented within the company. Often there is the opportunity to mirror the changes made to prevent issues occurring in other parts of your business.

Why Use A3 Reporting
The A3 reporting format does not have to limited to simply problem solving. Toyota use it for a number of things such as status reports, improvement suggestions and proposals. Other companies have developed similar reports for things such as coaching. Your imagination and business needs are your only limitation.
The A3 lean process is highly flexible and provides you with a highly visible way to communicate everything from your problem solving to continuous improvement initiatives. Used well with trained and dedicated teams it can really make a huge difference to your company.
Related posts:
- Top 50 Lean Tools | Comprehensive List for Lean Manufacturing and Service
- VSM Value Stream Mapping
Post navigation
Leave a reply cancel reply.
Your email address will not be published. Required fields are marked *
Save my name, email, and website in this browser for the next time I comment.
CAPTCHA Code *
- Agile Education Program
- The Agile Navigator
A3 - Root Cause Analysis
The A3 is a tool for identifying root causes to deep problems and building consensus on how to remedy them.
Estimated time for this content : 20 minutes Audience : Scrum Masters facing a reoccurring impediment Suggested Prerequisites : Retrospective , Muda
Upon Completion you will:
- Have a base-line knowledge of lean principals as practiced by Toyota
- Know how lean and agile practices utilize the Plan Do Check Act cycle
- Understand the pre-cursors to doing root cause analysis
- Understand how to perform root cause analysis
- Be able to complete a step-by-step process for the A3
The A3 tool was pioneered by Toyota to document and address problems with their production process. Anyone at Toyota can initiate the process and they do it for almost all problems they encounter. To capture their analysis, they use the largest sheet of paper that fit into a copy machine, the A3 or Tabloid (two 8.5x11 sheets side-by-side.)
The A3 process is based on the Plan, Do, Check, Act , or PDCA Cycle. To initiate the A3 all the stakeholders should gather. The owner is the person who is responsible for ushering the process through to its end and the mentor is typically a high-ranking executive who can help implement the actions that result from the process. An A3 is meant to simplify complex problems, so using just one large sheet of paper follow the example in the slides. The title should be something catchy so it is easy to remember and to refer to.
A3 Template
A3 Template in Google Docs (Opens in a New Tab) A3 Problem Solving Template v1.2 (April 2015) by Henrik Kniberg and Tom Poppendieck License: Creative Commons Attribute 4.0 International Original link: http://www.crisp.se/lean/a3-template
Step 1: Plan
The first cell is used to describe the background of the problem. It is important that all stakeholders participate in this phase so everyone involved has a clear idea of what the problem is. The A3 is a process so even if the problem is obvious, it is important to discuss it and make sure everyone is literally on the same page. Often, the background is a macro problem that affects multiple parts of the Scrum process.
With the background established, the discussion moves on to establishing the current conditions. This will be a list of symptoms like decreased Velocity or poor morale. It is important to make sure that the group is able to include some Metrics in this cell. Loss of revenue is always helpful because it gets management’s attention but any number of metrics will do. The important part is that they are precise and measurable.
Next, the group should decide on what the ideal outcome will be when the problem is solved. (The ideal state is similar to an Acceptance Test or Definition of Done for a Product Backlog Item .) Metrics are helpful here as well. It is important to have a well-defined target condition because it will help align all stakeholders around a common vision.
The last part of the planning phase is root cause analysis (see video) and this is the core of the A3. Establishing the problem and what life will be like after the problem is solved is relatively easy, agreeing on what the root causes are may involve some uncomfortable truths.
It sounds very high minded, but quality root cause analysis actually requires channeling your inner five-year old. The technique is called the Five Whys . Basically, the group needs to start with the most obvious problem and ask why. Here is an example:
Sprints are failing. “Why?” A: People think that the Team is lazy. “Why?” A: Because morale is low. “Why?” A: The Team is getting mixed messages from the Product Owner. “Why?” A: The Product Owner is getting conflicting orders from two managers. “Why?” A: The organization incentivizes competition rather than cooperation.
The point of the exercise is to get at least five layers deep into any problem. Five layers is a general rule of thumb. Root causes can be found three or seven layers deep. It is really important to invest a lot of time here. Often the stakeholders think they have arrived at a few root causes only to have to repeat the process later. Another good rule of thumb is that once the group thinks it has discovered the root causes, they should then put in again as much time as they’ve just spent. It is important to be exhaustive. (There are other root cause analysis techniques. A variety can be found here .)
There will likely be multiple root causes to a problem. In the above example, the Product Owner role has broken down, managers are probably talking to the team outside of their scope and the organization’s incentives are flawed.
Finding a root cause is a bit of an art. Here are a few characteristics to help guide your process: first, a root cause will resonate with stakeholders. Second, root causes also tend to be actionable, meaning that the group will have an idea how to approach the specific challenge. And, third it will have a certain amount of specificity. In the above example, “people think the Team is lazy” doesn’t have any granularity. Further inquiry helped pinpoint a more detailed root cause.
In Systems Theory, if multiple solutions are implemented at once, it is impossible to trace the effect of each. Therefore, it is important to implement only one solution at a time. The A3 is a living document so the group should continually note the results of each solution implemented and update the A3 as conditions change.
Step 3: Check
It is important to confirm that the countermeasure has the ideal state identified in step one. In order to know if the countermeasure worked, it is important to have objective criteria to judge it against. That is why having metrics in the current and target conditions makes for a better A3. It may be that multiple countermea sures are necessary to achieve the ideal state.
Step 4: Act
Hard Truths
When an A3 fails it is usually because the group didn’t delve deep enough into the problem or that the problem was beyond the ability of the team to solve or recognize. Solving the root cause can be the end result of a successful A3. However, that’s not always the case. A successful A3 can show that the root cause is beyond the ability of the organization to change like in the above example where there wasn’t enough market demand for the product. A good A3 can reveal deep challenges within the organization like conflicting core values, poor leadership or a critical lack of resources. The A3 isn’t a silver bullet; rather it’s a tool to bring transparency to dysfunction. How the stakeholders handle the dysfunction is their responsibility.
Paper: Lean as a Scrum Troubleshooter
Related Posts via Categories
- Blending Lean and Agile for True Transformation
- Leaders Leveraging the OODA Loop for Value Stream Management
- The Effort Estimation Matrix – A Tool for Estimating Agile Story Points
- Scrum@Scale for Organizational Success: Insights from a Scrum of Scrums Master
- Scrum Inc. Webinar with JJ Sutherland and Jeff Sutherland
- SI Consulting Chats: Why Agile Transformations Fail
- Decoding Agility: Asset-Based Prioritization
- Debunking Sustainable Pace with Dr. Jeff Sutherland
- The Shifting Landscape of Business Agility and Consulting
- Scrum@Scale: Navigating Modern Challenges
Simpler® Consulting

Lean into A3 thinking to improve over the long term
Published by devuser on september 15, 2023 september 15, 2023.

What is A3 thinking?
A3 thinking is a problem-solving methodology, not just a summary on A3-size paper. Used effectively, A3 thinking helps teams look at a problem and make decisions about solutions in a new way.
Simpler’s A3 problem-solving process expands the traditional six steps to nine. On A3 paper, this would appear as nine boxes.
1.Reasons for action

2.Initial state
3.target state, 4.gap analysis, 5.solution approach, 6.rapid experiments, 7.completion plan, 8.confirmed state, 9.lessons learned, the magic happens in boxes 6 and 9, boxes 6 and 9 can rewire thinking and create opportunities, experts in a3 thinking can help you maximize your potential.
Our experts meet you where you are. Let us tailor a plan that transforms your business and helps you solve problems effectively throughout your organization. Ready to get started? Contact us today.
Related Posts

Simplify your AI journey with the AI ladder
Using the AI ladder can simplify your AI journey.When it comes to AI, you know just enough to be dangerous. How can you expand your knowledge and use AI to your advantage? No one was Read more…

Enhance your Operational Excellence System by Adding Technology to Value Stream Analysis
Previously, I shared some thoughts regarding integrating a technological perspective into the outputs from the Value Stream Analysis (VSA) process.

Adapt to constant challenges with a business improvement strategy
The manufacturing skills gap in the U.S. could cause as many as 2.1M unfilled jobs by 2030. How many of those job openings will be in your organization?
- What is Lean?
- Our Approach To Lean
- History & What We’ve Done
- Lean Research
- About Capability Development
- Login / Sign up
Sign up and join the community
Email address *
Subscribe to our newsletter
Please select all the ways you would like to hear from us Email
Your personal data will be used to support your experience throughout this website, to manage access to your account, and for other purposes described in our privacy policy .
Home > A3 Practical Problem Solving – Step 3 Problem Analysis & Breakdown
A3 Practical Problem Solving – Step 3 Problem Analysis & Breakdown
28th June 2021 - Peter Watkins
This video blog will give you an inital overview to A3 Practical Problem Solving – Step 3 Problem Analysis & Breakdown. This is an 8 part mini series on the A3 8 Step Practical Problem Solving method. We have already covered:-
Step 1 – Problem Clarification
Step 2 – Containment
A3 Practical Problem Solving – Step 3 Problem Analysis & Breakdown
The video is presented by Peter Watkins a Senior Coach at LEA , who explains the key points using a Visual Teach Poster.
The top half of our Teach Poster focuses on the Purpose, Process & People of Practical Problem Solving. This is covered in our FREE Skill Level 1 course on A3 Practical Problem Solving – ACCESS HERE
This blog series concentrates on the lower half of the Visual Teach Poster , which covers the 8 step method based on Toyota Business Practice.
Play the Video Overview for A3 Practical Problem Solving – Step 3 Problem Analysis & Breakdown
Video is played best when watching in Full Screen Mode
Key Learning Points from the Video
What is the purpose of analysising & breaking the problem down .
Break down the problem to the correct level , so you can focus and tackle one significant contributing causal as the “Problem to Pursue”
How to breakdown a Problem
Start with the GAP
Get the Data b y going to the actual thing (e.g. parts, people, systems, activities)
Here you will find actual data to build actual facts
Understand the work – learn how the work is done
Example of Step 3 – Problem Breakdown & Analysis
use the 7 Problem Solving tools to help you visualise & breakdown the data
Breakdown Data – Look at the data in terms of WHAT, WHERE, WHEN, WHO
Prioritise – Use data to find the biggest contributors to a problem. We use ‘inch wide mile deep’ thinking to focus on the area of the problem with the biggest impact on it
Identify the Point of Cause
Identify the Point of Cause – Don’t guess Focus the problem solving activity on a specific point in the process
Work from the back of the process and look for evidence of the problem – where does the problem start?
State the Problem to Pursue
By breaking down the gap and finding the point of cause you can then Summarise the Problem to Pursue in a short statement
You cannot tackle everything ! You need to focus and select a portion of th e gap that is manageable to tackle
Establish the Direct Causes
Establish Direct Causes of the Problem to Pursue
For each Problem to Pursue we must establish the Direct Cause(s)
Direct Cause(s) have a Direct Effect on the occurrence of the Problem
Use Fishbone diagram as a framework to think about all the potential causes for the problem to pursue
Fishbone Helps to capture ideas from group in a structured way and systematically eliminate / prove them with PROVEN DATA & FACTS
Data will show which are direct causes – there might be more than one
The identified direct causes are what you take forward for root cause analysis using 5 why’s in step 5
Helpful hints on this step:-
Consider these 3 points when breaking down the problem :-
- Go too deep on a problem breakdown and the impact on GAP may not be worth the effort ! (check back)
- Keeping the problem at a high level and not breaking it down enough makes it hard to establish any real direct causes, rootcauses and countermeasures (too vague and wide).
- Check by asking if we eliminate these direct cause(s) how much will the GAP be closed? (this will also help you with step 4 target setting).
Try to tackle only one Problem to Pursue at a time ! You can always come back and take the next highest contributor.
Problem solving is about taking action, It better to get one thing done now to impact the GAP.
Make sure you prove out all your potential direct causes highlighted on your fishbone with data / facts for effect . Otherwise its just an opinion !
A lot of the time data and facts might not be available to verify that your potential cause have a direct effect on the problem to pursue
You may need to set up trials and experiments which will support investigating your causal confirmation
Want to succeed at A3 Problem Solving ?
Join us on the 7th July at 3:30pm UK time for our Lean A3 Problem Solving webinar. During the webinar we will walkthrough the Purpose, Process & People, then 8 step approach to A3 problem solving – all based around our 8 step Practical Problem Solving Teach Poster . Find out more information about the webinar HERE , or you can purchase your tickets below:
Related Courses and Recommended Reading
We have gathered together some links below for selected courses, books and articles if you want to learn more about A3 Problem Solving.
- Construction
- Manufacturing
- Public Sector
- Retail & Hospitality
- Supply Chain
- Capability Development
- Lean Leadership
- Lean Principles
- Management System
- Process Improvement
- Product Development
- Tools & Techniques
- Transformation
- Demand Analysis
- Flow Costing
- Lean & Green
- lean certification
- Lean Digital
- lean learning
- Lean Summit
- Lean Thinking
- Lean Transformation Framework
- Managment Routines
- People Capability
- Problem Solving
- product development
- Purpose Process People
- Rapid Problem Solving
- Standardised Work
- Supply Chain Management
- Teach Poster
- Training Within Industry (TWI)
- UK Lean Summit
- Value Stream Analysis
- Value Stream Mapping (VSM)
- Value Streams
- Visual Management
Problem-Solving A3
Problem-solving is essential for any organization to improve their processes, products, and services. A3 problem-solving is a structured approach that helps teams identify and analyze the root causes of problems and develop solutions. This paper describes the A3 problem-solving process, its benefits, and how it can be applied in different industries.
Introduction
Problem-solving is a critical activity every organization must undertake to improve its operations and meet its objectives. However, problem-solving can be complex and challenging, especially when dealing with complex issues requiring a systemic approach. A3 problem-solving is a structured problem-solving approach that helps teams identify the root causes of problems, develop solutions, and implement them effectively. This paper provides an overview of the A3 problem-solving process and its benefits.
The A3 Problem-Solving Process The A3 problem-solving process is a structured approach that follows a step-by-step process to identify and solve problems. The process is named after its paper size (A3), a standard paper size used in many countries. The A3 problem-solving process consists of the following steps:
Step 1. Problem Clarification
1.0 background.
- Background information about the situation
- You and your responsibilities
- The scope of the subject/problem
- Why am I tackling this problem, and why is it important?
- Where do the Ideal Situation and Ultimate Goal come from?
- What is the impact on the business?
1.1 Gap Analysis – GAP is visualized
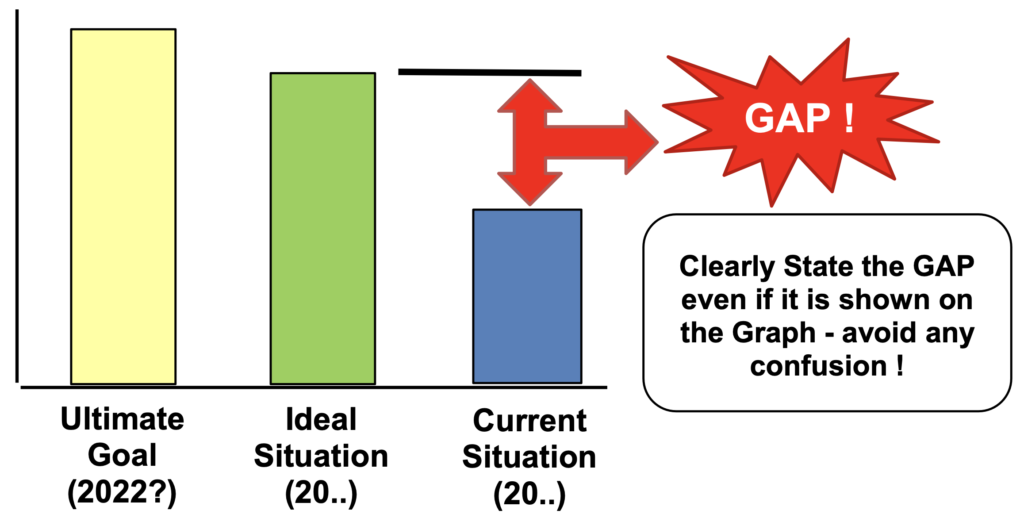
1.2 Problem Statement
Ultimate goal:.
Where do you want to be, e.g. 3-5 yrs? Where does this figure come from?
Ideal Situation:
Where should you be?
Current Situation:
Where are you now?
Problem Statement:
The GAP between the Ideal and Current Situation. How much is this worth?
Step 2. Containment
Containment activity (5w, 2h):.
- What : What is the activity?
- When: When is the start date and timing?
- Where: Where will the activity be done?
- Who: Who will be involved (name, title)?
- Why: What is the purpose of the activity? How: How will it be done?
- How much: What do you expect to achieve?
Ideal Situation
Visualize: is the containment working.
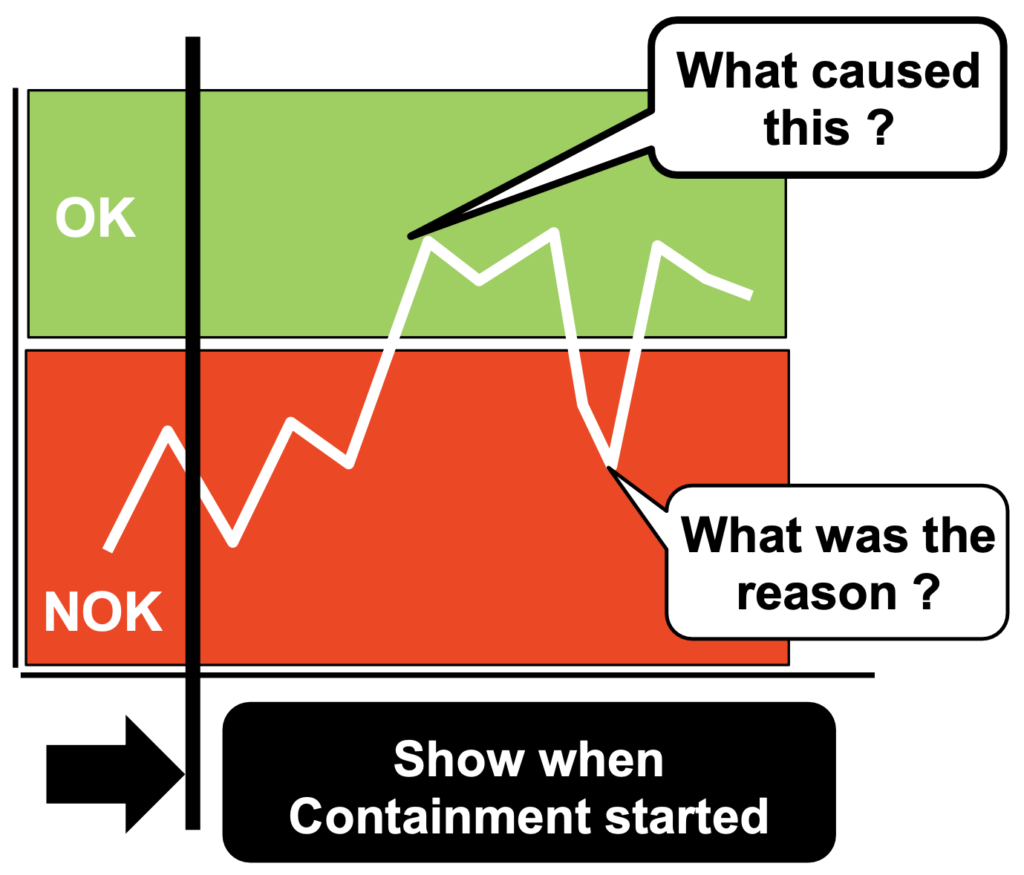
What actions have you taken during Containment?
Show some of the actions taken, and what have you discovered and learnt from the Containment activity?
- Screenshots
What is the impact of Containment on the Gap?
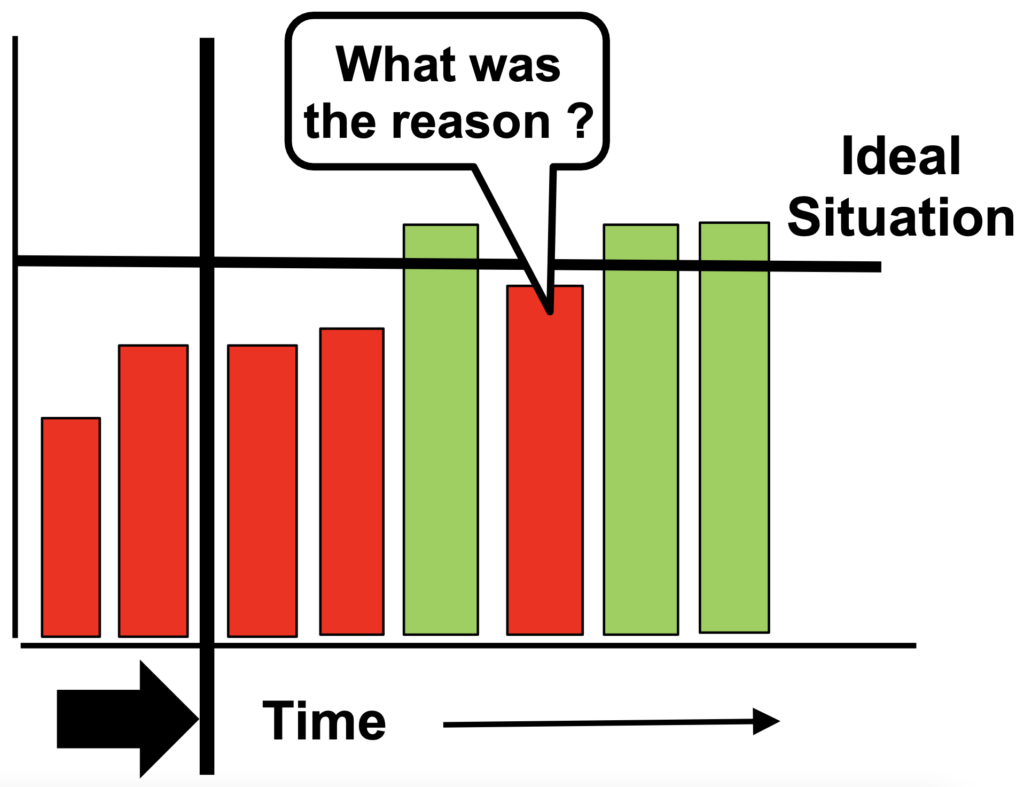
Step 3. Problem Analysis and Breakdown
Breakdown the current situation or gap.
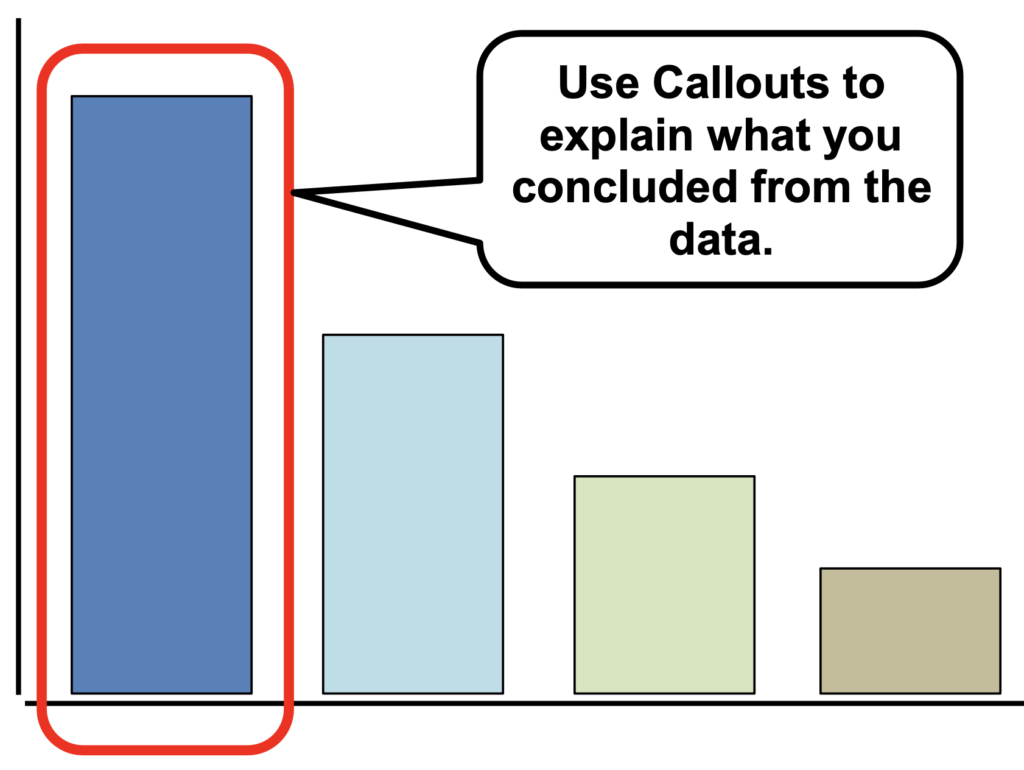
‣ 7 QC Tools
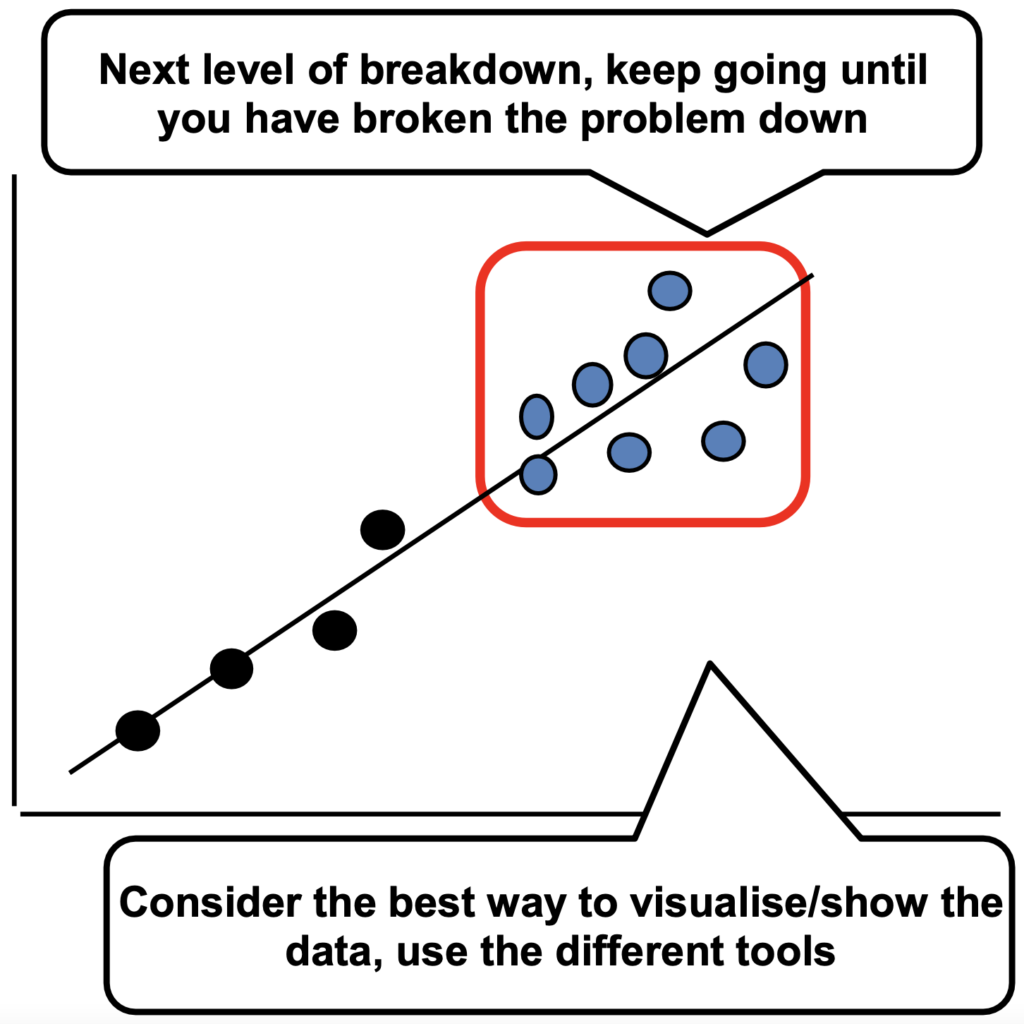
Point of Cause (PoC) – Where is the problem happening?

Point of Cause key points:
- Walk back through the process steps – Go and see for yourself
- Find where the problem happens
- Prove with data
Establish the Direct Causes – What switches the problem ON and OFF?
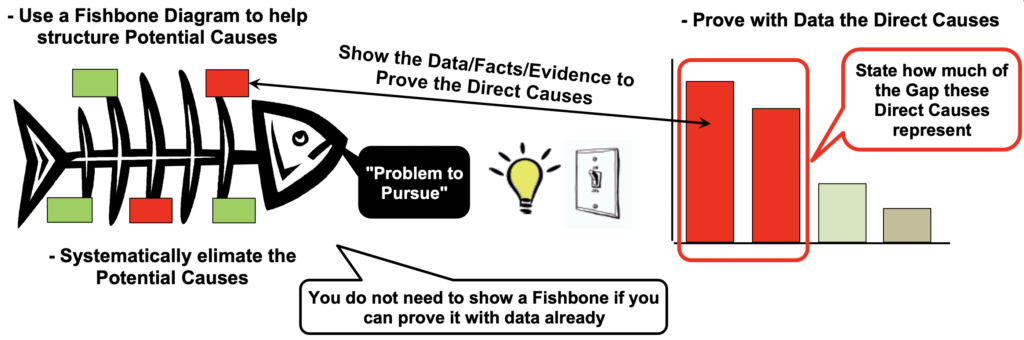
Use data and facts to determine the following:
- What is the problem you are going to tackle?
- When is it happening?
- How is it happening?
- How much of the gap is it contributing to?
Breakdown of critical points:
- Pareto 80:20 rule
- Collect data if you don’t have it
- Use Problem-Solving Tools to analyze the data
- State what the data is telling you!
- A short, simple statement of the problem
- What, Where, When, How, How Much
Direct Causes key points:
- Cause/Effect relationship on the problem
- Light switch test! ON/OFF
- Prove with data or by experiment
- They are the first “Why” in Step 5
Summarise the Direct Cause(s)
- Direct Cause 1
- Direct Cause 2
- How much of the Gap do they represent
Step 4. Target Setting
Smart target statement.
“By solving the Problem to Pursue by this Date, I will Close the Gap by this much” Short, simple statement
Always quantify the $, € of the Target and potential look across benefits if initially small.
Visualize your Specific Target Evolution
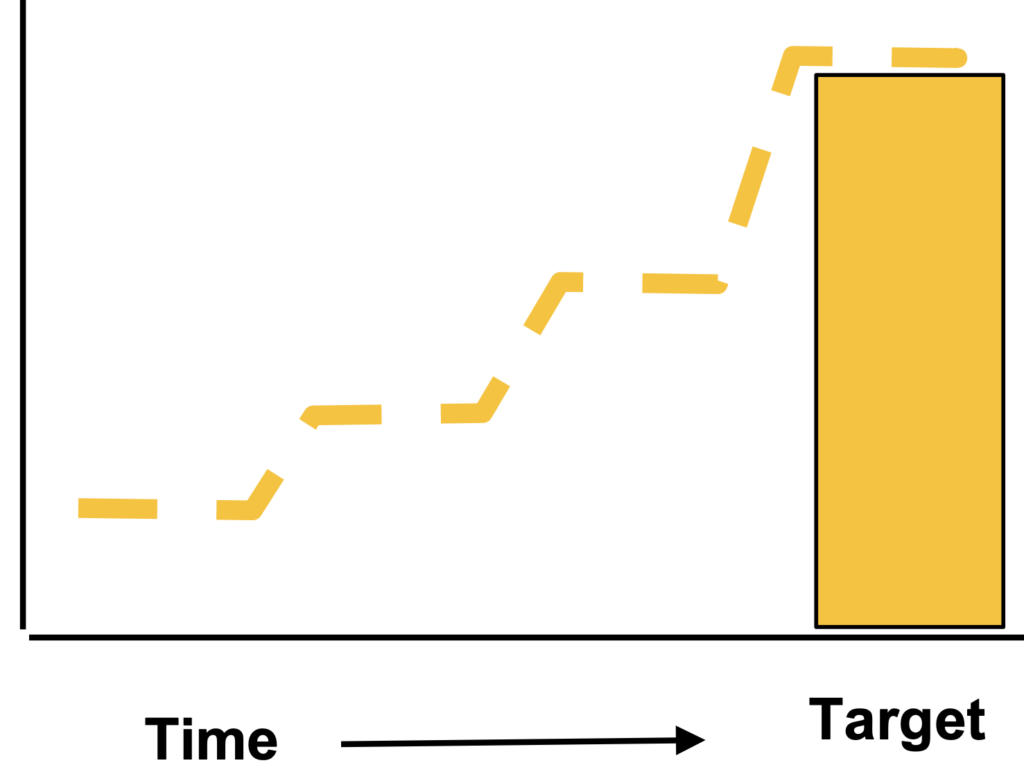
Impact on the Gap

Step 5. Root Cause Analysis

Step 6. Develop and Plan Countermeasures

Step 7. Check results
Result vs your specific target.
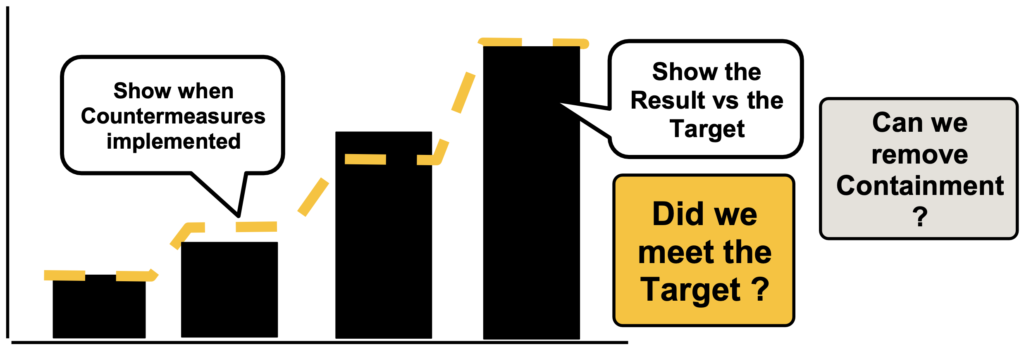
Step 8. Standardize and Share
Standardize.
- What did you learn?
- What are the next steps/actions?
- Sustainment: Standardise Countermeasures, update Management Routines
- Update EOS process documents, FMEAs, Control Plans, and other documents…
- MUST be actions (what, who, when)
- How will YOU share the learning points?
- Can we apply the result anywhere else inside your area and outside?
- To similar Products, Processes, Departments, Plants, Regions, Divisions…
- How can we leverage the benefit?
Application of A3 Problem-Solving
The A3 problem-solving process can be applied in manufacturing, healthcare, and service industries. For example, the A3 problem-solving process in manufacturing can improve quality, reduce defects, and improve productivity. In healthcare, the A3 problem-solving process can reduce medical errors, improve patient outcomes, and streamline operations. In service industries, the A3 problem-solving process can be used to improve customer satisfaction, reduce costs, and improve service delivery.
Source: Lean Enterprise Academy
Template here
Updated on May 2, 2023
- More By sensei
- More In Process Excellence

Mastering Gemba Walks: A Step-by-Step Guide for Continuous Improvement

Unlocking the Power of FMEA: Essential Steps for Process Reliability

Your Ultimate Guide to the 2024 CSA Standards Updates

Review of “Document Everything” by Rick Hermanussen

The Essentials of Six Sigma: A Deep Dive into Waste and Value Analysis

Essential Product Performance Metrics for Business Growth

How do you ensure that your quarterly Objectives are both ambitious and achievable?

A Comparative Analysis of Popular Continuous Improvement Methodologies: PDCA, DMAIC, A3, and 8D
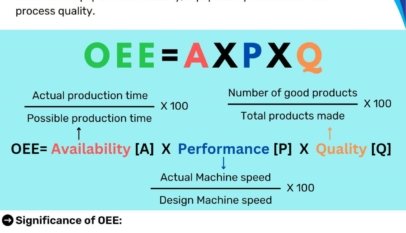
Optimizing Manufacturing Efficiency with Overall Equipment Effectiveness (OEE)

Management View on Lean, Flow, Standard, Continuous Improvement, and Respect: A Comparative Analysis
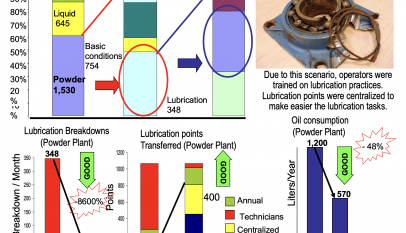
Planned Maintenance Case Study, Food Processing Plant
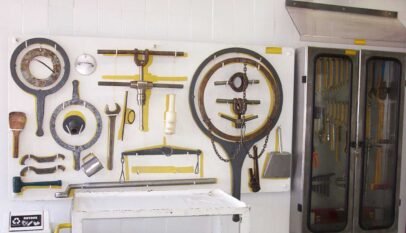
Shadow boards reduce waste
Very good understanding of concepts
Leave a Reply Cancel reply
Your email address will not be published. Required fields are marked *
Most Popular
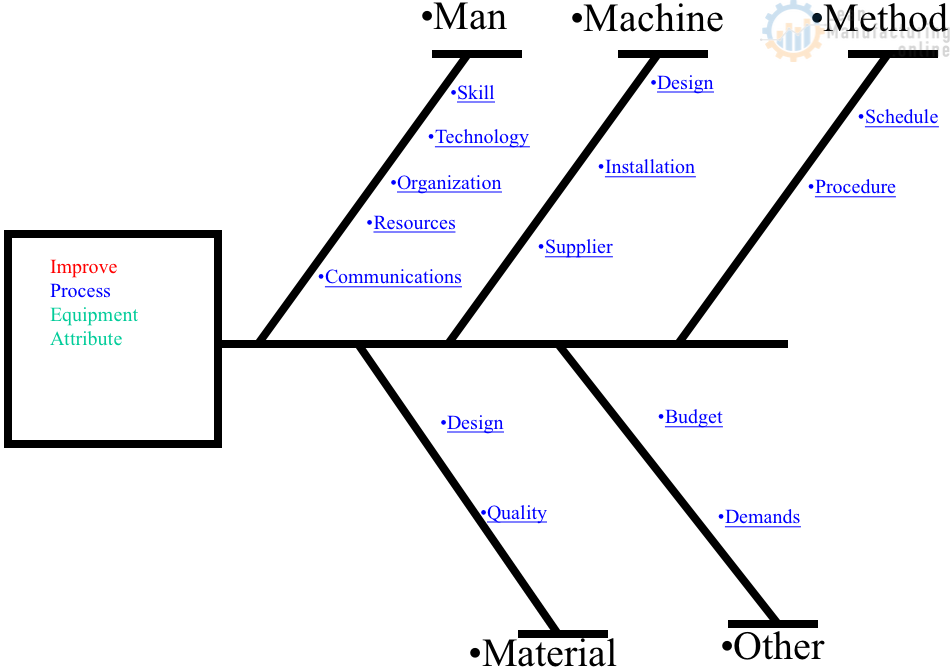
4M Analysis Process
The purpose of this procedure is to define the steps to do a 4M …
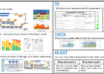
PDCA – A Process Approach

OPL – One Point Lesson Template – Free Download
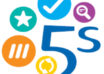
5S Audit Checklist and Report

Why-Why Analysis
Blog Search
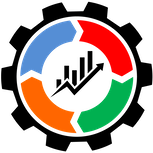
- Terms of Use
- Privacy Policy
- About Our Ads

COMMENTS
Problem-solving is an important component of any business or organization. It entails identifying, analyzing, and resolving problems in order to improve processes, drive results, and foster a culture of continuous improvement. A3 Problem solving is one of the most effective problem-solving methodologies. A3 Problem solving is a structured and systematic approach to problem-solving that ...
The A3 is a problem-solving tool that encourages a collaborative and systematic approach to problem-solving. The term A3 comes from the paper size which is roughly 11″ by 17″ and used to map out the problem-solving process on a single sheet of paper. The A3 paper size is used as a single-page constraint that ensures the team focus on the ...
A3 Thinking in Action. In the dynamic landscape of business and continuous improvement, A3 thinking has emerged as a powerful tool, providing a structured and systematic approach to problem-solving.
This process of solving problems while creating better employees—A3 analysis—is core to the Toyota management system. An A3 report guides the dialogue and analysis. It identifies the current situation, the nature of the issue, the range of possible counter- measures, the best countermeasure, the means (who will do what when) to put it into ...
The A3 Report is a very useful problem solving and continuous improvement tool. It was first used by Toyota and is quickly gaining popularity in industry today. Companies must start to view problems as opportunities for improvement. The A3 Report format allows the entire problem identification, clarification, analysis and resolution steps to be ...
A3 thinking involves the practice of consolidating the problem, analysis, countermeasures, and action plan onto a single sheet of paper, commonly an A3-sized sheet. This brief document serves as a summary of the project at hand and is regarded as a valuable storytelling tool for project communication. Utilizing the A3 approach doesn't require ...
Mind the Gap. Breaking down your problem situation is a two-, possibly three-step process. First, consider the nature of the unwanted condition or occurrence at its location in the process as the starting point to look to the end of the process to see if your problem is related to a performance gap in delivery to the customer and/or the business.
The A3 problem-solving approach is a powerful tool used to identify, analyze and solve issues. It consists of a comprehensive template which can be used to effectively unlock improvements and gain deeper insights into various situations. This article will discuss how this versatile technique can be used to help individuals unlock their ...
The A3 'problem' (a gap, in this case, between the intended purpose and actual usage) echoes the broader challenge facing widespread adoption of any proven TPS methodology: moving from lean tools to lean management, according to Jim Womack. As he notes, "Tools—for process analysis and for management—are wonderful things.
Like using a detailed blueprint in construction, A3 problem solving provides a detailed plan to build a solution. The A3 methodology is a structured approach we use in Lean Six Sigma (LSS) to address and solve complex problems. Many of these issues are related to waste reduction through analysis of the 8 Wastes and Continuous Improvement.
In the Lean Operating System, we achieve operational excellence by: Defining our standards. Continuously compare our operations against those standards. Engaging in aggressive and rigorous problem-solving when there is any deviation from the standard. Step 1: Identify the Problem. Step 2: Set the Target.
The A3 technique is a structured way to solve problems. It's part of the Lean methodology, developed by Toyota back in the mid-'40s. This doesn't mean you need to implement a Lean way of working to take advantage of this process — it can work as a standalone exercise. Granted, A3 isn't an inspiring name, but the story of its origins ...
The A3 Problem Solving Process. The A3 root cause analysis process is usually broken down into 7 steps, some break it down into 8 or 9, however the total number of steps and what they are called are not important as long as you follow the idea behind them. The steps follow the PDCA process and take you through a logical step by step route to ...
A3 problem-solving guides a user through several steps. With a name derived from the size of paper originally used at Toyota, the A3 user first describes the problem—a gap between desired performance and current performance. Next, the user figures out why there is a gap, then proposes a solution, and plans the steps to apply the solution.
The first cell is used to describe the background of the problem. It is important that all stakeholders participate in this phase so everyone involved has a clear idea of what the problem is. The A3 is a process so even if the problem is obvious, it is important to discuss it and make sure everyone is literally on the same page.
An Example Problem Solving A3. How important is the A3 template vs. the thinking behind the template? Look at the Problem Solving Flowchart ... Step 4: Root Cause Analysis Start Step 2 Narrow the GAP Line of Sight Quantifiable Quantifiable Not Quantifiable Ask WHY left to right and THEREFORE right to left test Cause and Effect Logic
The magic happens in boxes 6 and 9. To get more out of A3 problem solving, teams can zero in on steps 6 and 9 at a deeper level. Steps 6 and 9 give people the freedom to redefine potential solutions as often as necessary. Step 6, rapid experimentation, enables teams to fail fast and small. This approach provides opportunities for learning and ...
Develop Countermeasures O O D A. a. Develop potential countermeasures. - Tools and philosophies from Lean, TOC, 6 Sigma and BPR as appropriate. b. Select the most practical and effective countermeasures. c. Build consensus with others by involving all stakeholders appropriately. - Communicate, communicate, communicate.
28th June 2021 - Peter Watkins. This video blog will give you an inital overview to A3 Practical Problem Solving - Step 3 Problem Analysis & Breakdown. This is an 8 part mini series on the A3 8 Step Practical Problem Solving method. We have already covered:-. Step 1 - Problem Clarification. Step 2 - Containment.
However, not every problem requires the level of complex root-cause analysis that a typical problem solving or strategic A3 entails. Below are two other tools and processes that can be used for less complex problems. 2. Localized PDCA problem solving: Target, Actual, Gap, Causes, Experiment
July 26, 2022. As she details how to problem-solve using the A3 methodology, a veteran lean coach explains why it's essential to understand that completing an A3 problem-solving is a thinking process, not a form-filling-out process. In my experience, too many lean practitioners still approach the A3 report merely as a template with several ...
A3 problem-solving is a structured problem-solving approach that helps teams identify the root causes of problems, develop solutions, and implement them effectively. This paper provides an overview of the A3 problem-solving process and its benefits. ... 1.1 Gap Analysis - GAP is visualized. 1.2 Problem Statement Ultimate Goal: Where do you ...
A3 Exercise - Part 1 (35 min) Part A - (25mins) Write a problem statement for your team. Decide on scope; what is included vs. excluded. List appropriate team members who can work together to solve the problem. Part B - (10min) o 2- 3 min report out from each team.